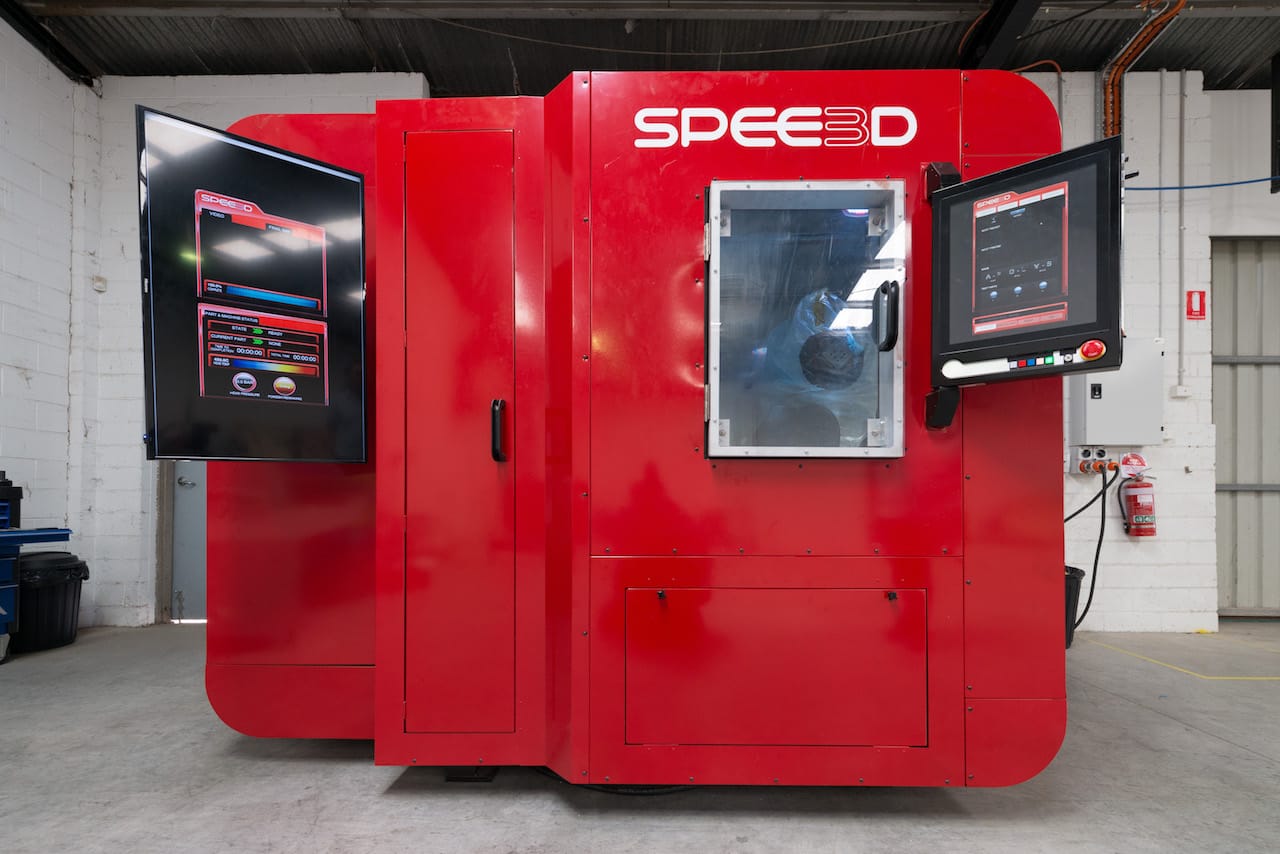
Australia-based Spee3D has developed a 3D metal printing process I haven’t seen previously.
Typical 3D metal printers involve high power lasers operating in oxygen-free sealed build chambers, blasting energy at expensive fine metal powders. This process indeed works very well, but it’s quite complex to perform, and as you might guess, quite expensive as well.
As a result a number of innovative startups have been pursuing alternative processes that can 3D print metal objects successfully and to the quality levels currently achieved by existing equipment.
Recently we’ve seen several startups develop far simpler means to achieve 3D metal printing, including Desktop Metal, Xact Metal, Markforged, Ability 3D, Aurora Labs and others. Many of these new processes involve 3D printing “cold” green parts, which are then sintered after printing to create the final metal parts. Few seem to be able to reproduce the current technology results by printing a metal part directly.
But then there’s Spee3D, who use a vastly different approach. They do use metal powder, but it’s actually standard metal powder that’s commonly available at commodity price levels, instead of the highly refined – and expensive – 3D printer metal powder used so often in other equipment.
How does Spee3D 3D print with this powder? They don’t use lasers, electron beams, but instead use “speed”, hence their company name. CEO Byron Kennedy explains:
The process is called supersonic 3D deposition (SP3D). We accelerate powders to supersonic speeds (3 times the speed of sound). When they a hit a surface they create a full density part.
The energy to melt the metal particles is kinetic!
The literally “supersonic” print head is mounted on a robotic arm that moves about to gradually lay down material to form a solid metal object.
But this demonstrates yet another advantage: by using robotic deposition, the Spee3D process is able to shift the orientation of the part during printing, virtually eliminating the need for support structures. This is quite important.
Why? Because when 3D printing in metal heat flows from the active zones of the print to the cooler areas, often through support structures. This can be good or bad: a delicate geometry might require quick removal of heat to avoid deformation, but in other situations you may want an amount of heat to remain to finalize the crystallization of the metal properly. It’s a science to figure out how to do this correctly, and many 3D metal printing workshops employ engineers to figure this out on each print.
But that doesn’t seem to be an issue with the Spee3D approach, as they don’t require support structures due to the orientation capability, and their process does not generate enormous amounts of heat. No warping!
Even better, the robotic approach does not require non-scalable cartesian gantries; the robot simply moves around within its reach to print parts. This means that the process can be scaled up to as large as required, so long as you have a suitably-sized robot.
Printed parts will not be perfectly finished, as you can imagine the spray of particles will not be particularly smooth. That simply means the finished part, if it requires a smoother surface, will have to undergo post-print processing, possibly by a CNC mill. This is also the case with normal cast parts as well.
One possible drawback to this approach might be the ability to 3D print very delicate structures in metal. It is possible that the spray approach may have a minimum structure size, as weaker structures might not support the blast of incoming particles at supersonic speed. There is also the issue of “missing” the delicate structure and having the particles embed themselves on background structures.
Nevertheless, this approach seems feasible and should be able to address the needs of a vast number of metal part producers at lower costs than other 3D print solutions.
Currently Spee3D offers the LIGHTSPEE3D, their first model, which has a 300 x 300 x 300mm build volume, sufficient for many metal parts. It uses common aluminum and copper powders, but I suspect the process might be workable with other materials in the future.
While the LIGHTSPEE3D is available for purchase today, the company has not yet announced pricing for the machine. They intend to do so at the FormNext conference in November, where we will certainly be onsite to see this machine in person.
Via Spee3D