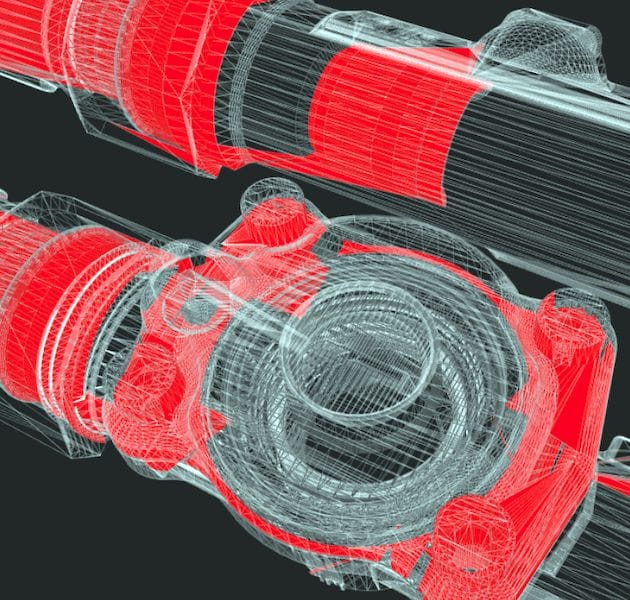
We’ve been covertly testing a new cloud-based 3D model repair service that is now available for testing.
Broken 3D models are all too often still encountered, in spite of the improvements in the 3D CAD systems that generate them. In many cases the flaws may be invisible to the eye, but oh-so troublesome to 3D printing.
Your print may simply fail during the printing operations. Or worse, actually much worse, you may introduce a hidden flaw into your printed part that may not be discovered until later.
Thus it is always in your interest to ensure your 3D models are in proper condition before you attempt to 3D print. I am often in the habit of running 3D models through a repair system even if I don’t suspect anything is wrong, and often issues are encountered. They may not always be critical but sometimes they may be.
I am therefore always on the lookout for new 3D model repair options. There are several new ones on the market now, and it looks like there is another one coming soon.
Our friends at Avante Technology, who recently have developed some interesting engineering filaments and a high performance 3D printer controller board, have been secretly working on a new 3D model repair service that’s cloud-based. It seems to be somewhat based on their previous Emendo standalone repair tool.
And now they want everyone to give it a try so they can work out the bugs. Avante Technology’s Bob Zollo explains in detail what they’re developing and how you can get involved today:
It is common knowledge the STL files often contain errors that can degrade the quality of a 3D print.
What is not so well known is that the source application and/or applications that were used to create the STL may create different types of errors that require different repair techniques to get the best results.
A CAD generated STL file of a part created by a single user may require conventional repair methods to create a “watertight” file for printing or milling on a CNC machine.
But if the part was designed by a team of engineers who each contributed a section of that part to create a single STL, different types of errors may exist. For example, there may be tiny voids between two components that are not visible on a computer screen.
More challenging problems may occur when components of an STL are created on different software applications. In addition to intersecting and overlapping triangles where two components meet, different precision settings in the source applications may create triangles of a different scale. This expands the potential problems where components are combined.
Components created in 3D rendering applications can sometimes be accidentally created with zero thickness. This can create serious problems for repair algorithms if the component is not properly connected to other components.
This is why hybrid, or “mashup” files are often not properly repaired using conventional software such as Netfabb, which was not designed for dealing with this type of hybrid STL.
Avante Technology, who has been in the STL file repair business for several years, has developed a new cloud-based repair architecture designed to deal with the growing number of compound and hybrid STL files. To help users get a clear picture of what is wrong with a particular file, a high performance 3D rendering engine allows the user to rotate, zoom in and out to view every problem triangle and its location to identify the cause of each problem. Repairs can be made from a variety of automated tools to address a broad range of STL files.
The soon to be released Emendo™ Cloud STL analysis and repair service is now available as a public Beta Test, for anyone to try their range of repair methods on any number of files at no charge, and with no confidentiality required.
The company is seeking problem STL files that have failed in other repair software. The public beta test is available now and runs through 18 May. It can be found here. For more information contact: info@avante-technology.com