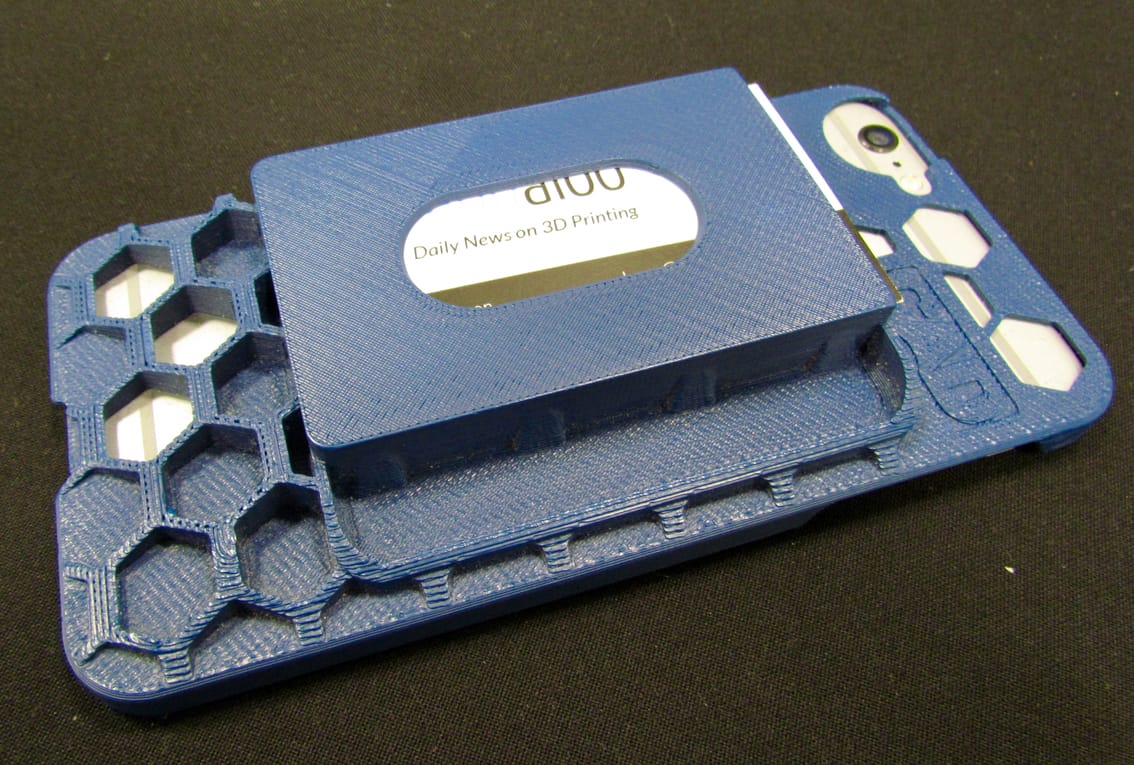
Ok, we did not get an F370 in the mail to test, but we did speak at length with someone who actually runs one. The machine is the largest model in a new line of professional 3D printers just announced by Stratasys.
Jesse Hahne is the President of CAD Product Development (CADPD), a Minnesota-based company that provides design and engineering services for clients producing hardware products. According to CADPD, they specialize in highly unusual projects that other firms might turn down due to the complexity involved.
The company uses earlier Stratasys equipment, including the venerable uPrint, to produce prototypes for their numerous commercial clients. They also have access to a variety of other 3D printers and CNC equipment to produce the required components on any project.
