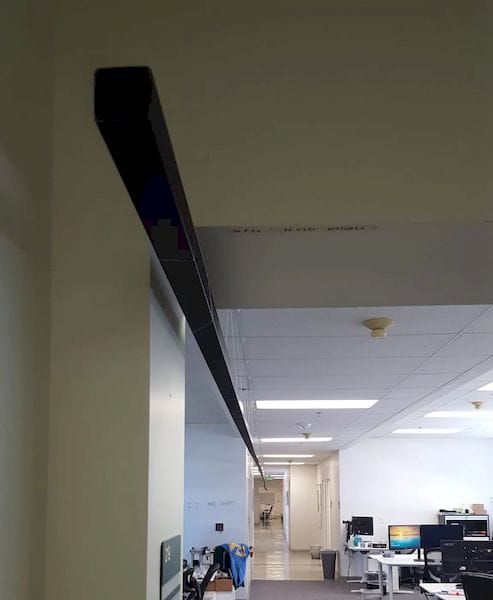
Made In Space achieved a very important milestone: the longest 3D print yet made.
By “longest”, I don’t mean the longest duration; you would not want a contest where everyone sits around waiting the longest. No, this is about length, and Made In Space 3D printed a structure no less than 37.7m long. Yes, that’s meters!
Previously the longest 3D print I’d seen was a demonstration done by Stratasys to show off their “Infinite Build Demonstrator”, a machine that 3D prints sideways and can theoretically print infinitely long objects if you keep feeding in thermoplastic pellets into its top-mounted hopper.
The experiment by Made In Space appears to follow a similar “infinite” process.
One big reason they’re developing this capability is for NASA’S Archinaut project with an ability to build very large space structures.
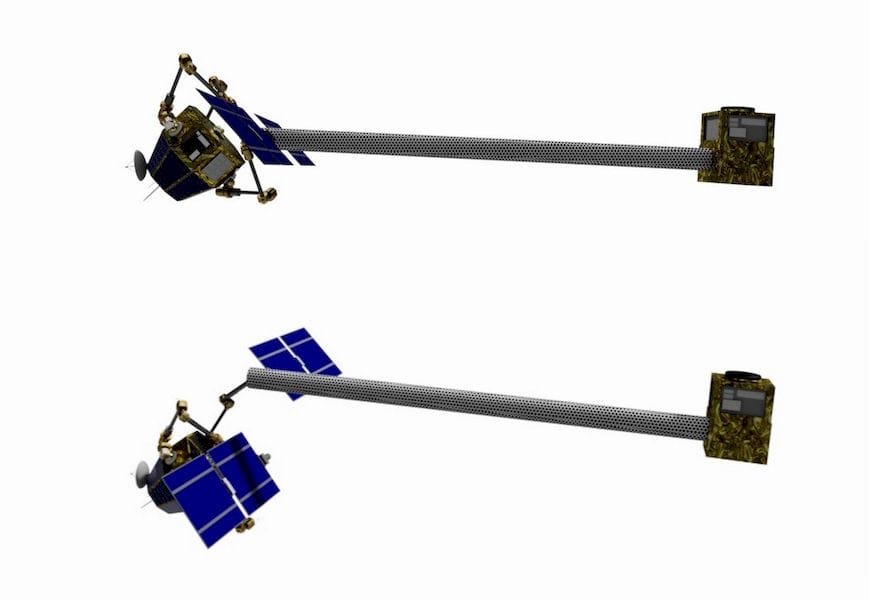
Large structures in space are inevitably necessary, but their large component sizes are problematic when attempting to ship them up from the Earth, as their typically bulky sizes don’t always fit in existing launch vehicles. To compensate, large structures today sent to space are often folded up, causing all manner of complexity in design and operation.
One way to circumvent that issue is to simply build the structures on site, and that’s what Archinaut is intended to investigate. Made In Space, selected by NASA for this work in 2015, is developing a specialized 3D printer to do just that, and evidently they are succeeding, based on the tests they’ve already done on orbit, and the recent lengthy print.
But the large-format space 3D printer will have some additional challenges beyond their current approach on board the International Space Station. While the ISS is a microgravity environment and requires a number of stringent safety protocols, the large-format printer must operate outside the station in the space environment directly.
This means in additional to microgravity, the machine must endure a vacuum, extreme temperatures – sometimes simultaneously, radiation and lack of immediate operator assistance.
There are some advantages, however. One that I can think of is that there would be little need for a cooling fan, as the freshly extruded hot material would be instantly exposed to a -200C environment where it could quickly radiate its heat away. There’s no air to blow in any case.
I am very interested to see this large format machine operate in space directly, because if it works, we could see a revolution in space construction with companies opting to build simple structures onsite rather than ship complex folding structures up in an expensive manner.
Via Space