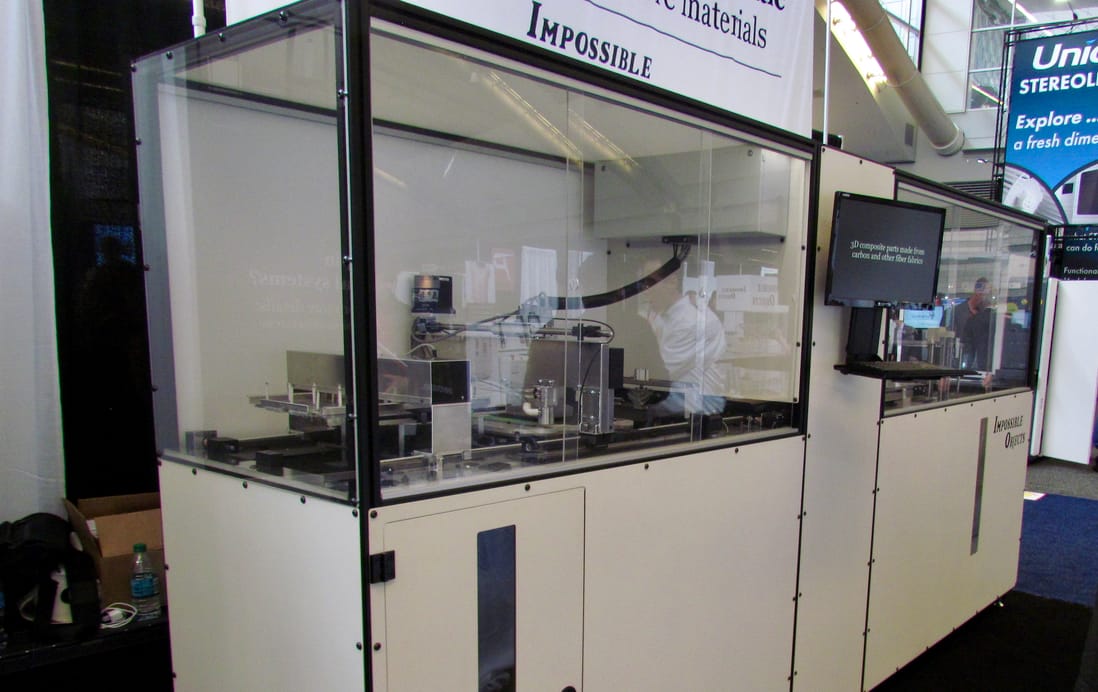
Illinois-based 3D printing startup Impossible Objects has received a hefty amount of cash.
The startup is pursuing a very different method of 3D printing in plastic: it uses a sheet-based approach they call “CBAM”. We’ve written about them previously and even had a look at their machine up close. It’s an interesting technology that offers some advantages over other 3D printing processes.
Essentially, their process laminates successive sheets of plastic material together, slicing off un-needed bits as required. Truthfully, this is really a subtractive manufacturing process rather than an additive one, but nevertheless it is a form of 3D printing in which you can “print” objects.
Their approach is quite reminiscent of MCOR Technologies’ paper-based 3D printing system. That approach targeted the color market by offering the ability to print fully textured RGB color objects using only plain paper as the input material. The choice of paper as material dramatically lowered the cost of operating the system, as compared to similar plastic color 3D printers. The material was the key to their process.
And the same is true of Impossible Objects: these plastic sheets I speak of are definitely not paper; they can be any number of different powerful materials, including: carbon fiber, Kevlar and fiberglass.
The big difference is that these sheets will have fully strands of the strengthening material embedded within them, as opposed to other 3D printing techniques that also use similar materials.
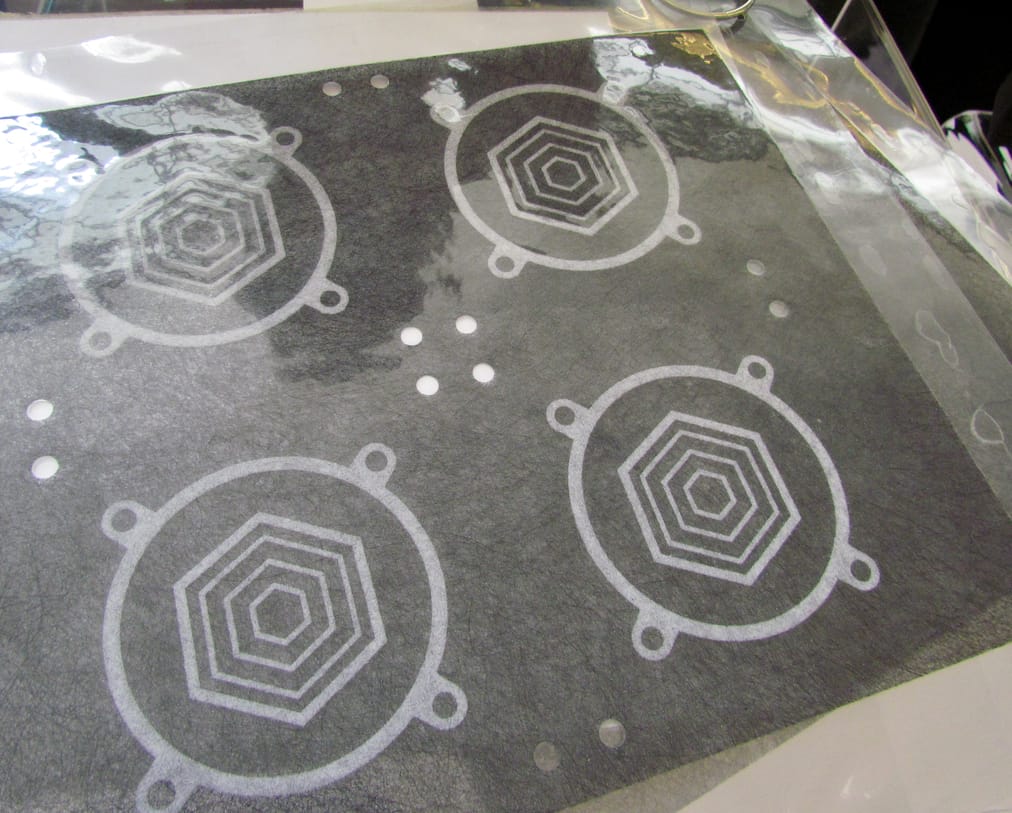
Consider carbon fiber, for example. A typical carbon fiber 3D printing system will employ a thermoplastic filament containing chopped up bits of carbon fiber. This makes the printed object somewhat stronger, but it is certainly not as strong as if the object had full strands of carbon fiber running its length.
That’s what happens in the Impossible Objects’ CBAM approach: the remaining sheet after cutting does indeed contain full strands of the embedded material, making the objects impressively strong.
However, there are some challenges in that not all geometries can be properly 3D printed using this approach. You can easily imagine a shape, for example, that has an embedded void. How can you remove the cutout for the void after printing?
Nevertheless, this process is certainly suitable for a wide variety of parts that don’t fall into the impossible geometries.
And that, perhaps, is why a consortium of investors have sloughed no less than USD$6.4M into the company.
What will they use it for? I suspect it will be primarily used to bring their name forward, as they are not particularly well known yet. They’ll no doubt invest in sales and marketing operations to get their unit production up.