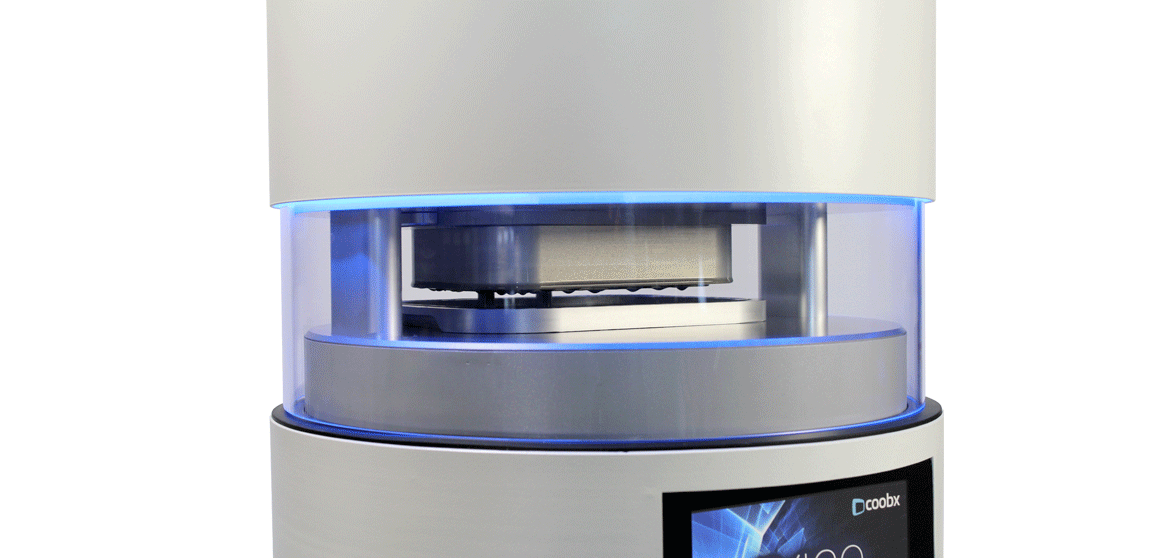
A small company has produced what appears to be a very attractive option for high resolution 3D printing.
Coobx, a small Liechtenstein-based company, has developed the Exigo 3D printer, available in two different versions. The company may be new on the 3D print scene, but apparently their team been developing complex manufacturing machines for decades, including resin handling for high-volume DVD replication lines. Coobx’s Marco Schmid explains:
The core team and founders come from the machine tools and semiconductor business and produced for them a lot of things. The core business has been fluid handling and filtration systems for the machine tools industry, where we’ve learned all about viscosity, physical properties, handling possibilities and so on.
This puts them in an excellent position to develop a powerful 3D printer for industry, and that seems to be what they’ve done with the Exigo.
The key element of the Exigo is what Coobx calls “LIFT Technology”, which seems to be a highly optimized version of stereolithography. This diagram hints at how it works:
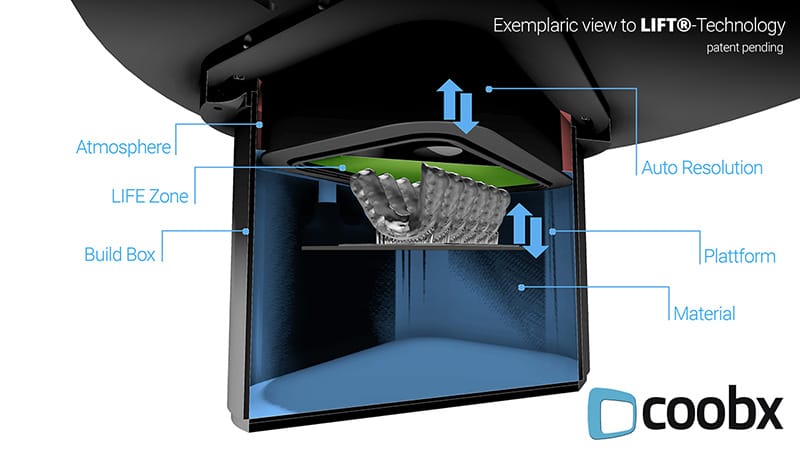
At the bottom is a vat of resin (which, by the way, they also produce specifically for their process). Above the surface is what they call the “LIFE Zone”, where the building takes place when the light engine selectively illuminates portions of the liquid resin surface.
As building takes place, the platform moves down into the resin, exposing another layer for illumination. When the print is complete it is entirely submerged and rises dramatically out of the resin, hence the name “LIFT” technology.
