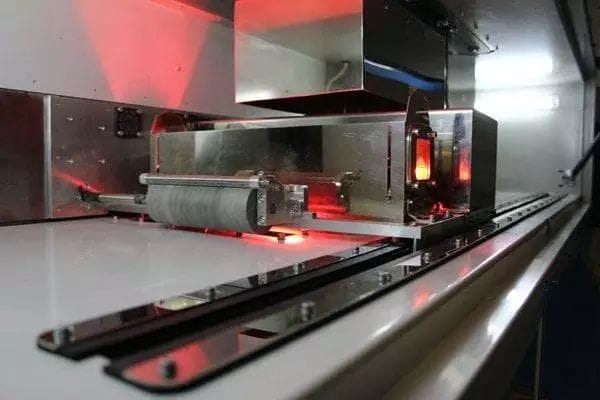
After emerging from its early days in the lab and entering the commercial space, High Speed Sintering is taking another developmental leap with the formation of Xaar 3D Limited, a company dedicated to commercializing fast and scalable 3D printing technology.
Giving a boost to the newly formed business is an investment by Stratasys, one of the largest players in the additive manufacturing industry.
To learn more about the new firm and its ties to Stratasys, we spoke to the director of 3D for Xaar 3D, Neil Hopkinson.
Bringing High Speed Sintering to Xaar
With its development beginning in the early 2000s, High Speed Sintering started in the labs of Loughborough University and, later, the University of Sheffield. Hopkinson and his team looked to create a technology that could take on mass manufacturing methods like injection molding.
The process sees an inkjet printhead deposit black infrared radiation absorbing ink onto a bed of thermoplastic powder, which outlines the desired shape, before an infrared lamp heats the powder and causes the particles to fuse.
In 2016, Hopkinson carried the technology over to UK-based industrial printhead manufacturer Xaar PLC, where he acted as its director of 3D Printing. There, the team continued developing HighSpeedSintering machines under its newly formed 3D Printing business unit, while Xaarās core business continued manufacturing industrial printheads to sell to original equipment manufacturers.
āAs both business units progressed, it got to the point on the High Speed Sintering side where we thought it made sense to maintain focus by setting up a new business dedicated to High Speed Sintering,ā Hopkinson said. āThis gives us a bit more flexibility. It just made sense to make a new venture that was purely focused on High Speed Sintering machines.ā
High Speed Sintering technology will continue to be licensed by Loughborough University and printheads will continue to be sold by Xaar PLC to Xaar 3D Ltd, along with other companies, including large-scale 3D printer manufacturer voxeljet.
Read more at ENGINEERING.com