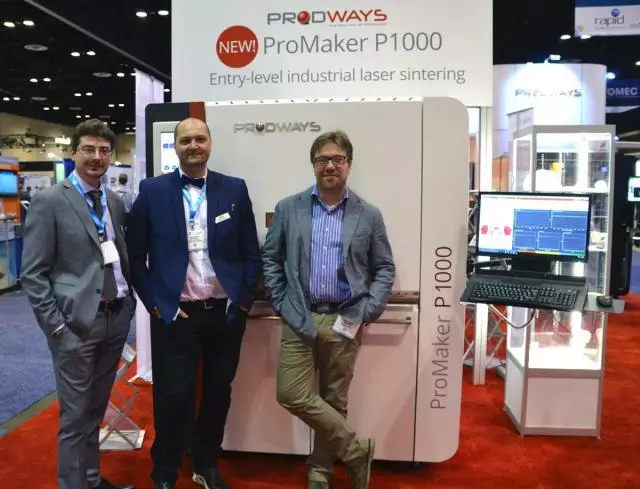
With the expiration of each 3D printing patent comes a new wave of affordable systems.
In 2009, the expiration of key fused deposition modeling (FDM) patents led to the desktop explosion begun by the RepRap community. This was followed by a slightly smaller explosion of stereolithography (SLA) and digital light processing (DLP) systems when other patents expired a few years later.
The desktop selective laser sintering (SLS) explosion has been significantly smaller. While key patents expired about three years ago, only three companies have been able to bring costs down to affordable prices: Sintratec, Sinterit and Sharebot. To learn why this is and what this new low-cost SLS will bring to the industry, ENGINEERING.com spoke each of them.
Why SLS?
SLS works by zapping a laser at a bed of thermoplastic powder, usually nylon, fusing the particles together layer by layer. Due to the use of a bed of powder, objects printed with SLS don’t require the addition of support structures, as is the case with FDM, SLA and DLP. This makes printing objects with overhangs of over 45 degrees much easier.
Moreover, hollow objects and moving assemblies can be 3D printed because, once a part is excavated from the unsintered powder, often in a separate part-removal chamber, any cavities filled with such material can be emptied out through holes designed into the part’s CAD file. Although SLA can produce fragile objects and FDM components may be weak in the Z-axis, parts printed in SLS may be robust enough for functional use and are detailed enough for prototyping applications. Additionally, it’s possible to make parts with high ultraviolet and temperature resistance.
News of low-cost SLS began to emerge in 2014, when a company called Norge Systems launched a Kickstarter to fund the manufacturing of its Ice1 and Ice9 SLS 3D printers. Norge, however, was acquired by Prodways, a French company with an increasingly broad product portfolio. With the purchase, Prodways was able to release the first professional SLS machine priced under EUR€100,000 (USD$113,170).
Though less expensive than other industrial SLS systems, Prodways’ ProMaker P1000 may still be beyond the grasps of many small businesses. Fortunately, just a week after the Norge Kickstarter began, details were released about an Italian company’s foray into SLS 3D printing.
Sharebot is Italy’s largest desktop 3D printing brand, with a broad portfolio that includes a variety of FDM, SLA and DLP 3D printers. This range is in part due to the existence of an R&D group within Sharebot, something that not every desktop 3D printer manufacturer has.
“When we started Sharebot, we had a dream of understanding all of the technologies, so we started a small R&D group inside of Sharebot to study all of the technologies,” said Sharebot CEO Arturo Donghi.
Sharebot may boast a small R&D group, but it would not be alone in the race for desktop SLS. Soon after it was revealed that the Italian firm was building one, a Swiss startup called Sintratec took to Indiegogo to fund the production of the EUR€4,999 (USD$5289.94) Sintratec Kit. Several months after the crowdfunding campaign for this kit was successfully funded, a Polish company known as Sinterit came onto the scene promising its own low-cost SLS machine.
https://www.youtube.com/watch?v=hS1mSxF3QeY
Sintratec, as well as Sinterit, pursued SLS because the startups’ founders just weren’t satisfied with the quality of the parts made with other 3D printing technologies. Sintratec co-founder and head of operational management and software development Dominik Solenicki explained how he and two other engineers began their Swiss firm in 2014.
“We were very let down by the existing small-budget 3D printing offerings,” Solenicki said. “The promises we were told that 3D printing should bring just didn’t hold up with what we were able to get. But once we found laser sintering, there was no holding us back. We needed to get our hands on this awesome new technology. Sadly, system prices started at well over USD$100,000. Initially the only way for us to have our own system was to build it. After getting started, we made it our mission to change that high entry barrier and enable enthusiasts and small businesses to enjoy the real world of additive manufacturing!”
