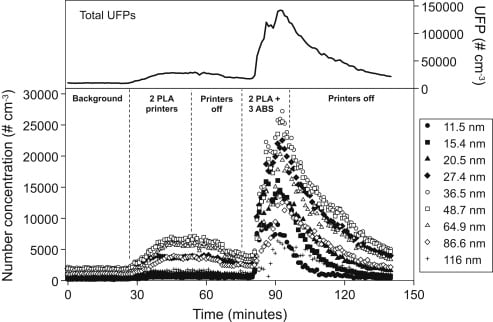
There’s been much ado about nanoparticle emissions from desktop 3D printers, but one solution may actually not be one.
Debate continues over the potential safety implications of using desktop 3D printers, as they apparently emit varying quantities of ultra fine particles (UFPs). These lightweight particles become airborne and can therefore be breathed in by those nearby.
What is unclear is the effects of UFPs on personal health. MSDS documents (Material Safety Data Sheets) that accompany (or should accompany) 3D printer material shipments sometimes indicate issues, or not. Here are some excerpts from the PLA MSDS from MakerBot include:
Inhalation: Heating may release vapors which may be irritating. In case of inhalation of decomposition products, affected person should be moved into fresh air and kept still. Get medical advice/attention.
Provide local exhaust ventilation system. Ventilation should be sufficient to effectively remove and prevent buildup of any dusts or fumes that may be generated during handling or thermal processing.
However, their ABS MSDS, which contains much of the above as well, also contains this:
ACGIH – Threshold Limit Values – Biological Exposure Indices (BEI) Styrene (100-42-5) 400 mg/g creatinine Medium: urine Time: end of shift Parameter: Mandelic acid plus phenylglyoxylic acid (nonspecific); 40 µg/L Medium: urine Time: end of shift Parameter: Styrene
Which essentially says that the ABS contains Styrene and there are limits to how much exposure is safe.
What’s happening is that when the thermoplastic is heated it begins to emit UFPs. How many? There have been a few studies, including this one.
This paper shows that UFPs are emitted after heating commences, and that the UFPs come in a variety of sizes, as you can see in their chart at top and below. Note that ABS produces far more than PLA in their experiment.
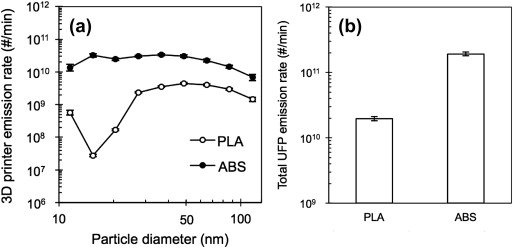
The long-term health effects of breathing in UFPs is not clear, as far as I can tell, thus it is obviously a good idea to provide a solution to accumulating UFPs in the 3D print workshop. On the other hand, our air is swimming with nanoparticles of many kinds, many of natural derivation.
The obvious solution is simply to ventilate the area, as listed in MakerBot’s MSDS. But that isn’t always feasible, as the workshop or office using the device may not provide a physical means to install ventilation.
The alternate solution most frequently employed is by installation of a filtration device. Some filter systems scoop air directly from the hot end, the source of the emissions, while others involve erecting a sealed enclosure equipped with a blower and filter around the 3D printer. Enclosures are also valuable for other reasons, including their ability to maintain a consistently heated build environment.
Some vendors have also included air filtration systems directly within the 3D printers themselves, but such systems are the exception in the market today. You can also purchase external “lab style” standalone filtration units and somehow hook them up to your 3D printers.
But here’s the catch: you will sometimes see these filtration systems billed as being equipped with a HEPA filter, the de facto standard highly effective air filter. You’ll see them in many consumer air cleaners, for example.
The problem is that the HEPA standard specifies the ability to filter down to 0.3 microns – and the UFPs as measured by the researchers above ranged from 0.012 – 0.116 microns.
In other words, the UFPs will pass through standard HEPA filters, blowing the UFPs into your workplace. Not good.
It’s not clear if you can easily obtain filters able to capture particles this small, which is perhaps why some 3D printer manufacturers chose not to include them.
Those making their own filtration enclosures should be aware that stock HEPA filters may not eliminate UFPs. I’ve read some material suggesting that respirator filters may do a better job, so that might be an option.
But to me, this finding means that the best option is to truly install a proper external ventilation / exhaust system.