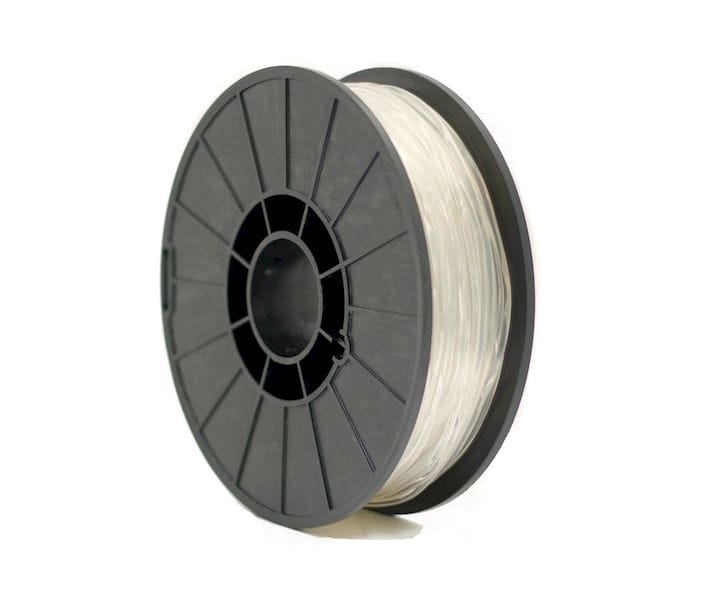
Essentium announced a highly unusual flexible filament material for 3D printing, called “TPU 80A”.
To understand what they’re doing, you have to first understand what’s going on inside a flexible filament chemically.
The molecules in a flexible material have very loose bonds between each other, creating the very flexibility desired. However, for 3D printing there is another requirement: thermoplasticity.
This is the property of being able to be repeatedly softened and hardened, as is done by the hot end of a filament-based 3D printer. Indeed, the filament itself was extruded in a similar manner to be created in the first place.
But many flexible materials are actually thermosets, which, as opposed to thermoplastics, cannot be resoftened and rehardened.
How do flexible filaments exist, then? It turns out they are co-polymers, a mix of flexible molecules and thermoplastic rigid materials. The ratio of rigid thermoplastic content determines the degree of flexibility of the resulting combination material.
But that said, flexible filaments are notoriously difficult to print, for a couple of reasons.
First, Bowden-style extruders push filament through relatively long tube paths towards the hot end of a 3D printer. A flexible filament simply cannot withstand the load along those lengths and bends. Imagine trying to push a section of cooked spaghetti through a straw and you’ll understand the concept here.
This is why Bowden-style machines almost always cannot easily 3D print flexible materials, although some can if the input filament is wider: 2.85mm vs the more standard 1.75mm diameter.
Another solution is to use a direct feed extruder, where the “push length” is only a few millimeters, removing much of the possibility of bending along the way.
The second issue is that when the flexible filament eventually hits the hot end – assuming you’ve solved the feeding problems – there is some back pressure as the material enters the smaller diameter nozzle. If the pressure is sufficient, the flexible material simply bends outwards.
A typical solution for this issue is to 3D print very, very slowly. This gives more time for the filament to soften and thus reduce the back pressure. But it makes prints take a very long time to complete.
These constraints cause a limitation of how soft a filament can be and still be successfully printed, and thus we find there are only certain types of flexible filaments on the market.
Essentium now says they’ve developed a filament that is softer than any previous material, and that it can be successfully 3D printed on many devices, at least those allowing third party filament. They say:
It is the most flexible filament currently available for 3D printing that is able to print on any open platform.
How is this done?
It turns out they’ve made a kind of composite filament that is made of a thin layer of relatively rigid – but still flexible – material on the outside of the filament, and the core is a far softer flexible material.
When this combination material hits the hot end, it’s all mixed together and extruded as a single material that has mostly the more flexible component.
It’s a brilliant solution to an old problem in 3D printing. With this material it should now be possible to 3D print more flexible objects with a reasonable expectation of success, and even print at speed.
This amazing material, TPU 80A, is currently available for sale in Essentium’s online store in 750g spools, both 1.75mm and 2.85mm formats at a cost of USD$95 each.
Via Essentium