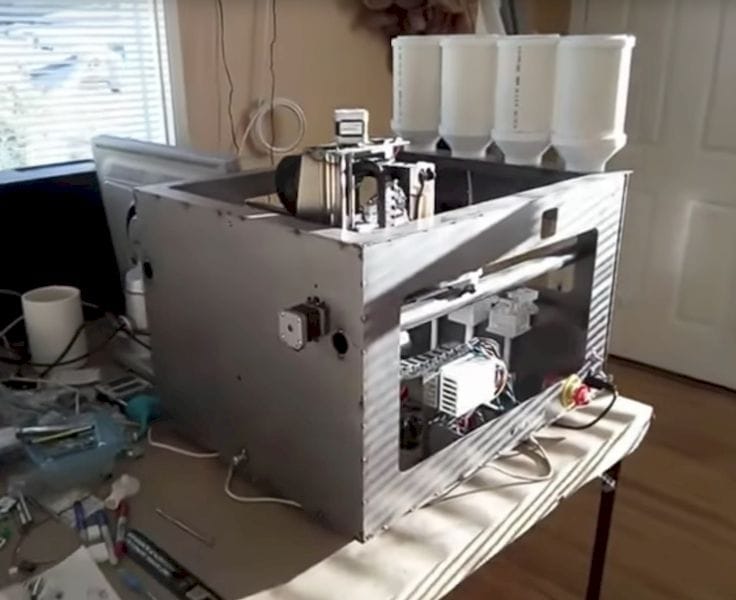
Iro3D has a metal printing process that is, in retrospect, obvious, and I wonder why no one else came up with the idea before.
3D metal printing is otherwise a rather complex process involving precision lasers, fine powders, molecular chemistry, sophisticated software and a whole lot of money to pay for the machine, materials and expertise to run it.
This huge cost has driven many to attempt to invent less expensive methods of producing 3D metal prints, and we’ve seen many very interesting processes emerge in the past couple of years from a series of startups. Some look to become huge players in the industry, such as XJet or Desktop Metal.
Another 3D metal printing process apparently developed by Seattle startup Iro3D seems so straightforward I’m baffled as to why no one seemed to attempt this previously.
In a video posted a couple of months ago, Iro3D explained their 3D metal printing process. The method involves using standard metal powder, available at low cost, as well as an inert support material in powder form.
The Iro3D machine holds stores of these two powders in hoppers above the printing mechanism. It doesn’t use an extruder or a hot end, but instead has “pourers”. These appear to be simple funnels that selectively release powder onto a plane.
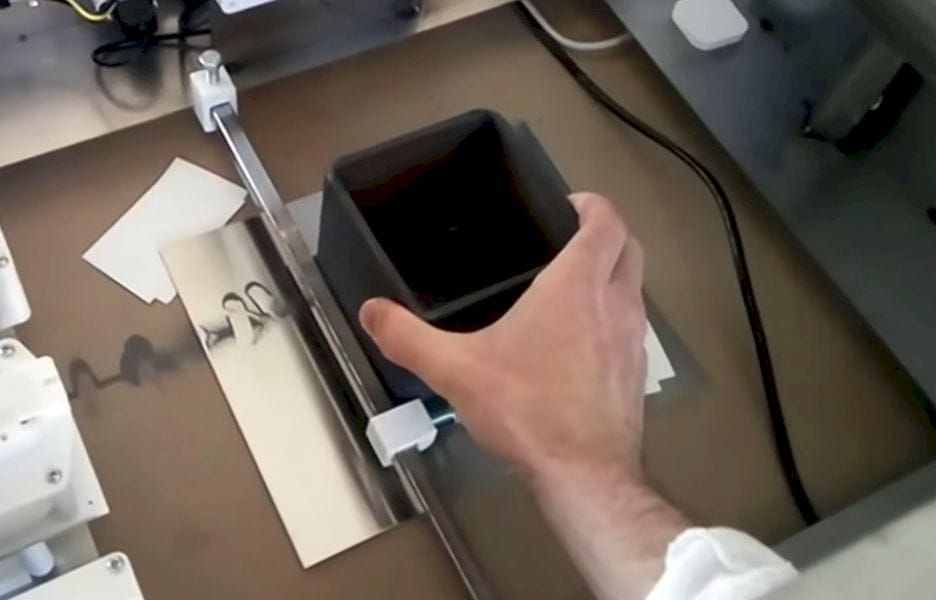
And this is where the interesting part appears: the plane of 3D printing is within a crucible! This is the bottom half, of course, with the top open for the pourers to access the bottom of the crucible.
