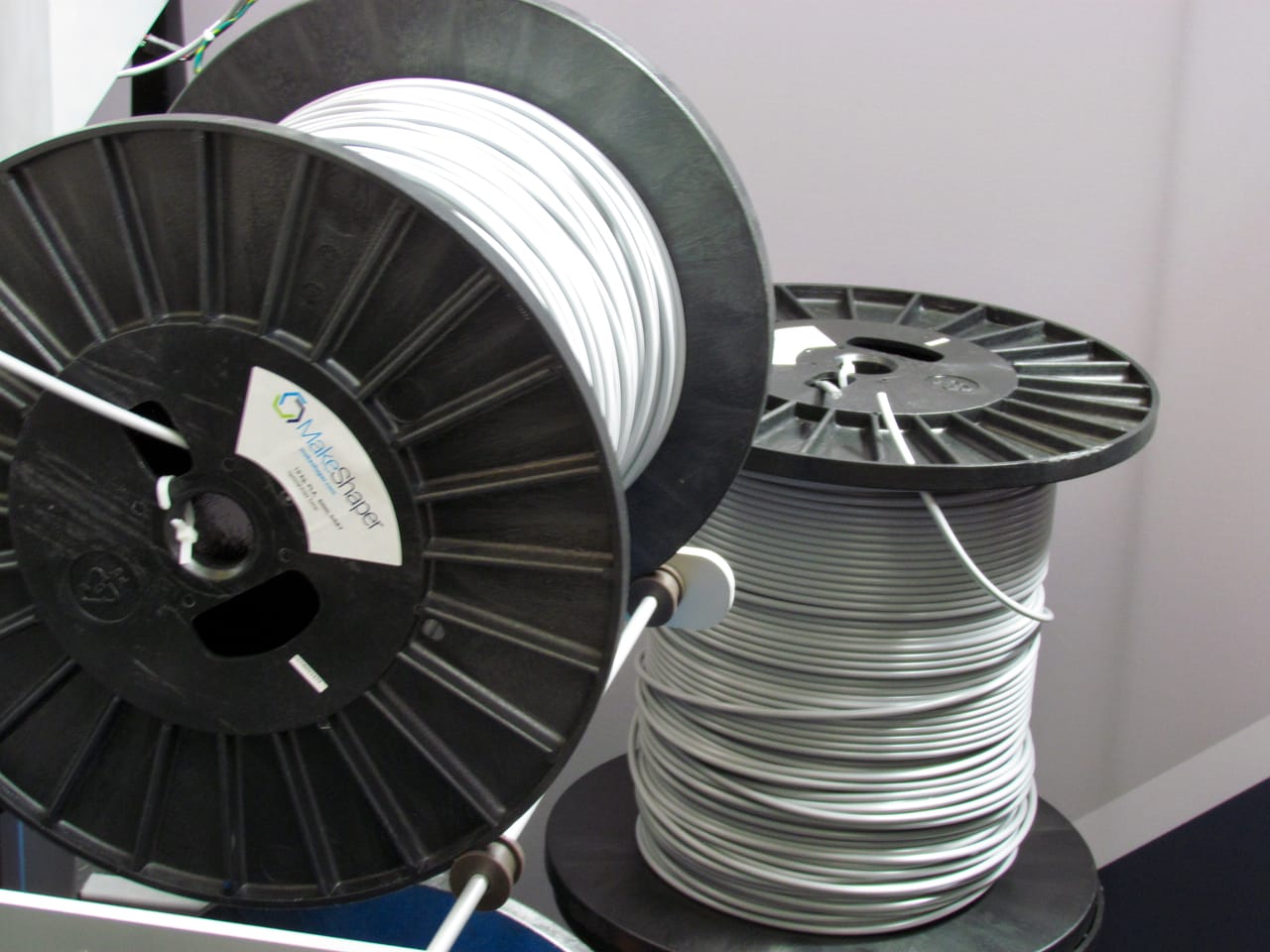
3D Platform has a problem they’d like to solve, but they really need the cooperation of others in the 3D printing industry.
Their focus is on very large scale 3D printing equipment, made possible by scaling up the standard desktop style equipment to sizes of a meter or more. This enables them to 3D print larger objects, some the size of furniture.
However, one of the issues they – and other large format 3D printer manufacturers – face is the extraordinary lengthy print times required to produce such big objects. In some cases, you might wait a week or even more to complete a large 3D print!
Such long prints are risky, as the longer a machine runs, the more time there is for something to go wrong. The last thing you need is a massive 3D print to fail half-way through, wasting a week of time and a great deal of 3D printer filament.
3D Platform has attempted to address the problem by re-designing their fancy extrusion systems to increase the flow of plastic significantly.
This certainly works, but the mechanics of the extruder are only one factor involved in increasing plastic flow.
The other major factor is the plastic itself. While the company has experimented with an alternative delivery system, plastic pellets, they found it not optimal:
Some research has been done to allow pellet-fed extruders to be used on FFF machines. To date, the only production machines available with pellet-to-part extruders have print volumes in excess of one cubic meter. The pellet-to-part production process adds many additional process variables that need to be controlled to produce parts with consistent quality.
Also, pellet-fed extruders require additional upstream processing equipment (inspection equipment, material driers, volumetric feeding, etc.) and have higher change-over times than spool-fed extruders.
So they’d prefer to use pre-made spools of plastic filament, as has been done since the dawn of desktop 3D printing. However, the industry has more-or-less settled on using two sizes of 3D printer filament: the most popular size is 1.75mm, which is very useful for small machines printing in fine details. The other de-facto standard size is 2.85mm, which is most often used in Bowden-style machines that must push a rigid filament through a long tube.
3D Platform’s advanced extruders are capable of taking up a lot more plastic than can be supplied with mere 2.85mm filament, so they’re looking big.
At top you can see an experimental 6mm filament spool. I inspected this spool and found that the plastic is quite rigid and I’m not sure it would easily bend through a complex path to an extruder successfully. 3D Platform found similar results for stiff materials and eventually tried a small 4.5mm size.
But here’s the problem: while they can figure out the optimal size for this large-volume printing, where would you buy such filament? I don’t know where you can get 6mm filament, let alone 4.5mm filament, unless you custom order it.
As a result, there is going to be a need for larger-size filament for not only 3D Platform, but for other manufacturers of large-scale 3D printing equipment.
Unfortunately there are no standards bodies in place in the industry to determine what a standard might be. So 3D Platform has formed a consortium of their own to figure it out.
So far they have partnered with:
- 3D Platform
- 3DXTech
- E3D
- Essentium
- Titan Robotics
- MakeShaper
- Ultimaker
- PolyMaker
- Push Plastic
This is a good start, but it doesn’t include other large-format 3D printer manufacturers such as BigRep, at least yet.
I am rather curious about Ultimaker’s presence on this list, as they do not (yet) make a machine of large size.
I believe this is a very good step forward, as part of the 3D printing community is trying to set up its own standard, rather than simply adopting standards set by some other unrelated industry.
If their large-format standard catches on, then we may see an easier path for vendors to create large-format 3D printers.
Via 3D Platform