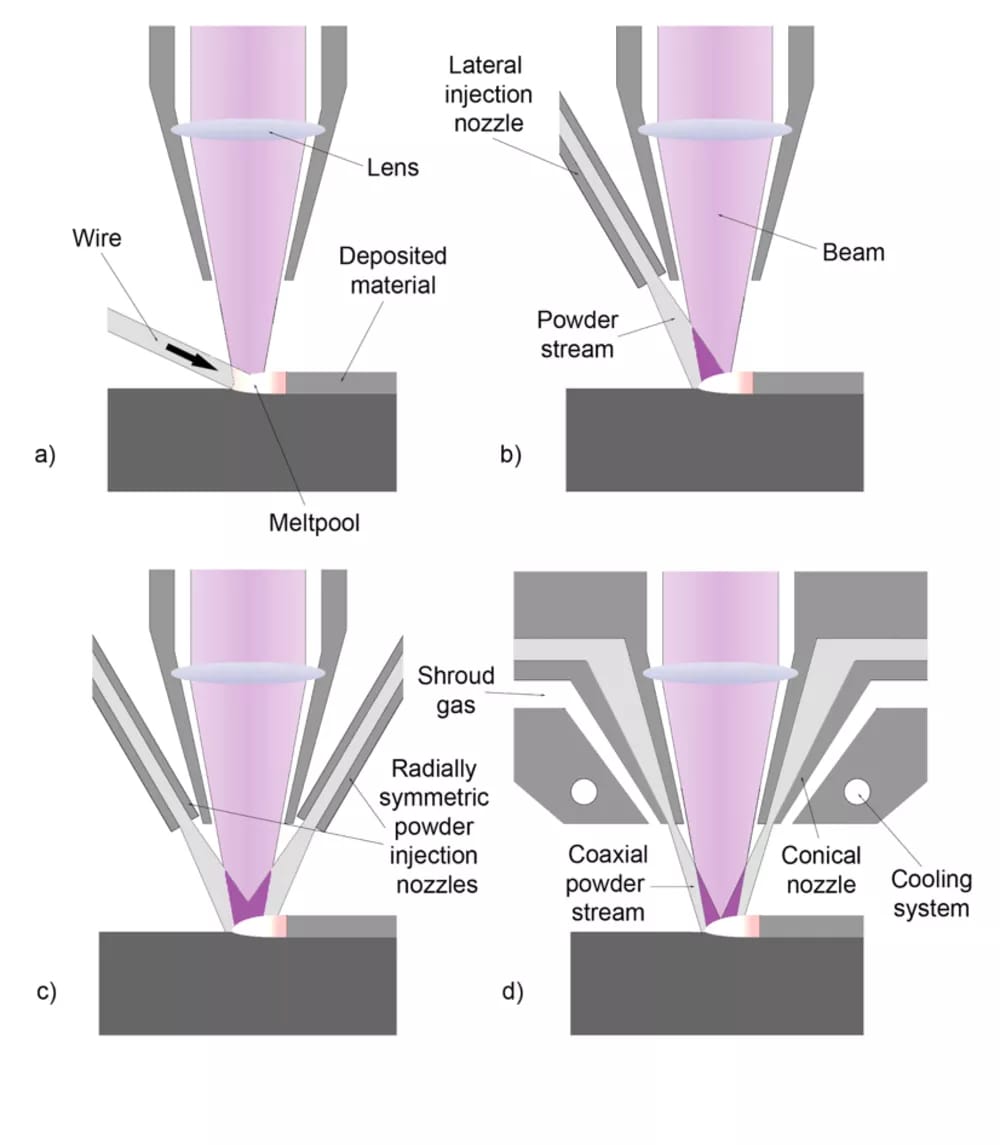
For some engineers, 3D printing may be coming on in an unwelcome rush.
