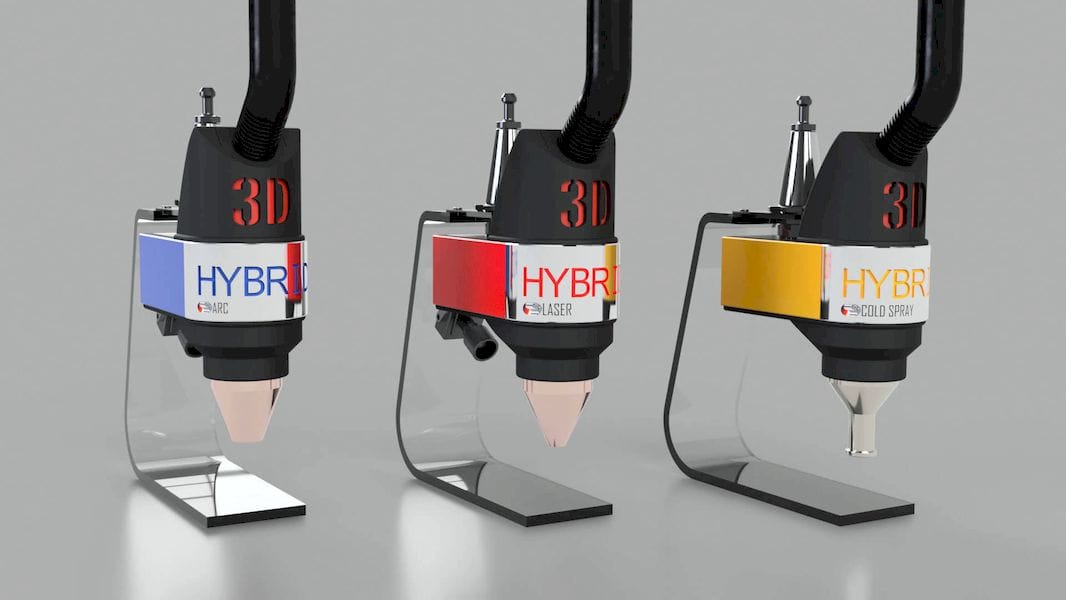
This could be a very big idea: 3D Hybrid Solutions announced a system to convert everyday CNC machines into powerful 3D metal printers.
The startup company, based in Los Angeles, offers add-on hardware that could become a tool in a multi-tool metal CNC machine. Typical competent metal CNC machines today offer the ability to mill solid metal into many geometric shapes and include a tool-changing capability.
Tool changing is usually employed to make the milling process more efficient; use a large milling bit to chop off the majority of the material, and then use progressively smaller milling bits to grind down to the shiny result.
But what if one of those tools were a 3D metal printing unit?
That’s exactly what 3D Hybrid Solutions seems to be doing with their solution.
The process would be as follows:
- Install the 3D metal printing toolhead into a metal CNC machine
- 3D print some layers, roughly, using it
- Swap out the 3D metal printing tool and replace with one of the existing CNC tools
- Mill down the edges of the printed layers to smoothness
- Swap again and continue 3D metal printing upwards
- Repeat until complete
This is actually a process used by some 3D printer manufacturers who have developed hybrid CNC – 3D metal printers that do exactly this. However, they typically cost USD$500,000 or even more.
Hybrid 3D Solutions’ have suggested their tools would cost in the USD$50,000 range – perhaps 10X less expensive than buying a dedicated CNC – 3D printing hybrid device.
That could be extremely attractive to a workshop that has already invested hundreds of thousands in a CNC machine. With a relatively small investment, such an operation could almost instantly gain an entirely new capability for their clients.
And there’s something else I must mention: 3D Hybrid Solutions is providing “tools”, not just a “tool”. There are no less than THREE different 3D metal printing toolheads.
One is the “Powder + Wire Arc” toolhead. This unit consumes standard welding wire and uses a powerful electric arc to melt it, while your CNC machine moves the tool around to deposit the meltpool appropriately.
They call it a “Powder” and Arc toolhead because it also is able to use an amount of metal powder that can be mixed with the welding wire to create new alloys or composites on the fly. For example, you could mix in glass powder. This feature alone would transform a metal workshop into one that can create its own materials!
The second toolhead is the “Laser”, which as you might expect, includes a powerful laser (they list it ranging from a mere 500W to 25,000W!) Fine metal powder is blown through a special nozzle where it is blasted by the laser into a meltpool, which the CNC again deposits appropriately.
One very intriguing feature of the Laser tool is that it has what they describe as an “antigravity” nozzle, which can apparently deposit materials at angles greater than 90 degrees to the vertical!
This means that your 5-axis CNC machine would theoretically be able to 3D print metal in 5 axes, making the print operation shorter in duration.
The final toolhead of the three is the “Cold Spray” unit, which handles materials that are difficult to use with the other toolheads, such as copper. In this tool, the metal powder is blown through a fine nozzle at extremely high speeds (up to 3500fps / 1000m/s) where the kinetic energy mashes the particle onto the target.
This approach could be used to build entire objects like the other tools do, but more interestingly could be used to spray a metal coating on top of an existing object or repair one, so long as the CNC understands its shape.
And that is one of the questions we have about this concept: how does the software work? Typical CNC software may not understand deposition functions, let alone three different kinds, so 3D Hybrid Solutions will have to show the way forward. They don’t mention much about software implications, but I suspect that it could be a big concern for CNC workshops wishing to convert their equipment into this new mode. Some training would be required, and perhaps even new software.
Nevertheless, this is quite an interesting development that could stall the efforts of the dedicated hybrid CNC – 3D printer manufacturers.