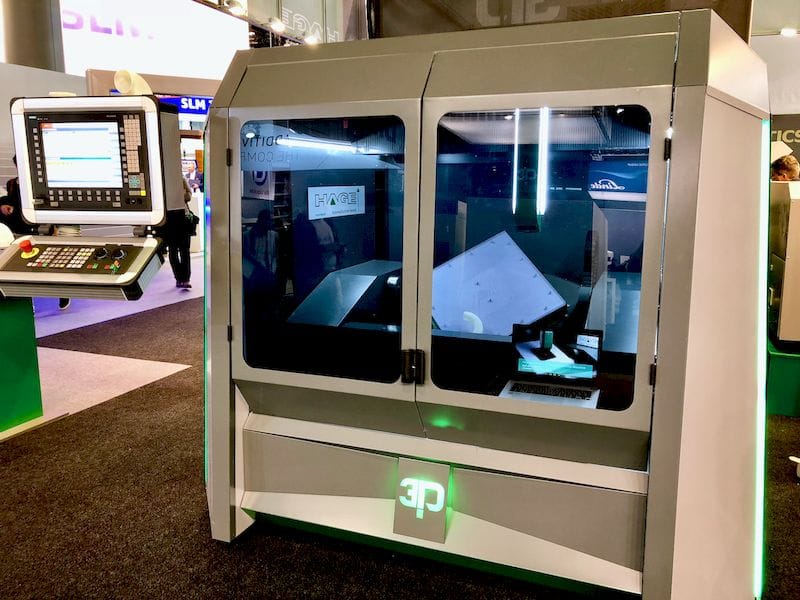
One of the rarer forms of extrusion-based 3D printing is known as “5-axis” 3D printing.
And one of the few companies developing such a complex device is Austria-based Hage, whose Model 175X indeed has 5 axes of 3D printing.
What’s the big deal about 5-axis 3D printing? There are some huge advantages, but also some disadvantages.
The idea behind use of 5 axes is that you can re-orient the print during 3D printing operations. This is quite different from the typical 3D printer in which the print remains stationary on the print plate and the nozzles run rapidly about the build chamber. Yes, some designs involve moving the build plate along a single axis, such as the Prusa i3 design, but essentially they are the same: three axes of movement.
A five axis system enables re-orientation. This is extremely useful because it means you can always 3D print without overhangs! If there is an overhang, the 5 axes simply rotate to re-position the print in such a way that the new material is deposited in a non-overhanging manner.
Yes, that means No Support Material is required!
Well, there are a very few situations where support may actually be required, even in a 5-axis scenario, specifically if there is a non-contiguous segment that has no other connection to the base model, for example. But nevertheless, support material is essentially eliminated for almost every print.
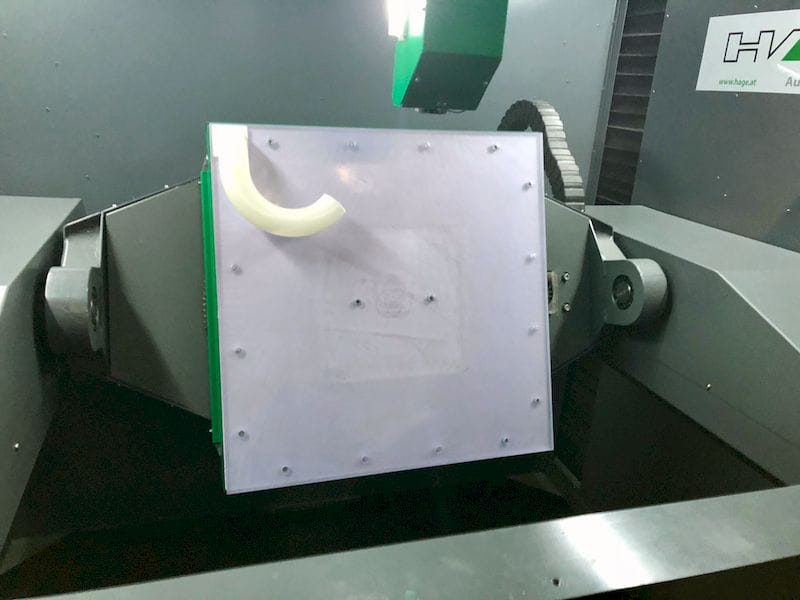
Another benefit is that the concept of layers becomes less important. With 3 axis systems the print is divided into thin parallel layers, much like a deck of playing cards.
But if you can constantly rotate and reorient the print, then the “layers” are definitely not parallel at all. You could, for example, extrude curved lines of material on the surface of a cylinder – and then change the direction on a subsequent layer, making the extrusions spray in several directions. This makes the part far stronger, because typical 3D prints tend to fracture along the relatively weaker joins between the parallel layers.
Another advantage could be speed. You don’t have to spend any time 3D printing support material, obviously, but you can also optimize the extrusion movements in 5 dimensions to obtain the shortest path to complete the object.
If these are powerful benefits, then why isn’t every 3D printer using 5-axis techniques?
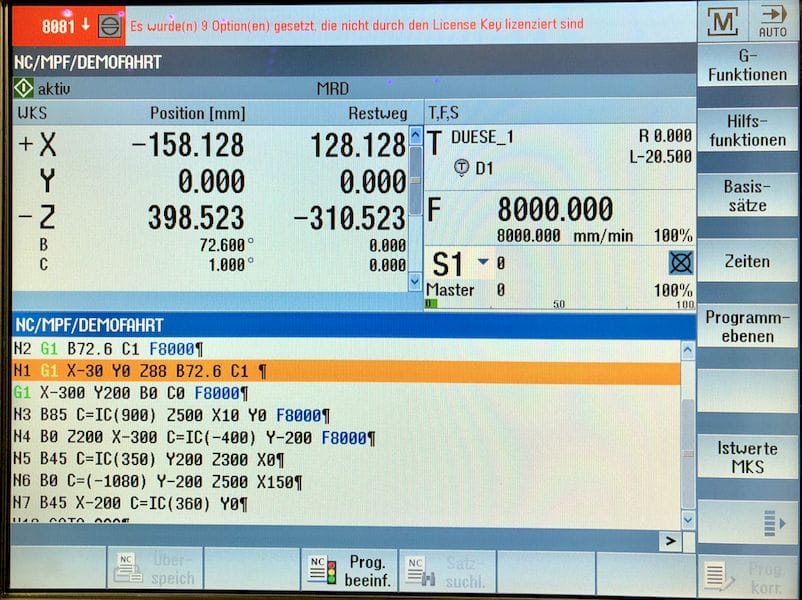
There are a number of issues.
One is cost: five axes are significantly more complex than three. There’s much more hardware involved, and it must be heavy-duty because it has to literally flip the build plate around. Typical 3-axis systems can be quite light because the plate is immobile.
The second is complexity: while there are plenty of 3-axis software solutions available, many at no charge from open source projects, there are few if any corresponding 5-axis software solutions. Typically one must buy these highly complex systems from providers like Siemens (who seems to be partnering with Hage on the 175X) at commercial price levels.
As a result it’s unlikely we will see inexpensive 5-axis 3D printer options available anytime soon.
Meanwhile, there are a couple of such systems available, like the Hage 175X.
Via Hage