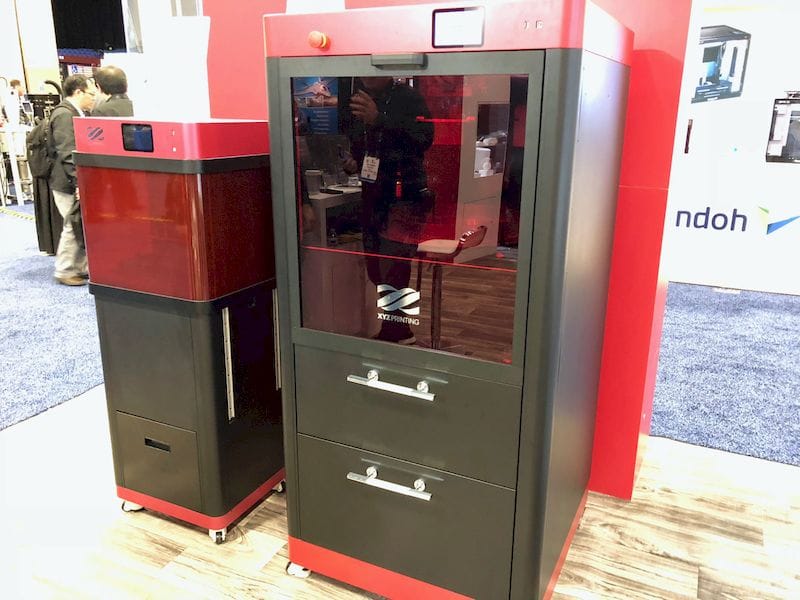
XYZprinting has developed a style of resin 3D printing system I have not seen previously.
The Taiwan-based company is quite prolific in producing seemingly dozens of different and similar 3D printers of all types, and so it’s always difficult to find the new developments. Their cryptic numerical product names don’t help either.
But hidden in the back of their stand at Rapid+TCT we found a machine with an interesting feature. The MfgPro380 xP is targeted at manufacturers, and is a resin machine, one of several in XYZprinting’s product line.
So far it’s not surprising. This machine uses a 405nm laser system to illuminate photopolymer resin to create solid objects. The machine has excellent XY resolution (0.130mm) and a great Z resolution (0.025mm). They provide a full complement of resins: standard, flexible, rigid, tough and high temperature. The MfgPro380 xP is fully networked and ready to participate in a workshop with multiple users. A 5” touchscreen provides easy operation.
And the build volume is 380mm diameter by 300mm tall.
Wait, “diameter”?
Resin 3D printers virtually always quote build volumes in three dimensions, X, Y and Z. What’s going on here?
The MfgPro380 xP has a cylindrical build volume, much like you’d see on a delta-style filament extrusion 3D printer. This is highly unusual, perhaps because many resin 3D printers use a DLP light engine, which illuminates in a rectangular pattern of pixels. But the MfgPro380 xP uses a laser to trace over a circular surface.
Lasers do not have to follow that pattern, so why do this?
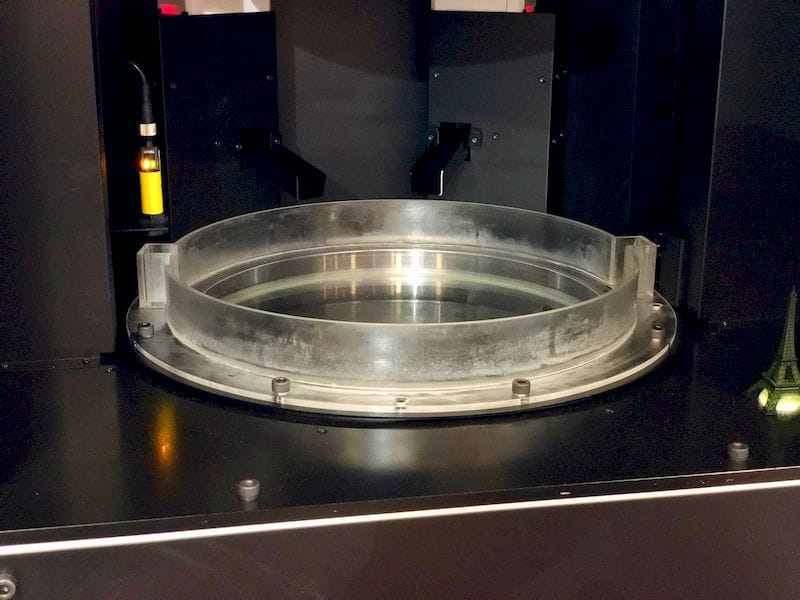
It has to do with the peeling process.
Peeling is the process required by all resin 3D printers that illuminate the resin through the transparent bottom of their resin tank. The laser energy passes through the tank bottom and interacts with the nearby resin to solidify it. That’s what’s desired, but a side effect is that sometimes the solidified resin adheres slightly to the bottom of the tank.
To engage the next layer of 3D printing, most resin 3D printers perform a “peel” operation in which the newly solidified layer is slowly peeled off the tank bottom and fresh resin is allowed to slosh in. This peeling movement is typically done by slowly lifting the print bed from one side and tipping towards the other, just like you’d peel adhesive tape off of a table.
This is where the magic comes in.
The MfgPro380 xP does not lift to do perform the peel. Instead, it rotates!
The resin tank, shown at top, rotates, which releases the newly solidified layer from the tank bottom and at the same time introduces fresh resin. I suspect this is a faster process than traditional peeling, which occupies a significant amount of print time on most machines.
That’s why the print volume is cylindrical: because it must rotate during printing.
This approach looks very promising and I’m wondering if it will catch on. Perhaps XYZprinting has patented it, however.
We’re told the MfgPro380 xP will be available in 2019, with some beta testing being done by the end of this year.
Via XYZprinting