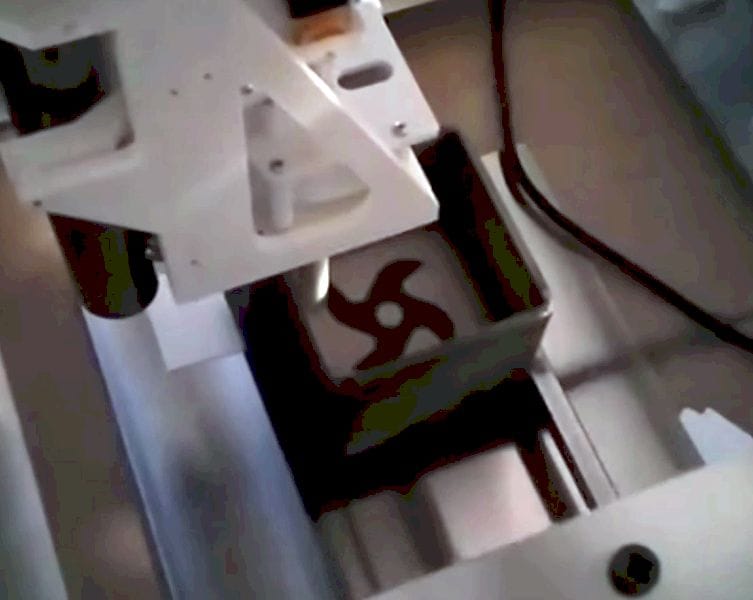
The powders are deposited within the crucible selectively, with metal powder laid in the shape of a slice, and completely surrounded with the support material. The printing proceeds until the entire object is “printed”.
The crucible is removed from the printer, sealed and placed in a furnace for sintering. The metal powder fuses into the desired object, while the support material remains loose. When complete, the crucible is emptied and the final part may be cleaned.
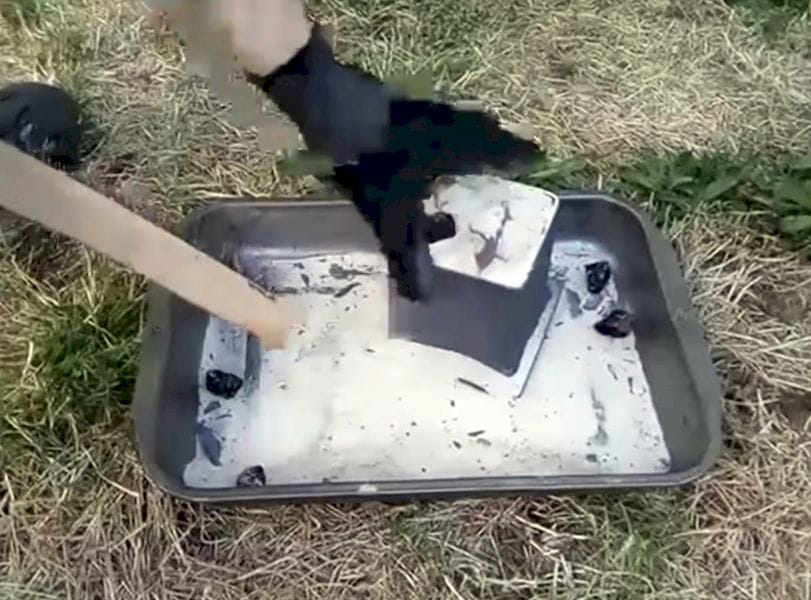
It appears that this process works reasonably well according to images of the prints, although they do not appear to have the very best surface quality. The very coarse surface is likely due to the nature of the support material and granularity of the metal powder. In this image we see there has been some buffing on the top surface, while the rest remains coarse.
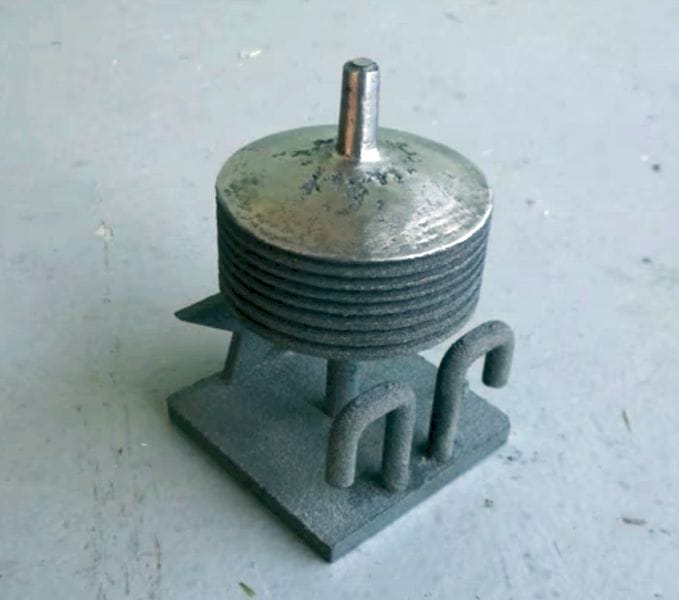
This may have something to do with the process. I can imagine that one must be extremely careful when moving the loose powder in the crucible before sintering. Don’t shake it or your print may look like a Star Trek transporter accident!
From the appearance of the machine itself shown at top, it definitely is a prototype, with welding marks clearly visible.
The process is fascinating because it is so simple. It will clearly work, as it is similar to traditional metal processes and in fact uses the same commonly available materials. While Iro3D’s videos create steel parts, it’s likely this process could work well with a wide variety of metal alloys.
Iro3D says the “beta” device is available only in the Seattle area at a cost of USD$5,000. This seems a bit unusual, as it suggests the company has very limited capacity for support, as one might expect with a startup. While there is very limited information available, I get the impression Iro3D is a very small company. Their video seems to show the machine being built in a residential location.
And that could be a problem for them. It’s not clear whether they have patented this process (or if someone else already has). Thus it is entirely possible other more well-funded companies might co-opt the concept and make a similar machine quite quickly due to the simplicity of the process.
There has been no information published by the company for a couple of months, so the stage of their project development is unclear.
Via Iro3D