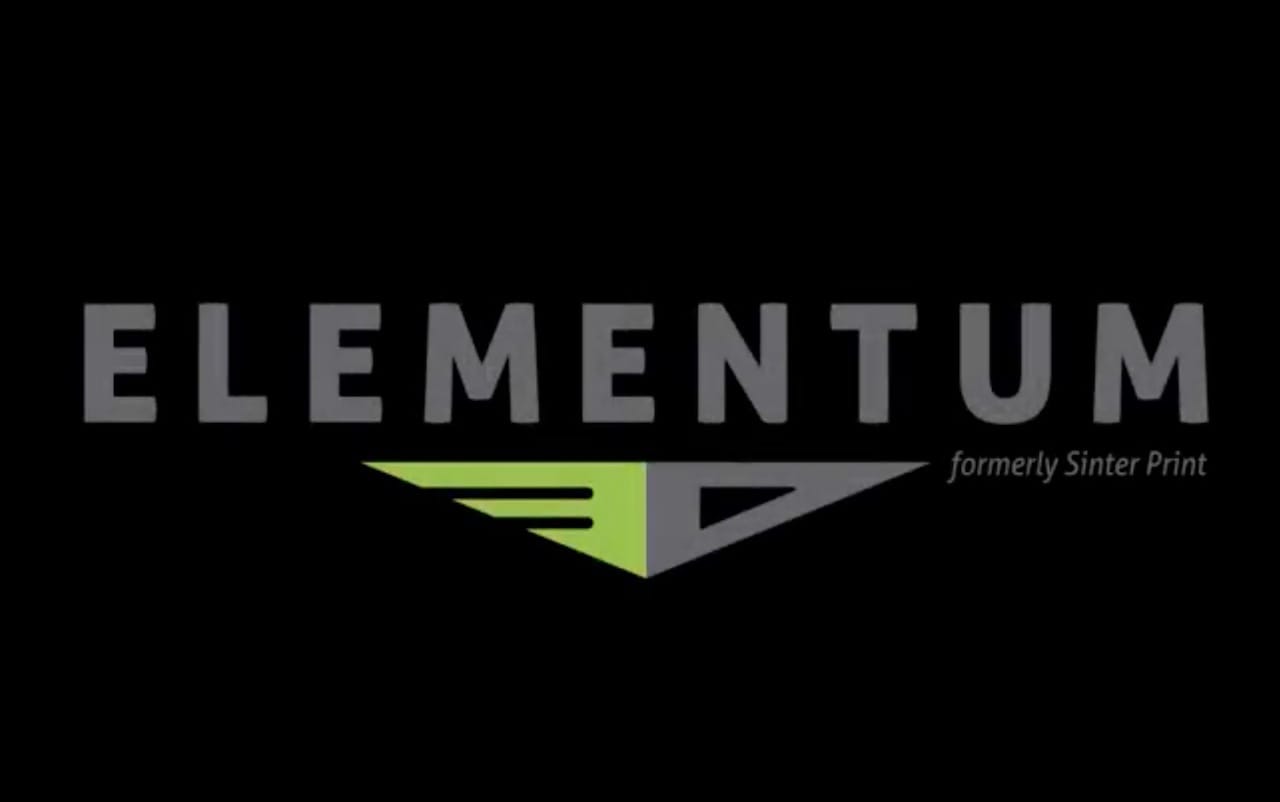
Market research firm IDTechEx predicts that the global market for 3D printing metals will hit $12 billion by 2028.
This growth in metal additive manufacturing (AM) will not only be due to greater adoption of the technology, as prices drop and new technology emerges, but also to the expansion of the materials portfolio itself.
Currently, metal materials for AM are pretty limited, particularly when it comes to powder bed fusion, the most widespread metal 3D printing technology on the market. This means that we’re going to see a number of initiatives established to make more metals available for powder bed systems.
Among the companies taking advantage of this new frontier is Elementum 3D, which is developing new metal powders for powder bed fusion that have some unique properties. ENGINEERING.com spoke with the company’s president, Jacob Nuechterlein.
Starting with Aluminum
After studying powder metallurgy at the Colorado School of Mines, Nuechterlein started working as a materials science consultant when he began to see the limited materials available in metal AM. It was then that he founded Elementum 3D.
“There’s thousands of materials to choose from, so why are there only six or seven metals for AM?” Nuechterlein asked. “Our goal was to expand the materials library for AM and found that the largest market was laser powder bed. That’s what we’ve been going after, developing new materials for laser powder bed from a couple of different techniques.”
The startup’s first material to be released is its aluminum metal-matrix composites (MMC), a metal matrix with a ceramic particulate dispersed within it. The only way it can be printed is through Elementum’s proprietary reactive AM (RAM) technique. “We use a technology called RAM and essentially we’re using solid-state chemical reactions to form different cross phases in the equipment,” Nuechterlein explained.
The use of ceramics in the composite means a stronger, harder, stiffer metal with great wear resistance. The aluminum MMC is similar to 7075 aluminum. It’s harder and stronger than the AlSi10Mg aluminum alloy typically used in 3D printing, and it’s even harder and stronger than steel. It also has a higher strength-to-weight ratio, comparable to titanium, but is less heavy, less expensive and faster to print.
Read more at ENGINEERING.com