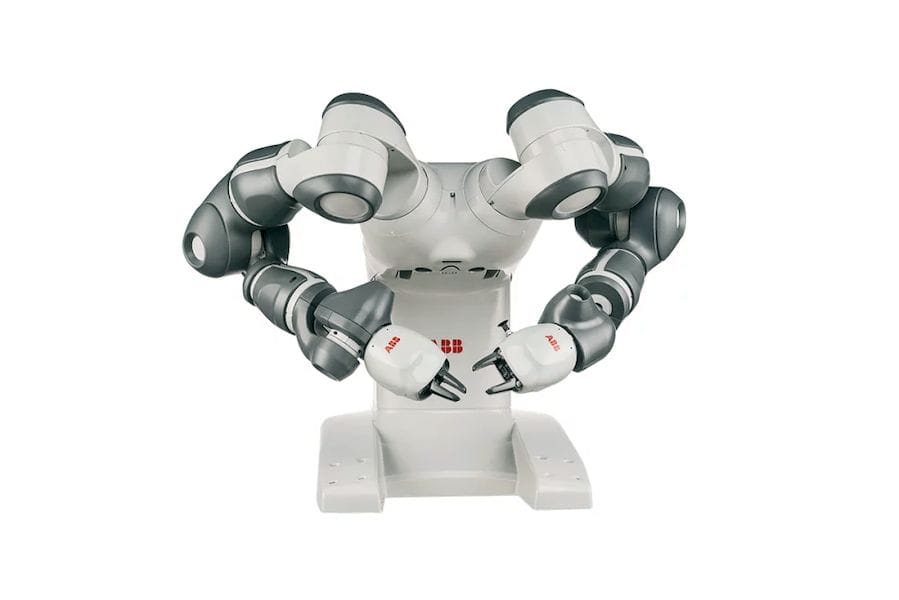
Fused filament fabrication 3D printing processes such as those performed by Ultimaker machines allow for some incredibly functional end-use parts.
If you need a sturdy and strong plastic item that can be used over and over again for a very reasonable price, then you could do a lot worse than this plastic extrusion process.
For those reasons and more, the robotics division of Swedish-Swiss engineering conglomerate ABB has turned to 3D printing to create a range of custom graspers (or “end effectors,” to use the proper term) for their industrial collaborative robots.
ABB has designed and manufactured YuMi. YuMi is a double-armed collaborative robot intended to work alongside humans in a production environment and is particularly good at tasks where small components need to be manipulated and inserted into larger assemblies. Such tasks are commonplace in the electronics and automotive industries.
Of course, assembly components come in all different shapes and sizes, and there is not a cost-effective universal grasper solution that is capable of performing all of these maneuvers effectively. Not yet, at least. So, ABB opted for a more tailored approach that requires a range of different graspers suited for individual tasks.
“We were developing the fingers here, for the YuMi … and then we had to make them, so we went through the traditional means of producing fingers with external providers. And it was taking a lot of time and it cost a certain amount of money, so we started to search for alternatives,” said Guillaume Pradels, YuMi product manager at ABB France. “We found out that it was very easy to print them instead of having them milled for example, which takes a lot of time.”
Not everybody at ABB was convinced of the utility of 3D printing in the beginning though.
“When we came to the idea of 3D printing, at the beginning, people were skeptical,” continued Pradels. “But I went to a fair with a 3D model on a USB stick, and I got it printed and then I brought it back here at ABB. And when they saw the results, they were very happy and convinced.”
One advantage of using rapidly produced components enabled by 3D printing was that ABB could test a lot more variants as the products evolved, over a much shorter period of time than would have been permitted with traditional manufactured parts. This accelerated feasibility studies (which were required by the customers) and helped ABB fast-track their validation process, enabling many iterations to be tested and a final product that could be produced in a fraction of the usual time. Pradels noted that the design time from final 3D design to final print was reduced to just a couple of hours.
Read more at ENGINEERING.com