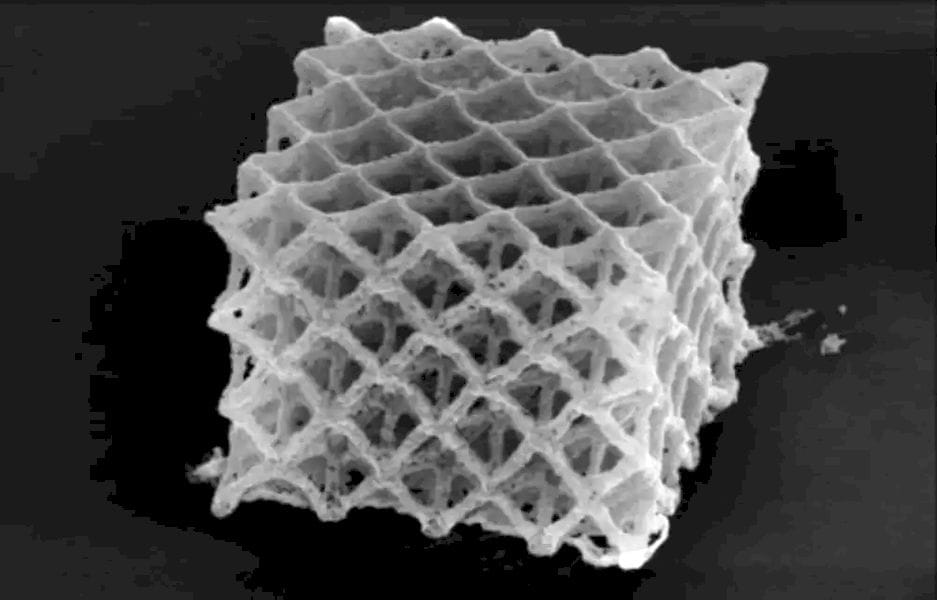
Metals. Humans have been developing innovative ways to use these electric-conducive, often shiny, malleable materials for centuries.
From creating intricate details in jewelry to forging weaponry and constructing giant structures, the use of metals continues to evolve in modern times.
Even 3D printing has its place on the timeline of metalsmithing, albeit relatively recent. Now, that marker just got bigger in a small way—a very small way. In fact, it is so small that the prints can’t be seen with the naked eye. Thanks to scientists at the California Institute of Technology (Caltech), it’s now possible to create complex nanoscale metal structures using 3D printing.
Julia Greer, Caltech materials scientist, has long been a pioneer in the creation of tiny 3D architectures via additive manufacturing, including lattices with beams nanometers apart that are created using ceramics and organic compounds. However, Greer had not used metals in her work.
“Metals don’t respond to light in the same way as the polymer resins that we use to manufacture structures at the nanoscale,” said Greer, professor of materials science, mechanics and medical engineering in Caltech’s Division of Engineering and Applied Science. “There’s a chemical reaction that gets triggered when light interacts with a polymer that enables it to harden and then form into a particular shape. In a metal, this process is fundamentally impossible.”
That is, until now. In a recent press release, the Caltech team details its study titled “Additive Manufacturing of 3D Nano-architected Metals,” which was recently published in Nature Communications.
Read more at ENGINEERING.com