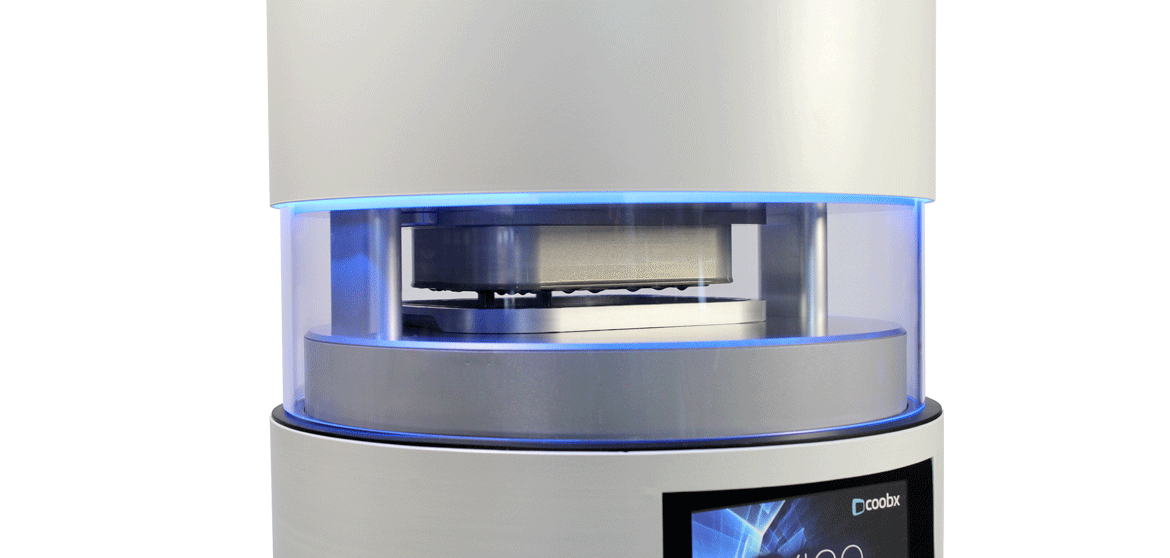
This approach is somewhat different than most of the recently released resin-based 3D printers, which tend to illuminate from the bottom through a transparent resin tank. The bottom-up approach generates a number of issues, however, including gradual wear on the tank bottom and “sticking” that slows printing.
A few other vendors use the top-down approach as Coobx does (such as Gizmo 3D Printers), but Coobx is different as they seem to have incorporated a number of interesting optimization features.
Their light engine is LED-powered, unlike the laser systems used by others. This suggests a speed advantage as the LED system could potentially illuminate an entire layer simultaneously, while a laser would have to laboriously trace all the elements.
Their expertise in chemistry and resin curing has allowed them to, for example, vary the resolution dynamically to speed up the printing process. Their automated focusing system can vary the XY size of illuminated pixels from 0.01 – 0.04mm.
The printing process on the Exigo is also near-guaranteed, as they explain:
Overcuring? Wrong settings? No more! An integrated algorithm calculates on every single picture frame to optimal curing time, layer height and build speed. These settings are optimized for all our Coobx materials to get productive parts out of the box
They can also vary the print speed to match the chemical and mechanical properties of each specific 3D model as it prints. Apparently the combination of these features permits the machine to print at the incredible speed of over 300mm per hour. How do they do this? The machine includes a powerful onboard processor that performs real-time calculations.
Of course, speeds will be dependent on the specific geometry in question, but nevertheless that seems awfully fast. For example, you could print a thin tower of 300mm quite a bit faster than a full-sized brick of 300mm. Perhaps the industry needs to come up with a better speed metric for such claims, maybe based on volume rather than height.
I’m wondering if the Exigo exhibits continuous 3D printing, as touted by a select few other resin 3D printer vendors. It would seem entirely possible with this setup and certainly the company would have the knowledge to do so based on the sophistication of their printing process optimizations.
Aside from the printer itself, the company provides a sophisticated slicing system that generates optimized support structures. They also provide a matching post-processing unit that cleans and final-cures completed prints in an optimal manner.
The company focuses heavily on materials, as they say their process is capable of printing “every kind of material” with its “integrated homegenisator” and custom light engine. So far the company has released this very impressive set of materials:
- Coobx Cast
- Coobx Gingiva
- Coobx Guide
- Coobx Model
- Coobx Tray
- Coobx Splint
- Coobx Denture
- Coobx Ceramic
- Coobx PU-R – rigid
- Coobx PU-F – flexible
- Coobx PU-E – elastic
- Coobx Standard – acrylatic
- Coobx SR – acrylatic, rigid
You’ll notice two themes in this list of materials: both medical and industrial use. And that leads to the two different models of the Exigo: Medical and Industrial.
As far as I can tell, the two machines are physically identical beyond the build volume. Each has a 154 x 86mm XY build area, but the Medical Exigo has a shorter Z axis of 110mm vs 340mm in the Industrial version.
What is the price of these machines? I can’t say, as the company has not yet released either the pricing or full specifications. We’re told they are planning to do so in the near future, and also to expect their pricing to be in line with their competitors.
Via Coobx