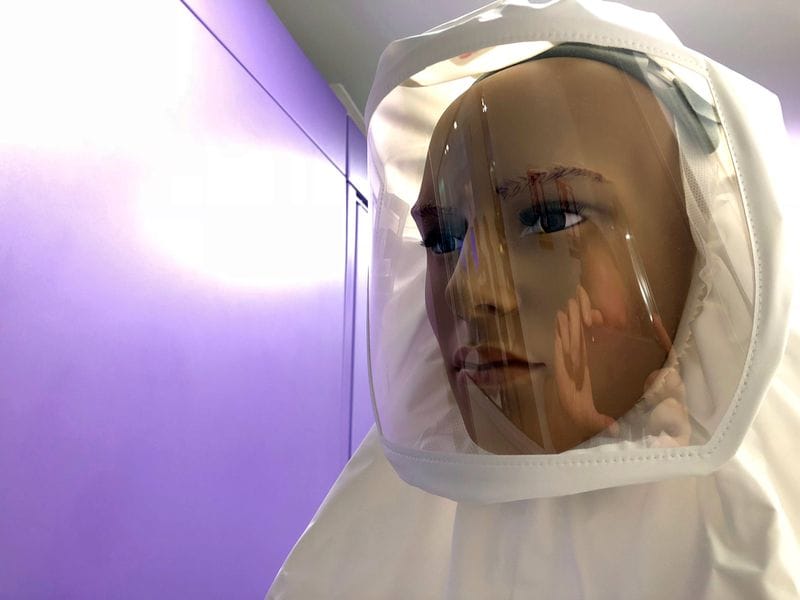
The last time we saw AddUp’s modular 3D printing workshop, it was merely a desktop model. Now we managed to walk through a real one.
AddUp produces a large and capable 3D metal printer, as do several other printer manufacturers. What’s often forgotten or ignored by 3D metal printer manufacturers is that there is a considerable expense and effort required to actually install these machines in a practical workshop.
The challenges derive from the nature of typical 3D metal printing processes, which involve very fine metal powders. These powders are not only toxic if breathed in, they can also be highly explosive. The powders must be kept pure and not exposed to moisture, lest they rust or congeal. They must be sieved to ensure the particles are of correct size or else print quality could be compromised.
For all these reasons there are significant structures involved in installations of 3D metal printers. You have to create a negative pressure room to ensure the powder doesn’t escape, for example. You must ensure those entering and exiting the workspace don’t contaminate or distribute the dangerous and highly expensive powder.
For these reasons it’s often necessary for companies installing 3D metal printers to engage an architect and/or engineer to develop a suitable workspace for the equipment and its operators. It can be an expensive and time consuming step towards achieving the ability to 3D print in metal.
AddUp recognizes this and has developed an incredible short cut: they have outfitted a modular workspace that contains all the features you’ll need to get started. This completely short-circuits the typical installation process and should speed up installation considerably. It also provides increased safety for personnel using the solution.
Built in the size of a standard 40ft “sea worthy” container, AddUp’s modular system includes all the inputs and outputs you need to get your AddUp (or other, I presume) 3D metal printer running.
You can literally drop one of these inside an existing space and hook it up to the required inputs and it’s ready to receive a 3D metal printer.
Let’s take a tour of the modular facility.
First, you enter the module through a conventional doorway. There is a step up.
The initial room is a changing room, where you can remove your normal attire, hang up your coat, etc., and don appropriate suits for work in the module.
You then pass through a clean-up room, where you can wash off materials before taking them back outside when you’re finished in the module.
Doors are controlled to ensure there are no mistakes in air pressure.
This panel shows the inputs that would normally be hooked up to the 3D metal printer inside. The inputs include nitrogen and argon feeds, compressed air and exhaust for output.
The 3D metal printer itself sits within the larger space in the module. However, in a practical workshop you won’t likely find cocktail tables. At least in the workshops I frequent, anyway.
Once the print is complete, it’s placed in this air controlled delivery chamber. This is the inside view.
The outside view of the same chamber, where completed parts can be extracted from the module and taken to subsequent post-processing stages.
On the exterior of the module, you will find the corresponding input (and output) hookups for necessary environmentals.
The modular concept seems complete and a relatively easy way to get a 3D metal printer operation set up quickly. It’s also possible to have different types of modules pasted together to form a complete manufacturing sequence, including post processing, for example.
We’re told the module cost is in the €200,000 range.
Via AddUp