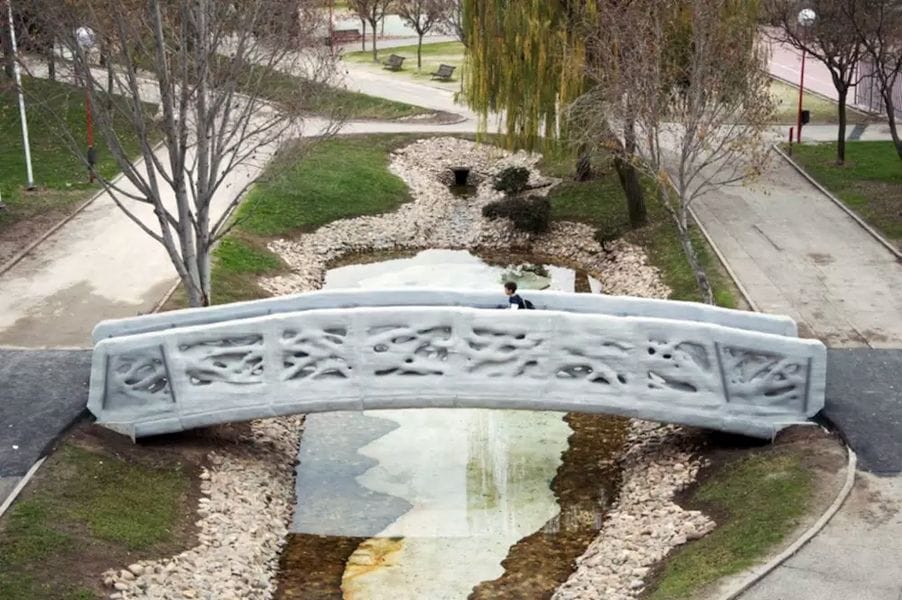
Additive manufacturing (AM) has begun to affect nearly every industry, from healthcare to aerospace, making it possible to create unique geometries with unique properties.
One industry where 3D printing’s impact is at an even more nascent stage in construction. There are firms and research groups exploring the use of 3D printing as a building technology, but additive construction is still so young that its exact purpose and benefits remain speculative and unclear. Why, other than for sheer novelty, squeeze concrete out of a nozzle to fabricate a building when you can rely on traditional methods?
Here we explore the various technologies currently being developed in additive construction to understand what the purpose, benefits, drawbacks and hurdles are to the technology.
Large-Scale Binder Jetting
Among the first large-scale 3D printers for construction was the D-Shape 3D printer, made up of a 6m x6m aluminum frame and 300 nozzles that spray a binding agent onto masonry material, such as sand. While D-Shape has printed some large-scale objects, including a 3m x 3m x 3m sculpture, the company has struggled to realize the vision of its founder, Enrico Dini.
Dini’s largest construction project to date, a 12-meter-long, 1.75-meter-wide pedestrian bridge, was performed in conjunction with ACCIONA and the Institute of Advanced Architecture of Catalonia (IAAC). The bridge is made up of concrete powder micro-reinforced with polypropylene and reflects a parametric design meant to optimize the distribution of material, while minimizing waste through the use of recycling raw material during the manufacturing process.
Rick Rundell, technology and innovation strategist, startup mentor and senior director at Autodesk, explained that the process used to fabricate the bridge might be more accurately described as 2.5D printing.
“Any of the companies that are making a go at 3D printing concrete really are kind of 2.5D printing concrete. They’re making custom panels by printing on a flat surface and giving it some dimension. Those panels are then intended to be tipped up and made into something,” Rundell said. “The railings of the bridge were 3D printed flat and tipped up, and then the bridge was cemented into place.”
3D Printing Metal
A pedestrian bridge is a good place to start when venturing into the world of 3D printing publicly used structures. Not as large as a single-family home, but not as small as an art object, a bridge can actually serve a useful purpose while demonstrating additive technology’s potential.
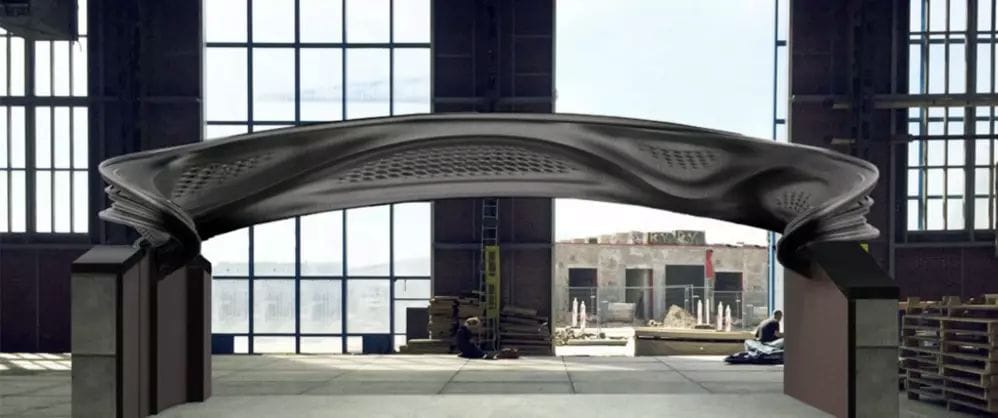
An additive construction that has received a great deal of attention is the MX3D Bridge, from Dutch firm MX3D. The project was unveiled in 2015 with an ambitious video depicting two industrial robotic arms standing on either side of a canal and welding a metal bridge until the two devices met in the middle.
Several years have passed since then, but the bridge is nearing completion. In the process, however, MX3D realized that the vision promoted in its initial video could not be created exactly as envisioned. Instead of printing the bridge live, on-site, the bridge has been fabricated off-site in a facility, where the industrial robotic arms would not be subjected to the elements.
“The MX3D Bridge project is a classic moonshot project,” Gijs van der Velden, CEO of MX3D, told engineering.com. “This means that we knew what we wanted to achieve, namely print a 12-meter bridge in stainless steel. We also knew that a lot of innovation was needed to bring the early stage technique up to the required level. We understood that our plan might have to be changed due to city permits or regulations. And it was clear that engineers, material researchers and other unforeseen external factors were going to change the original project plan.”
Read more at ENGINEERING.com