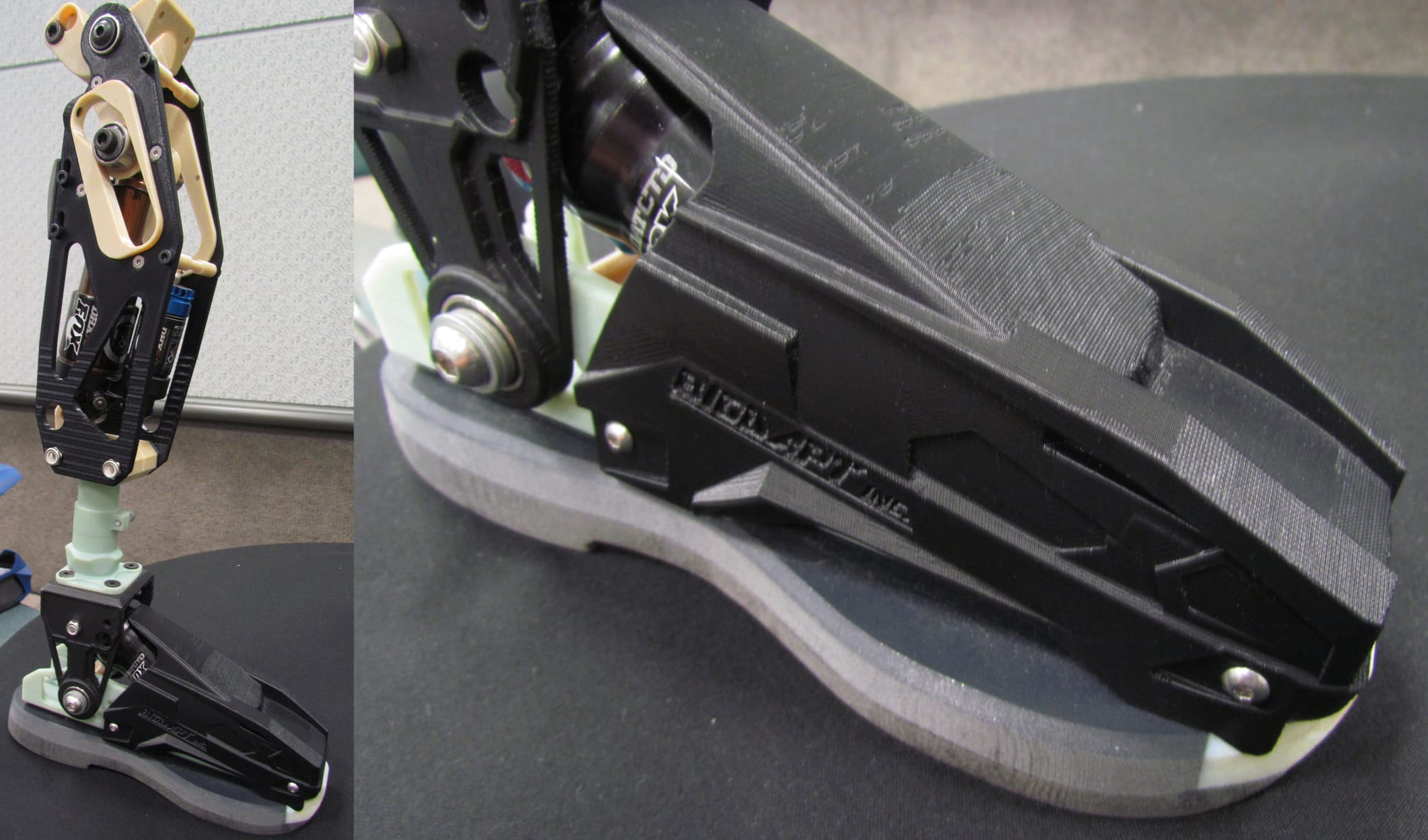
One item they recently produced is this artificial leg, which actually has components made not only on the F370, but also from a Stratasys Connex machine and CNC milled parts. You get the idea of what they produce.
CADPD started secretly testing the Stratasys F370 in September last year, and it appears they gave it a very deep shakedown.
One interesting statement from them is that they had no instructions on how to operate it, yet were able to figure it out easily on the fly. This coincides with Stratasys’ stated goals for this line of 3D printing equipment, as they’re hoping to gain entirely new clients who were previously uncomfortable using the equipment.
Technically, CADPD saw a number of operational improvements when using the F370, not the least of which was the far larger build volume over their uPrint. The uPrint’s build volume is 203 x 203 x 203mm, but the F370 is a much more massive 356 x 254 x 356mm.
But while you might think such improvements are minor in nature, they actually do have a significant effect on a workshop using 3D printers continuously. How? It’s the labor effect.
By reducing the amount of labor required to operate the machine, some interesting effects occur. In the case of CADPD, their clients were only offered prints in a single color, which was constantly loaded on their prior equipment. They did not offer a choice of colors because the prior Stratasys gear took a relatively long time to swap filament spools. When I say long, I mean like 20 minutes. And do that twice to get back to the original color. That’s around 40 minutes your equipment is NOT 3D printing. Do that a few times in a day and you’re essentially reducing the efficiency of your expensive equipment.
