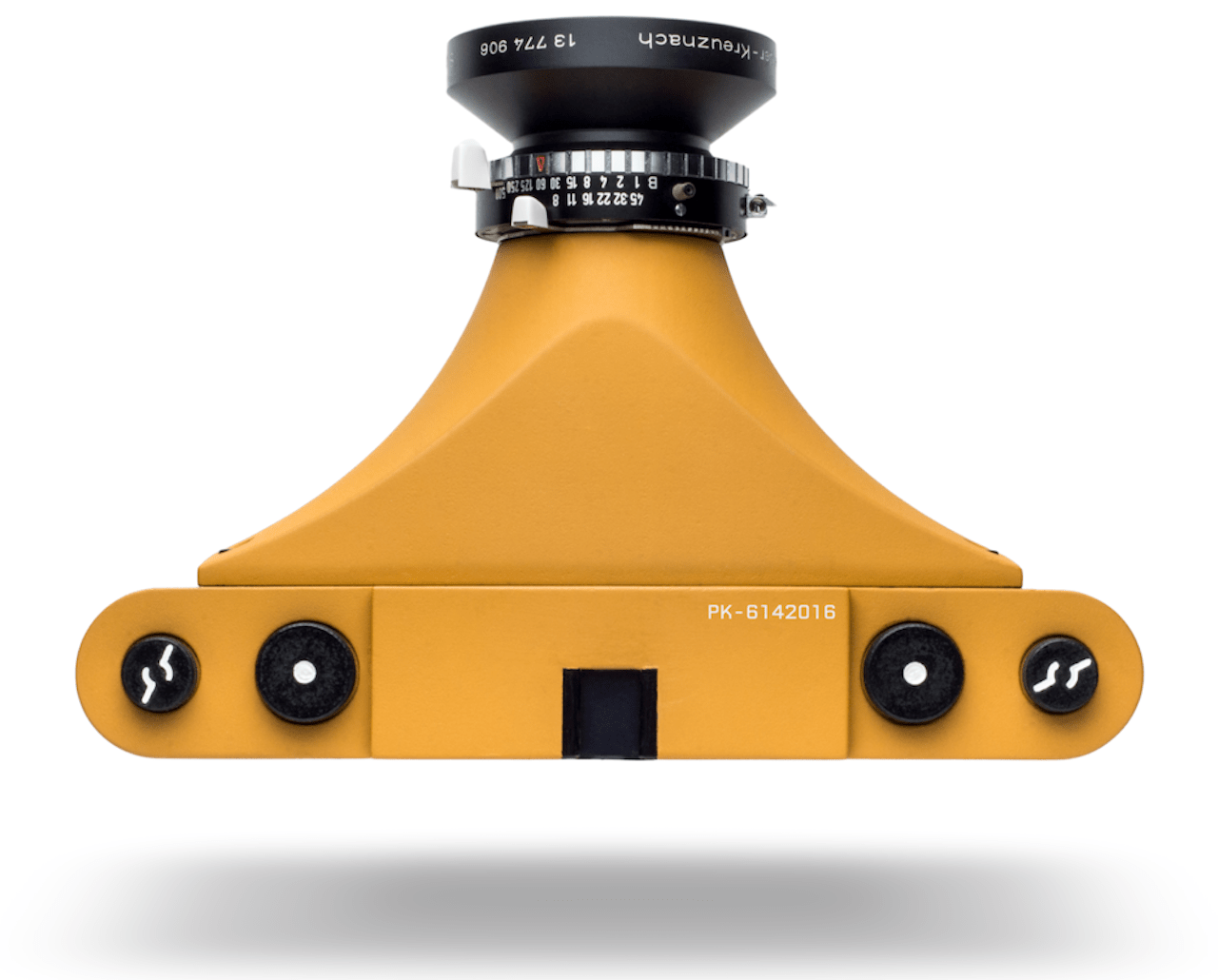
I’m reading an interesting story about how a photographer designed and 3D printed a specialty film camera, and realized what this actually signifies.
The camera project in question was undertaken by Paul Kohlhaussen, a photographer and designer based in London. Kohlhauseen, like some professionals, has an affinity for the older film approach to photography, over the current trend in digital.
He explains his dilemma and solution:
I have quite a passion for film photography. It calls for a slower, more deliberate creative approach and produces tangible results. I could rave on about my ideal equipment for hours – a Mamiya 7 for the practical take on medium format, a Hasselblad XPan for the panoramic frame size and of course the Leica M series for its iconic design. At the time of starting this project I had no way of affording any of these cameras – so I decided to amalgamate their desirable qualities into a single device of my own.
The camera, called a “PK-6142016, also known as the Cycloptic Mustard Monster”, is able to capture 60 x 140mm images on 120mm film.
Kohlhaussen then fired up Autodesk Fusion 360 and designed a camera to these requirements. But the design itself required some thinking:
This project makes use of a Schneider Kreuznach 90mm f/8 Super Angulon lens, intended for use on 4×5 cameras. The lens’ optical properties dictated the dimensions of the camera’s bellows and focusing mechanism. The latter works by inserting fixed spacer brackets between the bellows and camera body, allowing for the focal plane to be drawn nearer in preset increments. Loading the film is done by removing the body’s top plate, similar to removing the bottom plate on a Leica. The next step is to print the viewfinder that will attach via the cold shoe mount.
Kohlhaussen’s camera project was a success; he 3D printed the eight parts required in nylon, and they fit together well enough to produce some amazing images like this one (more on his site):
This is quite an accomplishment; an expert in a field was able to create an entirely new piece of equipment through the capabilities of 3D printing and related technologies.
But here’s the catch: Kohlhaussen knew enough about the domain to enable him to intelligently design the new camera. He also had to know how to use Fusion 360.
I’ve seen this pattern before, and it’s most evident if you browse the subreddit r/functionalprint. It’s full of examples of inventive folks designing workarounds for problems, replacing missing or inadequate parts, or something entirely new.
But in each case there’s a common pattern: someone with a need who knows how to go about designing a solution.
That’s the winning combination, but unfortunately most of the public loses out on two counts: they generally don’t know enough about a domain to conceive of a solution, and secondly they don’t know enough about design or design tools to create a feasible solution.
So it ends up that while 3D technology is extremely powerful, it can only be effectively used in this way by professionals or consumers with sufficient training and expertise in a particular domain.
Perhaps this suggests 3D modeling and printing should be a more mandatory subject in school? What if EVERYONE was able to do things like this?
We’d have a great deal more innovation, that’s for sure.
Via Paul Kohlhaussen