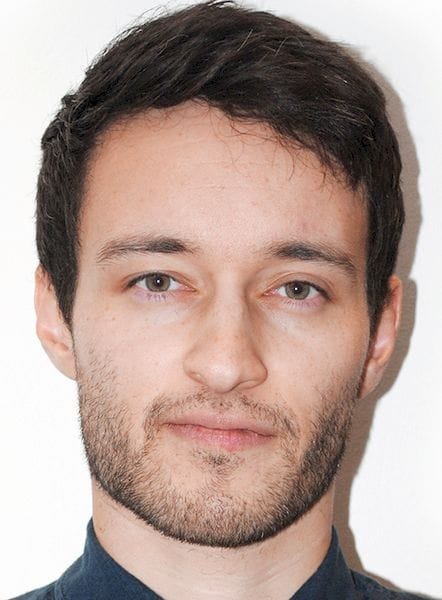
We asked Dr. Daniel Richards for his view of the future of 3D design.
Recently available 3D printing technologies are providing a means to produce astonishing new products, but this is only possible if there are software tools that permit new types of 3D designs to feed these new 3D printers.
I’m puzzled as to how traditional 3D design tools might be adapted – or even replaced – by newer approaches that can more easily design incredible 3D objects to be produced by 3D printers now emerging. To get some answers, we asked Dr. Daniel Richards of Lancaster University in the UK, who just happens to be working in this very field.
This is part 2 of a 2 part interview. Part 1 is here.
Fabbaloo: What approaches have you considered thus far? What have you found? What doesn’t work?
Dr. Daniel Richards: Let me start with a bit of background, over last couple of years, I have been developing an approach to designing multi-material objects with volumetric texture maps. The big idea has been to rethink solid 3D modelling techniques that are traditionally used in CAD for manufacturing, and consider an alternative approach that is more closely related to designing “shaders” for 3D graphics. To try and make this technical description easier to visualise: imagine drawing a curved surface, and then applying a “texture” to this surface which can add depth to it, wrap and distort the new volumetric surface geometry, make holes and transform topology, and completely describe the material properties of every point (at any resolution) within the “deep surface” design (Fig 1). That is the basic idea.
Initial experiments with this approach have worked well and have some specific advantages. Specifically, building on some incredible work of computer scientists Prof. Ken Stanley and Prof. Jeff Clune (related to an algorithm called CPPN-NEAT), we have shown that it is possible to discover interesting 3D designs and optimise structures for engineering applications with this sort of approach. The challenge of the interface has become: how can we now put this technical power in the hands of users to create powerful and expressive design processes, and how can we simultaneously extend, edit and further develop the technical foundations to enable alternative CAD metaphors?
One technique we have tried and that works well is creating voxel models that can be algorithmically generated and manually edited in a manner similar to the game Minecraft (Fig 2). Notably, the manual edits can be compiled back into the (vector-based) texture map to allow changes to persist across scale-changes (i.e. changing the resolution of the voxel grid). Designers can switch voxels on or off, change materials of voxels at different resolutions of the voxel grid, and perform other transformations such as adding symmetry, smoothing geometry, and changing colours. However, designers can also manipulate the designs algorithmically by navigating and comparing populations of solutions, and exploring different evolutionary linages of specific designs.
We are also thinking about how designs can be natively sliced, analysed and prepared for fabrication. In this process 2D slices can be isolated and material compositions explored at varying scales – i.e. from voxel-by-voxel descriptions to approximated macro-properties of physical features (Fig 3). This is still work-in-progress, and there are still plenty of challenges relating to accurate approximation of macro-properties, but I am excited to share this to give an indication of where this is going.
The biggest challenge at the moment, and the main thing that currently doesn’t work as well as hoped is the technique for interacting with the texture maps themselves. As shown in Fig 1, we currently have confusing network diagrams that designers must wrestle with in order to produce useful designs. We are currently in the process of exploring different visualisation and interface techniques for manipulating these texture maps (Fig 4). This is also very much work-in-progress, but by working at the intersection of data art, visualisation and interface design we are hoping to explore new ways of crafting 3D objects.
Fabbaloo: Would it be possible to simplify such an interface to permit wider segments of the general population to make use of it? What would be the challenges?
Dr. Daniel Richards: Absolutely, this is our goal. There are two main challenges from my point view. The first relates to discovering better ways of making sense of our texture maps so that they can be used to craft useful multi-material designs. The second relates to finding funding and working with commercial partners to test and evaluate the interfaces in relation to different application domains.
Fabbaloo: What stage of development is the project at today?
Dr. Daniel Richards: I am currently collaborating with Dr Allan Rennie and Tom Abram at Lancaster University’s Product Development Unit to test the capacity of these methods to fabricate functionally graded multi-material structures using the Stratasys J750 machine (Fig 5). We have not released any of these tools or code at present, but intend to release tools for people to use in the near future after further UI development and testing. We are also actively looking for interesting application domains to test the methods further, and welcome opportunities from interested parties.
Fabbaloo: What are the prospects of seeing this technology on the market? Have you been partnering with any particular suppliers or patenting any approaches?
Dr. Daniel Richards: We currently have a patent pending and are considering commercialisation options. We have been working with Stratasys are part of their exciting Voxel Print Research Program, and recently attended FormNext with them to help launch their new GrabCAD Voxel Print tool.
Fabbaloo: What are the most interesting potential applications for such technology? What might we see people create when 3D objects can be made from differentiated materials internally?
Dr. Daniel Richards: In the short-term, there are various possible application domains including: functionally graded body protection that seamlessly transitions from soft and comfortable to hard, protective materials within a single print. For example, medical splints, cycle helmets, sports equipment, or wearables. Mechanical parts that can be designed with integrated vibration damping qualities simply by tuning material properties, soft robotics, compliant mechanisms, and stab-proof vests.
In the longer-term, the sky is the limit. As the material palette of printers continue to expand we will likely see exotic 3D printed electric circuits embedded within parts (whereby properties such as resistance could be tuned at the voxel level!), functionally graded alloys, ceramics, and increasingly functional shape changing structures. I think we are at the start of what could be a very exciting journey for how we craft physical products with voxels!
This is part 2 of a 2 part interview. Part 1 is here.