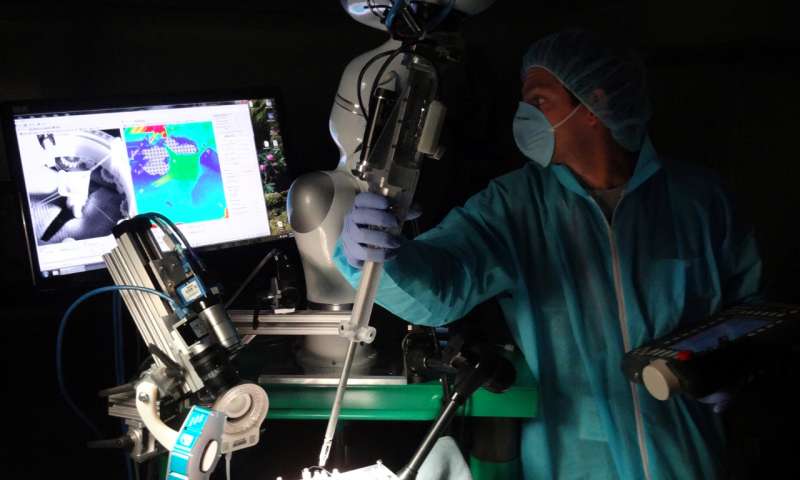
I’m reading a piece describing a 3D tracking system that’s being used for assisting delicate medical procedures and had an idea of how to apply something similar to 3D printing.
The Smart Tissue Autonomous Robot (STAR) is a system to leverage near-infrared light to produce an accurate 3D tracking system for both manual and robotic surgical procedures. As you might imagine, it’s critical to put surgical instruments in the right spots during an operation. This system, developed by researchers at the Washington DC-based Sheikh Zayed Institute, can position tools within 1.61mm.
What I’m imagining is that such a system could track the progress of a 3D print head during a print operation. If the print head varied from the expected tool path by more than a tolerance amount, then the print could theoretically be cancelled as a failed print.
Another way to leverage this tech within 3D printing might be to use it to monitor the position and size of the growing print during its production.
It would be known digitally what the print should look like at each layer of its printing. It might be possible for the STAR system to observe the print and match it against the expectations and again, determine whether something’s amiss during printing.
Yes, there would be all kinds of complexities in these scenarios. Heat from the hot end might confuse the infra-red detectors; complex geometries may hide some portions of the print from the detection system; the system may cost more than the printer itself. And probably a few more.
But I think such a feature might prove very useful in today’s desktop 3D printer equipment, if it could be made feasible. Why? Because too many prints fail.
On the other hand, if desktop 3D printers became a lot more reliable, maybe we wouldn’t need systems like this concept.
Via PhysOrg