Pressured by management forces who have read how additive manufacturing (AM) will save the world, reducing a hundred-part assembly into one part, or making super-lightweight parts with only skins over lattices, the engineers are subjecting the 3D-printed components and process to the microscope and, in some cases, have found them wanting.
Background
The dominant form of metal 3D printing is powder bed fusion, in which an energy source—a laser in the case of selective laser melting (SLM) or an electron beam in electron beam manufacturing (EBM)—fuses particles of metal powder together point by point, layer by layer until an object is complete. Powder bed fusion systems have mechanisms for controlling the energy source and the distribution of powder.
Directed energy deposition (DED) and binder jetting are also used to 3D print metal objects. In the case of the former, powder or a metal wire feedstock is introduced to an energy source. In the case of the latter, a liquid binder is deposited onto a bed of metal powder. After the print is complete, the object is heat treated and sintered in a furnace.
In the metal 3D printing process, a number of issues can occur that machine operators attempt to avoid. These include porosity, residual stress, density, warping, cracking and surface finish.
Surface Finish
Before a 3D-printed metal part hits the showroom floor or the fuel chamber of an engine, it has already undergone significant post-processing in the form of CNC machining, shot peening or sandblasting. That’s because the metal 3D printing process is a bumpy one when it comes to surface finish.
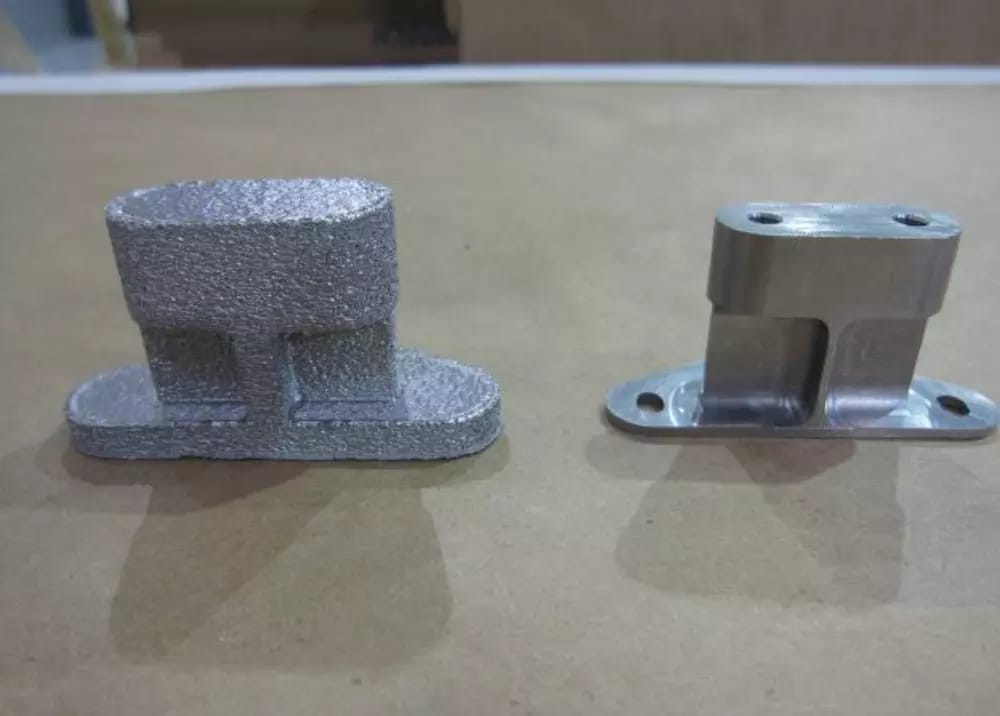
Due to the nature of the process, DED typically produces near-net-shape parts that must be CNC machined to meet specifications upon printing; however, powder bed fusion parts are somewhat closer to their final shape when produced. Nevertheless, the surface finish is still rough. To reduce this, finer particles of powder and finer layer thicknesses can be printed.
