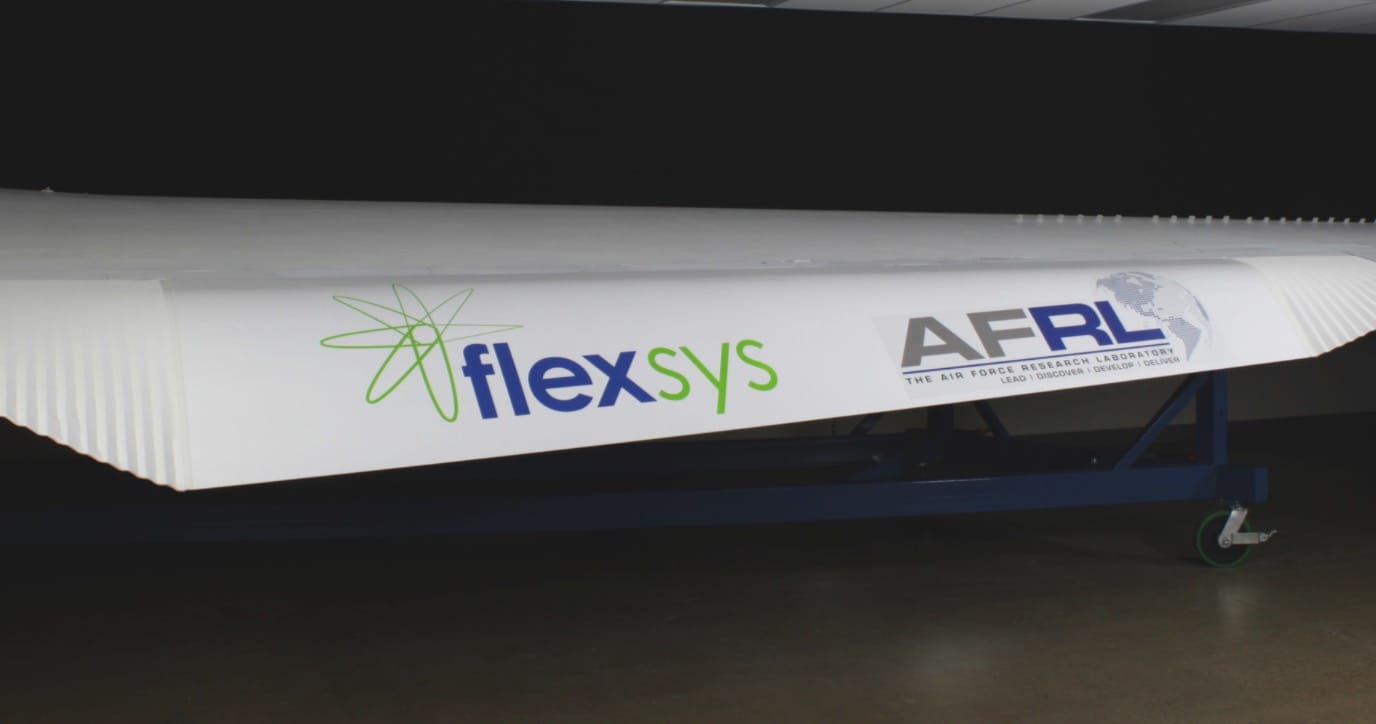
Recently we posted as story about Disney producing compliant mechanisms; it turns out another company is already producing them.
Reader Kevin Quigley asked if Disney’s project was different from the work undertaken by Michigan-based Flexsys. It turns out Flexsys does indeed produce compliant mechanism designs as well.
The concept of a compliant mechanism is a structure that contains flexible parts that enable the entire mechanism to articulate in functional patterns.
For Disney, this means they can produce more lifelike animatronic sculptures for their amusement parks, as we described earlier.
But for Flexsys, the concept is entirely different. It seems they are focusing on airfoils. The idea is that an airfoil can slightly deform to create a different airflow. Current airfoils are made from multiple articulated parts that roughly achieve this effect by tipping an aileron, for example.
This is very different than biological flight, where a bird will literally change the shape of its wing to develop different lift and drag characteristics, “on the fly”. However, manufacturing techniques were unable to replicate this advanced function until the advent of compliant mechanism technology.
That’s where Flexsys comes in: they seem to have developed a wing technology that approximates this effect through the use of a compliant mechanism. They explain:
FlexSys, Inc, approaches mechanism design by replacing multi-body rigid linkages with compliant flexible elements within a single component. We accomplish this by exploiting the elasticity of conventional materials (including high-strength steels, aluminum, titanium and composites) to create flexure and motion without compromising the strength and resilience of the material at hand. FlexSys design technology initiates small forces within a proprietary internal geometry that morphs a single-body “monoform” from one desired shape to another and back again.
Our technology spreads actuator forces throughout the whole geometry to distribute compliance without localizing strains in any focused region. This enables FlexSys to achieve remarkably complex shape morphing with less weight while maintaining exceptional strength and reliability. Because of their strength, our designs stay safely within conventional life cycle limits, are highly reliable, and still very cost effectively while offering major enhancement and new functionality.
But back to the question whether their approach differs from Disney’s. Here is how Flexsys creates their morphing shapes:
FlexSys’ design approach and the associated software take into account a desired manufacturing method during structural design and optimization. These mass-manufacturing methods include stamping, casting, extrusion, injection molding, composite molding, etc.
Disney is apparently using 3D printed approaches to develop compliant mechanisms. So the answer is that compliant mechanisms can be made using a variety of making methods.
We prefer 3D printed approaches, of course.
Via Flexsys