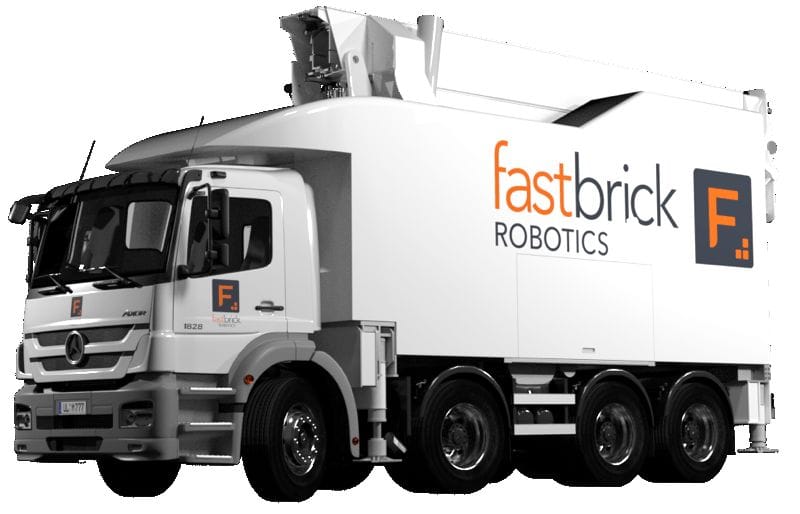
I’m looking at an Australian company that seems to have produced a 3D printer, but don’t call it one.
The company is Fast Brick Robotics, and their product is the Hadrian X, perhaps named after the Roman leader who made a notable wall – of bricks.
It’s a robotic system that precisely places bricks in sequence to create a complete structure, much like a human work crew might do. Of course, the advantage of robotics is precision and tirelessness. Robots don’t take breaks. Although they do break, on occasion.
The Hadrian X uses a store of pre-made bricks and places them using a fascinating robotic arm and gripper. They explain:
The Hadrian X positioning system allows for a wide range of ambient environmental conditions. Boom motion is compensated by FBR’s patented, multi-axis stabilisation system. This allows the blocks used in the construction system to be placed with unprecedented accuracy.
As the robot is working from the original CAD files of the structure, what the architect has designed and engineers have checked is EXACTLY what is built, down to the millimetre.
The bricks are held in place by an adhesive – not traditional mortar. Why so? Because the adhesive used is actually stronger than mortar, which really isn’t strong at all.
FBR says their system is capable of delivering up to 1000 bricks per hour, two to three times as fast as a single human bricklayer. What’s more interesting is that the bricks used by Hadrian X are apparently 15 times larger than a standard human brick. The robot arm is stronger than a human’s, and they’re leveraging this power. But it also means a much larger structure can be built in the same time: 15 x 2 = 30 times the brick volume per hour. And the robot can work 24 hours a day as well, presuming you keep it supplied with materials, which are provided by the pallet.
What’s fascinating to me about the Hadrian X is that it’s so utterly similar to a 3D printer:
- Material is deposited according to a 3D model
- Deposition placement requires precision mechanisms
- Layers must adhere to each other for strength
- Specialized material must be supplied to the system
Up to now most 3D printing construction projects have used some variation of continuous concrete extrusion, which requires a lot of set up before building commences. I suspect the FBR process is a lot easier to execute, as they say you need only deliver a pallet or two of brick and the “rest is automated”.
Bricks also enable the concept of overhangs, which are obviously problematic when extruding near-liquid concrete.
I suspect that while the FBR system may work, the company may find it challenging to convince construction crews to widely adopt the new approach. This happens in every industry, where successful businesses “do not want to change what isn’t broken”.
This has specifically been the problem in 3D printing for many years, and it is only now that it is gradually being overcome. It was conquered by those who realized the 3D printing technologies could be used to develop new kinds of products and parts that leveraged the abilities of 3D printing in ways not possible using other making processes.
For FBR, the path forward may be to discover similar leverages for their brick printing system.
Let’s make buildings like they’ve never been made before!