This, however, drives up the cost of the material. Therefore, there may be a tradeoff between surface finish and cost. Because all powder bed fusion parts will be refined to specification during post-processing, it sometimes makes more economic sense to use slightly larger particle sizes anyway. This also means that surface finish is less important than some of the other issues that can occur in metal 3D printing, since the part will undergo some level of post-processing regardless of how smooth or rough the end part is.
Porosity
Porosity occurs when very small cavities form within the body of a part as it is being printed. This can be caused by the 3D printing process itself or even from the powder used in the process. These microscopic holes reduce the overall density of the part and can lead to cracks and fatigue.
During the powder atomization process, gas pockets can form within the powder feedstock, which will then be transferred to the final part. For this reason, it’s necessary to purchase materials from a reputable supplier.
More often, pores can occur within a part due to the 3D printing process itself. When not enough power has been applied, the laser intensity is too low for example, the metal particles may not fuse adequately. When too much power is used, on the other hand, a phenomenon known as spatter ejection occurs, in which melted metal flies out of the melt pool and into adjacent areas.
Pores may also be formed when powder particles are larger than the layer thickness of a part or if the powder is too loosely packed. It can also occur if melted metal does not flow adequately into the desired melt region.
To address these problems, most machine operators basically have to tune their machines for a given material and print job. The machine parameters, such as the power, spot size and spot shape of a laser, will be modified for a given material and print job until porosity is minimized.
Porosity may also be reduced in power bed fusion processes through the use of an “island scanning” pattern employed by the laser. This checkerboard pattern features alternating unidirectional fills to reduce temperature gradients by distributing the heat.
In SLM, the shape of the laser can be modified to reduce spatter ejection. Known as “pulse shaping,” it’s possible to heat the melt area gradually. For EBM, powder particles can be ejected from the powder bed by the electrical charge. This can be reduced by quickly scanning the print bed and the diffuse beam to perform pre-melting of the powder.
Jim Gaffney, additive metal/DMLS lab manager at Forecast 3D, gave this advice for reducing porosity: “With the SLM process, density of over 99 percent can be achieved with quality raw materials, the proper build parameters and an environmentally controlled machine lab. Hot isostatic pressing treatment as a post-process can aid in the removal of any remaining porosity in final parts.”
It may also be possible to infiltrate powder bed fusion parts with another material, such as bronze. However, the use of auxiliary materials will naturally affect the chemistry of the primary metals, potentially disrupting the desired application of the part in the first place.
Density
The porosity of a part is inversely related to its density. The more pores a part has, the less dense it is and the more likely it is to experience fatigue or to crack under pressure. For critical applications, a density of above 99 percent is required.
In addition to controlling for porosity through the methods mentioned above, particle size distribution may aid in increasing the density of a printed part. Spherical particles will not only improve the flowability of the powder, but can also improve density. Additionally, a wider particle size distribution allows fine particles to fill spaces between larger particles, resulting in higher density. Unfortunately, this may decrease the flowability of the powder.
Flowability is necessary to ensure an even, densely packed layer of powder, which, as you might guess, affects both the porosity and density of a 3D-printed part. The more tightly packed a layer is, the denser and less porous the final object will be.
Jack Beuth, a professor in the department of mechanical engineering and the director of the CMU NextManufacturing Center at Carnegie Mellon University, was able to shed light on the advances being made in defining the parameters associated with porosity and density in metal 3D-printed parts.
“Maximum density (which translates to minimum porosity) is important as manufacturers move toward fabricating parts that will be subjected to cyclic (fatigue) loading in their applications,” Beuth explained. “In research carried out within our NextManufacturing Center, we have demonstrated that porosity from a variety of sources can be controlled and effectively eliminated by manipulating AM process variables. There is no one process that is particularly better at avoiding porosity than others, but for each process, there are combinations of process variables (we define them as a ‘processing window’) that do so.”
Read more at ENGINEERING.com