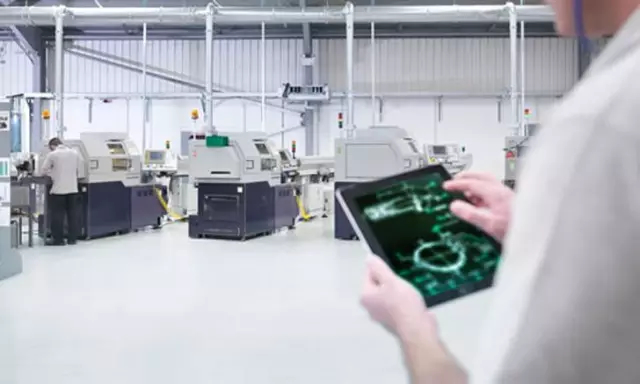
As 3D printing shifts from a prototyping tool to a production technology, manufacturers will be required to find ways to incorporate additive manufacturing (AM) into their existing workflows.
From a logistical standpoint, this means having software and management tools that are capable of handling the wide variety of AM processes used and validating and certifying the parts made with those processes.
For this reason, SAP was primed to take advantage of the burgeoning AM market and launched SAP Distributed Manufacturing to help original equipment manufacturers (OEMs) integrate 3D printing into their supply chains. ENGINEERING.com spoke with SAP Senior Vice President of Digital Assets and IoT, Gil Perez, to understand how the worldwide logistics giant was able to bring AM into mainstream manufacturing.
Preproduction with SAP
With offices in 130 countries, hundreds of thousands of customers in 190 countries and an annual revenue in the tens of billions of dollars, SAP is familiar with the manufacturing market and the manufacturing market is familiar with SAP.
“If you look through all of the manufacturing segments, SAP is probably there in anywhere between 7 to to 8, to 9 out of 10 of the top companies in each of those verticals. We’re also the largest PLM provider,” Perez said.
Not every manufacturer is familiar with 3D printing, however. Before OEMs even begin 3D printing short run goods, they need to ensure that these parts are suited for the 3D printing process. SAP enables these customers to first determine which components make sense to 3D print.
Perez explained, “We would go to one of our customers, like Sealed Air or HP, and we would go with them through the process of determining, out of all of their parts, which are the right ones to be digitized in order to be 3D printable.”
Once an OEM decides to 3D print a given part, SAP’s preproduction tools help that customer to validate the part, ensure that it meets given specifications and even pursue the proper certification, such as FDAapproval, for that part.
“We have SAP Approval and Collaboration, which allows you to start with a 3D model and goes through the whole process of testing, inspection, quality assurance, etc.,” Perez said. “At the end of this process, you really have a manufacturing instruction package for a specific printer with a specific material that you need in order to get a part that will meet your specifications. This manufacturing package is one that the company will be happy to put their logo on and provide their warranty with.”
It’s at this point that the part gets thrown over the wall to production, which sets about getting the part printed. “It then gets moved into the production aspect and it gets integrated natively into SAP’s manufacturing backend so that you not only have a scalable and standard method for going through the approval process and collaborating with 3D printer companies and material companies, but you also have a scalable and robust method for integrating into your supply chain, into your manufacturing backend.”
Read more at ENGINEERING.com