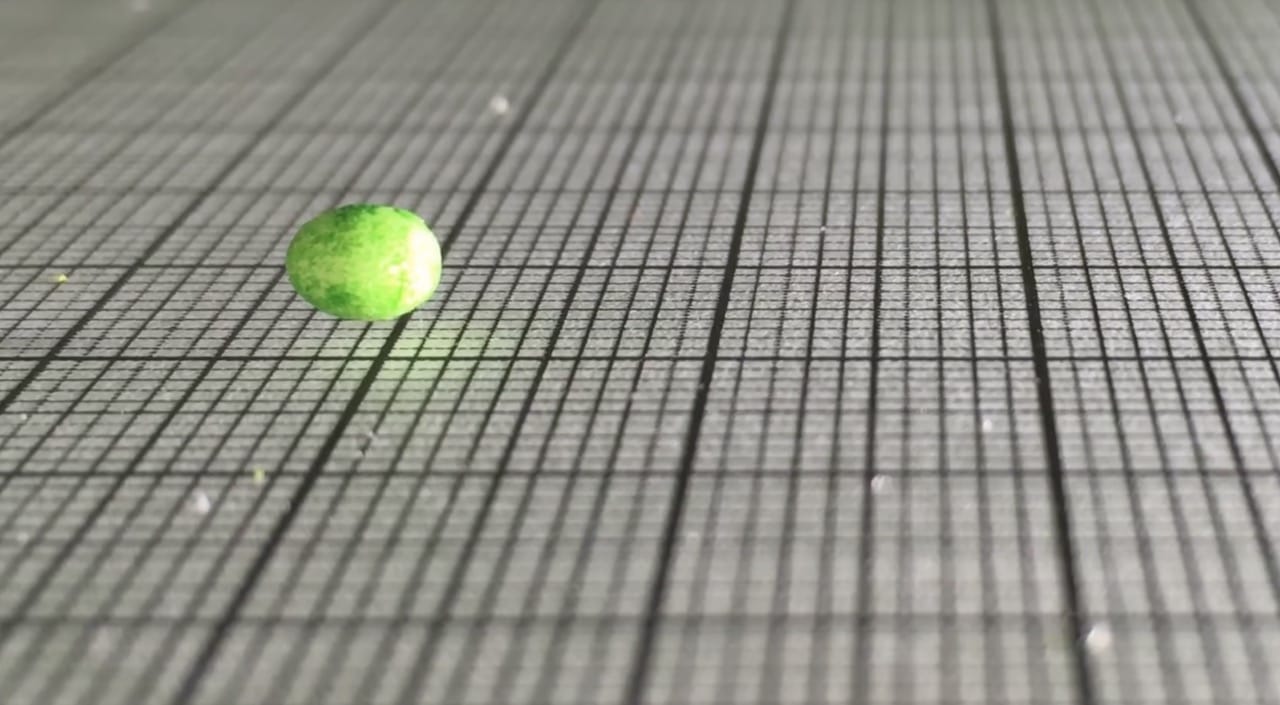
I’m reviewing a video of a new concept called, “ultrasonic 3D printing”.
It’s a fascinating technology in which banks of tiny ultrasonic wave generators face the interior of a build volume. These generators are individually controlled and can then be configured to produce varying pressure waves within portions of the build volume.
These pressure waves can then manipulate small objects within the build volume. In other words, this is like an invisible robot arm that can grab items and move them around with CNC-like precision.
The example shown in the video below illustrates how this could work. They’ve used as an example the assembly of a printed circuit board, where the electronic components are dropped into the build volume and then moved into position on the board. A separate laser then blasts their connections, melting the solder to perform the component installation.
After a few maneuvers of this type, they’ve completed a working printed circuit board.
This is pretty amazing, but I am at a loss to understand how it is 3D printing. It seems to be automated 3D assembly with a contactless approach.
How could you make a plastic object, for example? While you could move small chunks of input plastic into rough position, and then melt them with a laser, this would seem to be an incredible tedious approach, and one that wouldn’t have particularly great print quality.
Perhaps the researchers envision a far more precise system with zillions more generators capable of depositing a stream of sand-like material with a laser fusing the material as it drops? That doesn’t seem to be the case in the example shown.
Nevertheless, I believe this system could be of great interest to 3D printing, not as the core 3D print engine itself, but as a kind of accessory that could supercharge print operations.
Consider this: if a standard 3D printer build chamber were equipped with such generators, then objects could be easily installed in mid print.
Embeddeding items has long been a method for making hybrid objects, as we wrote four years ago.
But that was a manual approach. You had to stop the machine and then manually drop your nuts and bolts into the part, then restart the printing. The printer really had no idea embedding was taking place.
But what if it could? What if the print was automatically paused and parts were swiftly moved into place within a print?
I believe this could open up a huge set of possibilities for future designs. Not only would the designs be interesting, but the assembly process would be simplified, leading to additional deployments of 3D printers in production environments.
Ultrasonic assembly? That could be a powerful sidekick to 3D printers of the future.
Via YouTube