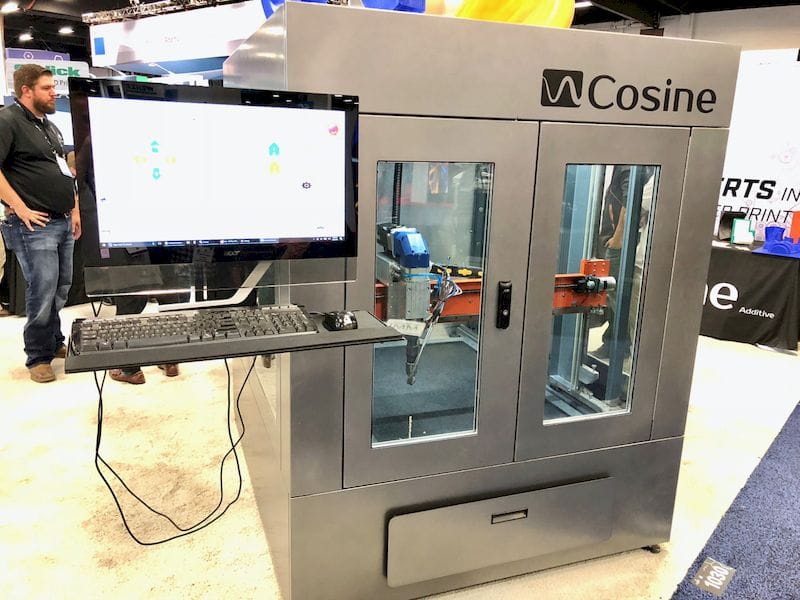
Cosine Additive is one of the few 3D printer companies that produces large-format devices.
They’ve been doing so for years, and we’ve covered both their initial machine, and more recently a complex upgrade to a then-unusual dual independent extruder setup.
We recently bumped into them at Rapid+TCT and got an update on their new features. Two of them are quite interesting.
The first development is that they’ve deployed a pellet extruder. This is increasingly being adopted by large-format 3D printer manufacturers as it provides a means for clients to use far less expensive material than filament. In fact, filament is simply processed pellets, so it is guaranteed to be more expensive than pellets in every case.
Cosine Additive explained that their pellet system can achieve flow rates 20x faster than conventional extruders. This is obviously a key advantage when 3D printing large objects, which normally would take many hours, well days, to complete. Printing at potentially 20x the speed could be significantly in terms of machine throughput: you could produce – and sell – many more products in the same elapsed time.
They say the cost of materials tends to be about 5X less expensive when using pellets, which is also a significant advantage. No spools are required; just pour the pellets of choice into the hopper and print.
The second innovation is perhaps of more interest. Cosine Additive, like several other thermoplastic extrusion machine manufacturers, is experimenting with metal 3D printing processes.
The Cosine Additive process for 3D metal printing involves, coincidentally, their pellet extruder.
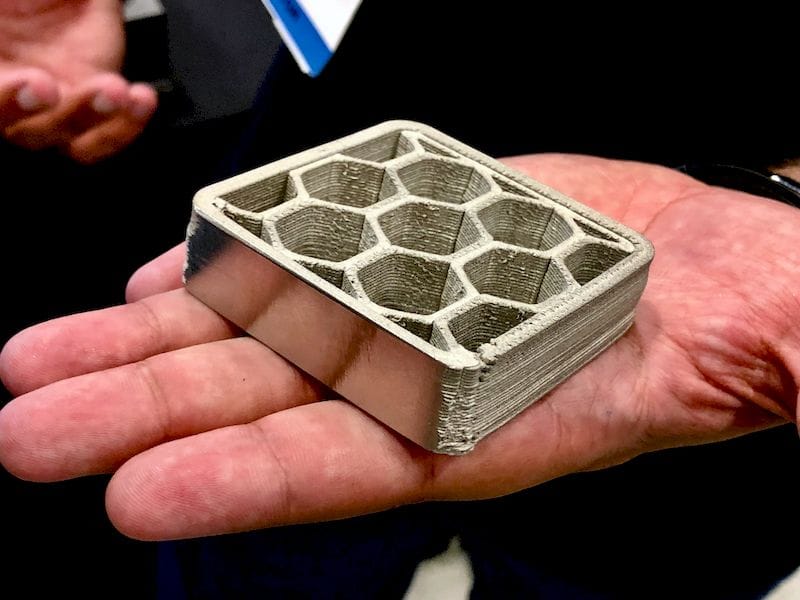
Pellets of metal powder and plastic are put in the hopper, and objects are 3D printed in the usual manner. Then, these green parts are treated by a process to remove the plastic binder, leaving a structure of metal particles. This brown part is then sintered in a suitable furnace to create the fully metal part.
There are advantages to this approach, as it is possible to 3D print voids, unlike some other 3D metal printing processes. Of course, the prints are somewhat coarse, as compared to finer metal prints on some other machines. However, there are plenty of applications that don’t require such detail.
But here is the huge advantage that we haven’t seen often with other 3D printer manufacturers experimenting with 3D metal printing: the pellets are standard metal injection molding pellets.
These are commonly available at low cost. They are found in almost any required alloys and have known, documented shrink rates.
This could be of great importance as it positions Cosine Additive to have a theoretically inexpensive, yet predictable 3D metal printing process that could be quite competitive against others that require proprietary metal materials.
This seemed like a bit of departure for the company from their normal activities, but apparently it was based on demand from customers who, I presume, were increasingly interested in 3D metal printing.
I suppose this is a natural extension of Cosine Additive users’ desires. The machine can 3D print large objects in a variety of engineering materials, and metal is another one that may attract the same audience.
Another great 3D metal printing option is coming.
Via Cosine Additive