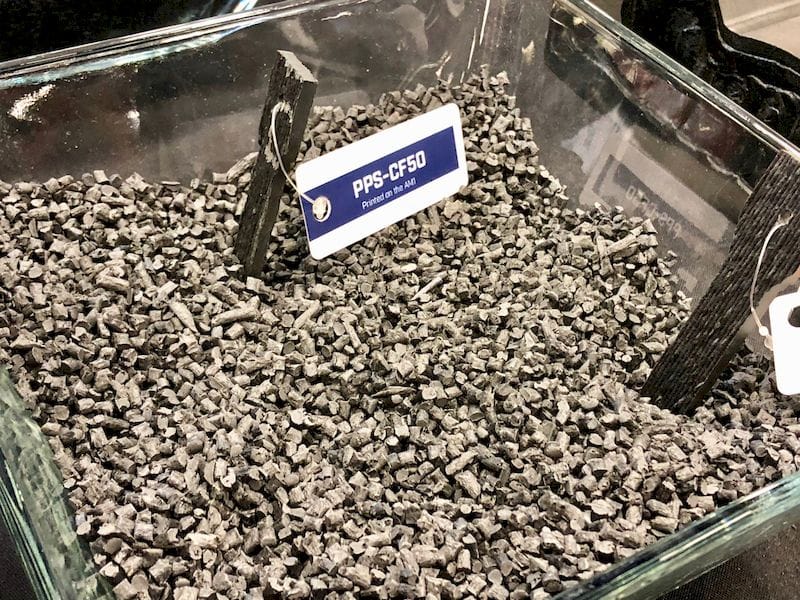
Pellets are slowly becoming a more popular 3D printing material, but there is one surprising reason this is so.
Typical 3D printers use filament, resin or powder as input materials, but in some cases pellets are used instead of filament.
This change must be by design, as the mechanisms used for extruding from pellets are quite different than from filament. Filament is essentially a packaging of pellets that is optimal for the simplified filament extruders of today.
Filament is desirable because it provides a means for precise control of the amount of material extruded: a stepper motor can, with each step, push a specific amount of material to the hot end. In pellet scenarios the heated material is more like a viscous fluid, leading to a more difficult problem in pushing precision amounts to the hot end.
But filament has several disadvantages, including cost: it is literally made from filaments. Pellets (and often a colorant) are poured in a hopper, heated and carefully extruded to form the filament, which is received on a large take-up spool. This process creates the filament, but also adds cost. Typically the cost per weight of filament could be as much as 10X because of this transformation.
This cost advantage attracts those 3D printer operators who perform a lot of printing and thus use a lot of filament. However, pellet extruders are hard to find.
One place they are found occasionally is in the large-format 3D printers. This niche market within 3D printing addresses industries that require large prototypes, sometimes up to or even exceeding a meter on a side.
The problem with large-format 3D printing is that the cost of filament becomes excessive. Remember that the volume increases by the cube of the dimension, so if a 10cm cube use X amount of material, a 20cm cube would use 8X. And a 100cm cube would use 1000X. We’re talking orders of magnitude more material for some of these large prints.
Because of this we’ve seen the major large-format 3D printer manufacturers begin to offer 3D printers available with optional pellet feeding systems.
But there is another reason for the use of pellets.
Filaments are always delivered on spools, typically today with 750g or 1kg weight of materials wound around them. While this size is quite useful for desktop machines 3D printing 150mm-sized objects, it is highly problematic for large-format 3D printers. These machines first usually require amounts of material for a print that exceeds these capacities. That implies the need for operation intervention to swap spools, raising the possibility of error or even print failure. Not good.
Secondly, large format 3D printers are usually tuned for faster printing to reduce the seemingly endless print durations on some large prints. This means they consume material far faster, and would slurp through a 750g spool far faster than a desktop machine might do. Again, this adds to the need for operator intervention.
What’s the solution here? Well, you’d think the answer would be this: bigger spools!
Some manufacturers and filament suppliers have attempted this, producing and using spools of 2kg or even a massive 8kg in weight. That does somewhat solve the problem, but it turns out there is a limit.
In such filament 3D printers, the filament is pulled from the spool by the extruder motor. Usually the spool is mounted on a freely turning placement and the strength of the motor can turn the spool during printing.
However, we’ve heard that some manufacturers have found that there is an effective limit to how big a spool can be properly used in these situations. It’s possible for the weight of a very large spool is too much for the extruder to reliably pull and turn.
Remember that the key to a quality print is highly consistent material flow. If the flow slows slightly because of the extruder straining to rotate the spool, that’s not good.
This is the real reason why all large format 3D printers will eventually move exclusively to pellet operations: unattended large, long duration prints cannot be done with filament spools.
Thus we will see these companies continue to introduce and improve pellet extrusion systems.
Hopefully their inventions will eventually make their way to desktop machines as well, whose operators surely would prefer lower material costs as well.