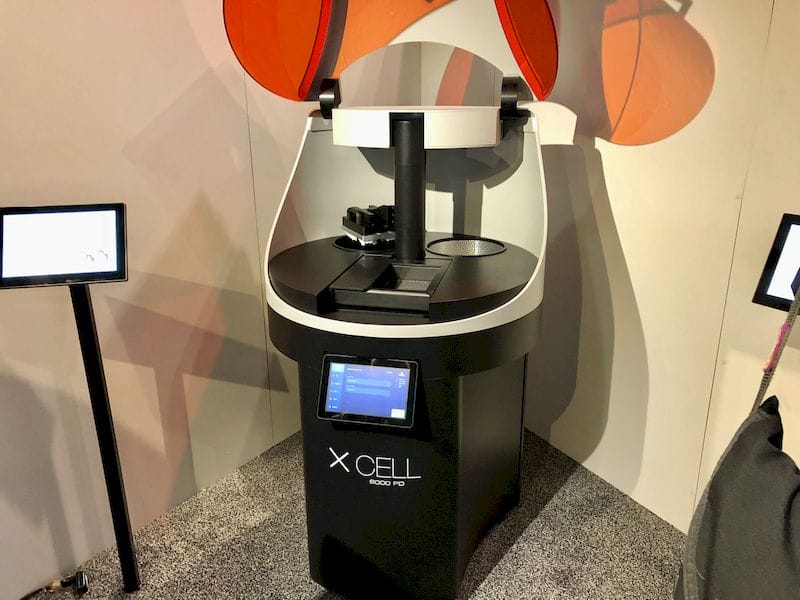
DWS is known for their precision resin-based 3D printers, but they seem to have developed an unusual automation system.
We recently had a peek at their new XCELL 6000 PD, which is an enormous machine powered by the SLA resin process.
How big is it? Unlike most of their product line, this item does not sit on a desk, as you can see in the image at top.
While nominally using their standard resin 3D printing process, the XCELL 6000 series employs some interesting features to make life easier for the machine’s operators.
One feature is a unique method for printing with continuous resin flow. Mechanisms are tilted to generate a flow of liquid resin material. This attempts to answer the problem of replacing solidified resin when the subsequent layers are produced by UV illumination. Many other resin 3D printers suffer from a delay when the print is raised for the next layer, as the often thick resin takes some time to flow into the gap. That should be minimized on the XCELL 6000 series because they are not only tilted, but actively pumping the fluid.
The other interesting feature is the “XPOD” concept which seems to be a new materials cartridge. In most resin 3D printers, the resin is dumped from the cartridge into the optical vat where printing takes place. When the print is finished the resin stays in the vat until you wish to change the material, in which case you must manually drain the vat back into the cartridge.
This is not the case with the XCELL system, which automatically drains the resin back into the cartridge, making for much easier material changes.
But there is another reason for this: the XCELL system includes integrated wash and cure systems. After the print completes, the resin is drained and an alcohol solution rinses off the raw, wet print. Once cleaned, a UV light bath cures the print to a final, solidified state.
This integrated system vastly simplifies the work of the operator, who more or less removes the completed print from the XCELL system. I suspect these features will be of considerable interest to operations that run continuous operations, as significant labor might be saved.
This machine is a lot more intelligent than most resin-based 3D printing systems
I’ve been referring to this machine as a “series” because that’s what it is. DWS offers the XCELL in several industry-specific configurations, including:
XCELL 6000SD: Industrial design, functional parts, design objects with demanding aesthetic features, models, prototypes.
For Jewellery:
XCELL 6000SD: Standard design, solid and detailed design models.
XCELL 6000HD: Solid design, filigree, fine detailed models.
For Dentistry:
XCELL 6000PD: Orthodontic applications, arches for thermoformed aligners, dental models, biocompatibile surgical guides, medical imaging, models for direct casting, models for dies, partial frameworks, crowns, bridges, temporary restorations, models for implant analogs.
Pricing is said to be between €45-65K (USD$55-80K).
Successful 3D printer manufacturers in recent years have focused much more on the issues of the users, and it seems that DWS is doing so in several aspects with the XCELL series.
Via DWS