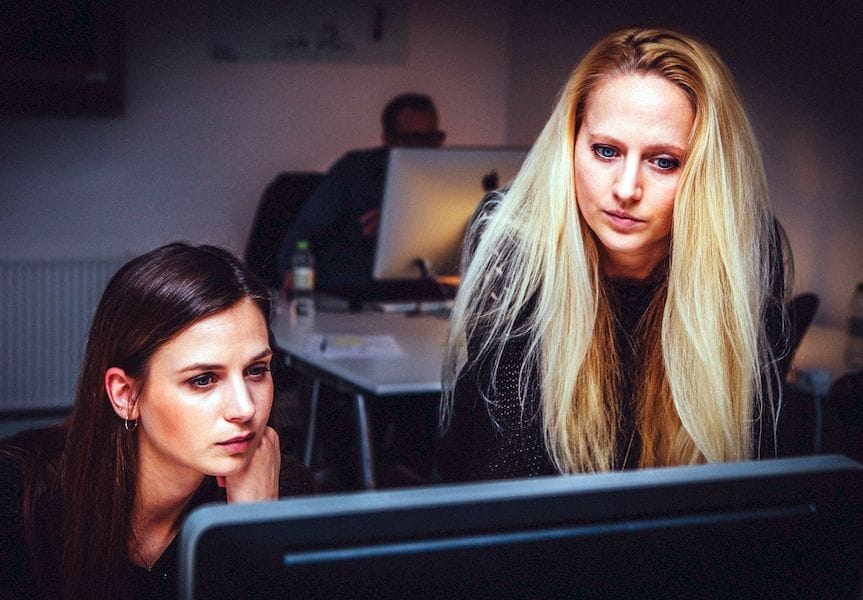
I’ve been reflecting on the history of 3D printing and had some thoughts about ease of use.
There are two dimensions of 3D print ease of use in the technology: the design of 3D printable objects, and the actual operation of 3D printers.
Let’s look at the latter first.
Years ago when desktop 3D printers first emerged the operational usage scenario was not particularly pretty. At that time there were several industrial machines well established in the market, as well as a few startup companies marketing extremely basic desktop 3D printers.
The industrial machines were somewhat reliable in terms of hardware; that is to say, the frequency of print failures was not outrageous due to deficiencies in the machines’ designs. That was not true of the early desktop machines, whose reliability was notoriously bad. I recall times when you’d be lucky to get one third of your prints done properly.
This was because the early desktop machines were made with cobbled together components and machine designs were primitive as startup engineers were still learning what worked well and what did not.
Software for machines of that era was also troublesome. Industrial machines used interfaces that were little different than the cryptic CNC equipment interfaces for other equipment that were designed by hardware engineers – who are not user interface engineers. They were (and in some cases still are) hard to learn, but easy to use once learned.
Desktop software was rudimentary to say the least, with plenty of buttons and lots of troubles. But persistent users somehow made it all work.
But that persistence is not a characteristic of the general population, and thus spelled the end of the notion of selling 3D printers to the consuming public.
Over time these have all changed.
Industrial machines have become more reliable through a series of gradual hardware innovations by many companies. Competition has pushed this as well.
Desktop machines have also benefited from competition, with today the leaders being those marketing machines that tend to be the most reliable. Reliable wins, even if it costs.
User interfaces have dramatically improved for both industrial and desktop equipment. Desktop machines leveraged powerful software tools and touch screens to create interfaces that are akin to photocopiers that almost everyone is familiar with, making it far easier to operate the machines.
Similarly, some industrial 3D printer manufacturers have produced slick software tools to manage 3D print operations. I’m particular fond of 3D Systems’ new 3DXpert system that can perform almost all required tasks in a highly graphical manner and integrates directly with all their recent equipment.
So we see that both hardware and software interfaces have dramatically improved over the years.
But what still struggles is the design aspect. 3D design is a learned skill requiring considerable training and (sometimes) expensive tools.
Multiple efforts have attempted to simplify the process of 3D design, but end up creating Minecraft-like systems that are fun but largely incapable of creating functional objects that fit into our world of parts.
Some have attempted to bypass the design problem by offering large repositories of pre-made objects from which non-designers could select desired items. These do work, but seem to fall into either “Not enough choice” and “Too many things; I’m lost!”
Other efforts have blended the repository into the design process by offering customizable 3D objects. Interfaces are sufficiently simple to allow almost anyone online to tweak some sliders and input boxes to create a unique item.
However, these have mostly focused on fashion items, and less on functional objects. We need a lot more “pedestrian” object generators to handle common office and household object needs. Where is the “Clamp Generator”? How about a “Tube Adapter Generator”?
I do believe the “Wizard” approach will likely succeed at the end, but for now these customizable solutions seem disjointed and hard to find. I believe there is a market opportunity for someone to make a new kind of 3D repository that is SOLELY filled with basic customizable objects. If such a thing existed we would find far fewer objects, as each customizable item would represent thousands of different possibilities.
One single service holding a collection of functional generators could become the go-to site for quick, useful printable 3D models. I’m hoping someone will eventually attempt to do this.
Will you?