Konrad Głowacki co-founded his Polish desktop SLS company Sinterit after years of working for Google as a software engineer, developing the tech giant’s internal marketing tools. “After some time, I came across an article regarding patents all around the business and learned that some SLS patents were about to expire,” Głowacki said. “Together with Paweł [Szczurek], we decided to see if we were capable of creating an SLS demonstrator.”
Building an SLS Machine
It’s been some time since these stories broke, but we have yet to see a proliferation of desktop SLS 3D printers like FDM and SLA. The biggest reason for this is that there isn’t a lot of documentation on the technology. SLS was protected technology manufactured by companies like EOS and 3D Systems, ensuring that intellectual property could be protected by those firms, but also giving them control of the technology, as well as its price on the market.
“It’s not easy,” Donghi said. “The problem is that there is no technical documentation. We had to test and test and test. It took us two years to develop our SLS 3D printer. There were two main problems: one problem was mechanical, the ability to control temperature, the process parameters and so on, and the other problem was with the software because we have to be able to control the movement of the laser.”
Głowacki said that Sinterit also relied on a trial-and-error approach, a process that took almost two years. “At first, we had no idea how SLS worked,” Głowacki explained. “Everything that we found out was trying and failing or trying and succeeding. At some point, I stopped counting failures. At first, we had no idea how SLS worked, other than there is a powder of this type and a laser, and over time, we built our own knowledge.”
Sinterit’s approach to developing the technology was an interesting one, which actually took advantage of open-source 3D printing to pull off. “The first prototype was 3D printed on an FDM machine, a Prusa i3 RepRap,” Głowacki said. “I bought the SLS and the laser in the United States. I had to carry the laser in my backpack to get it to Poland because it was hard to get them to ship it to Poland. Unlike it is now, it was extremely hard at that time to get anything like that sent to us. Now, though, you can buy easily. Material isn’t only sold in hundreds of kilos or in tons, but in 20 or 50 kilos.”
Sintratec had been performing several years of research and development before coming to market. According to Solenicki, the main obstacle was also the need to start from scratch. “We had to invent the complete toolchain necessary for lowcost laser sintering,” Solenicki explained. “We created custom electronics, control systems for the laser scanning and complicated temperature control, firmware for microprocessors, lots of software for the handling and processing of 3D files and all the hardware involved in creating a complex and high-performing system. The upside is that we can support our customers in every area. We control the whole toolchain from the bottom up and as such are able to build excellent products.”
The Sharebot SnowWhite
Sharebot was the first company to get a desktop SLS machine to market with SnowWhite, which first began shipping to customers in 2016. The company has since installed 25 machines worldwide. Unlike the desktop machines from Sintratec and Sinterit, SnowWhite features a CO2 laser, the same type of laser installed on the high-end professional machines.
SnowWhite uses a 14W CO2 laser, which is about half as powerful as the 30W lasers featured on EOS FORMIGA P 110, the smallest and least-powerful EOS machine. (Image courtesy of Sharebot.)
SnowWhite uses a 14W CO2 laser, which is about half as powerful as the 30W lasers featured on EOS FORMIGA P 110, the smallest and least-powerful EOS machine. (Image courtesy of Sharebot.)
Donghi explained, “It’s exactly the same as a 3D Systems or EOS machine—the same type of laser and parameters, but cheaper. It can print with any thermoplastic powder: PA12, PA11, TPU and most other materials on the market. There are many, many sensors inside, some thermocouples and some infrared sensors. All of this information is displayed to the user.”
Unlike high-end machines, SnowWhite is a desktop system, giving it strengths and limitations. Donghi pointed out that the machine has two tanks built directly into it, one for powder and one for part removal, making it truly a desktop system. At the same time, the build volume of 100 x 100 x 130 mm is a tight one for fabrication of substantially sized parts. As a result, most of the applications are for the development of new powders.
“For the most part, our customers are universities and R&D departments at businesses in the medical and chemical industries,” Donghi said. “They use it to test new powders because it’s easier. SnowWhite has the same parameters as larger machines, but in miniature. It’s very easy to use, and it’s easy to change powders. SnowWhite is the only SLS printer with a CO2 laser in the world that can print with only 200 grams of powder.” This is opposed to filling an entire powder tank with material that may not be used during the printing process, as is the case with larger industrial machines.
Donghi also emphasized the openness of the machine. Not only can customers modify the machine parameters easily, including the laser’s speed and powder, but they can also use powders from third-party vendors. The same is true of the resins and filaments for Sharebot’s SLA, DLP and FDM machines. “We don’t sell materials,” Donghi said. “We tell our customers to buy materials from 3D Systems or from EOS. That’s one of Sharebot’s philosophies. We don’t want to oblige our customer to use our materials.”
Read more at ENGINEERING.com