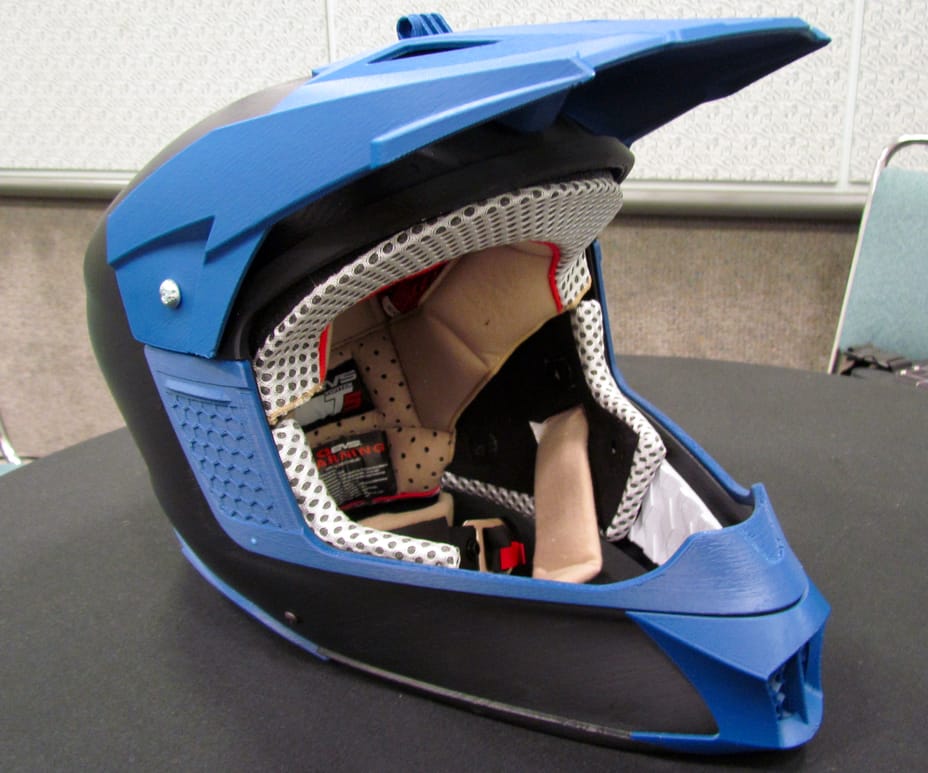
Now CADPD can offer multiple colors, because the labor required to change spools is negligible. And it’s been well received by their clients. This machine literally enabled a new product for the company.
The increased print volume is also a big time saver, as the company no longer has to chop up 3D models into smaller components and assemble them after printing. That saves time modeling, printing, post-processing and assembly. Labor is for many workshops, the most significant cost component of the end product.
The F123 series has larger material capacity in two ways. First, rather than the skimpy 30 cubic inch filament uPrint cartridges, the F123 series uses 60 and 90 cubic inch filament spools. Even better, some of the models can also include four materials bays, typically used for both support and model materials. But the F123 series is sufficiently intelligent to automatically swap to the second spool once the first one is emptied.
This, combined with the larger spools, means the machines can run far longer than prior Stratasys equipment. And that means a workshop spends less time swapping material spools, again reducing labor.
While the F370 model is able to use Insight, Stratasys’ advanced slicing tool, it turns out that most prints use GrabCAD, the default easy-to-use slicer. Hahne explained they used Insight once for a prototype vacuum tool where they had to more precisely control the porosity of a surface.
Is the machine truly reliable? Hahne explained that they’ve used the machine basically continuously for the past five months without incident. Well, that’s not entirely true. Hahne said they had two print failures. One was apparently due to over-using a print plate beyond the recommended usage levels, by printing many copies of the same item on the same spot on the plate over and over. The other was caused by a technician incorrectly adjusting the maximum overhang angle.
I think those are reasonable failures to have. That’s critically important to a company that derives their revenue from the operation of equipment such as this.
This level of reliability and efficiency is what Stratasys is looking for: it provides a level of confidence for customers and prospects that might not be found in many other machine options, even those that might be initially seen as less expensive. Companies know that the true cost is not just the machine or its materials itself, but all the costs and commitment to long term operation that might occur during the machine’s operational lifetime.
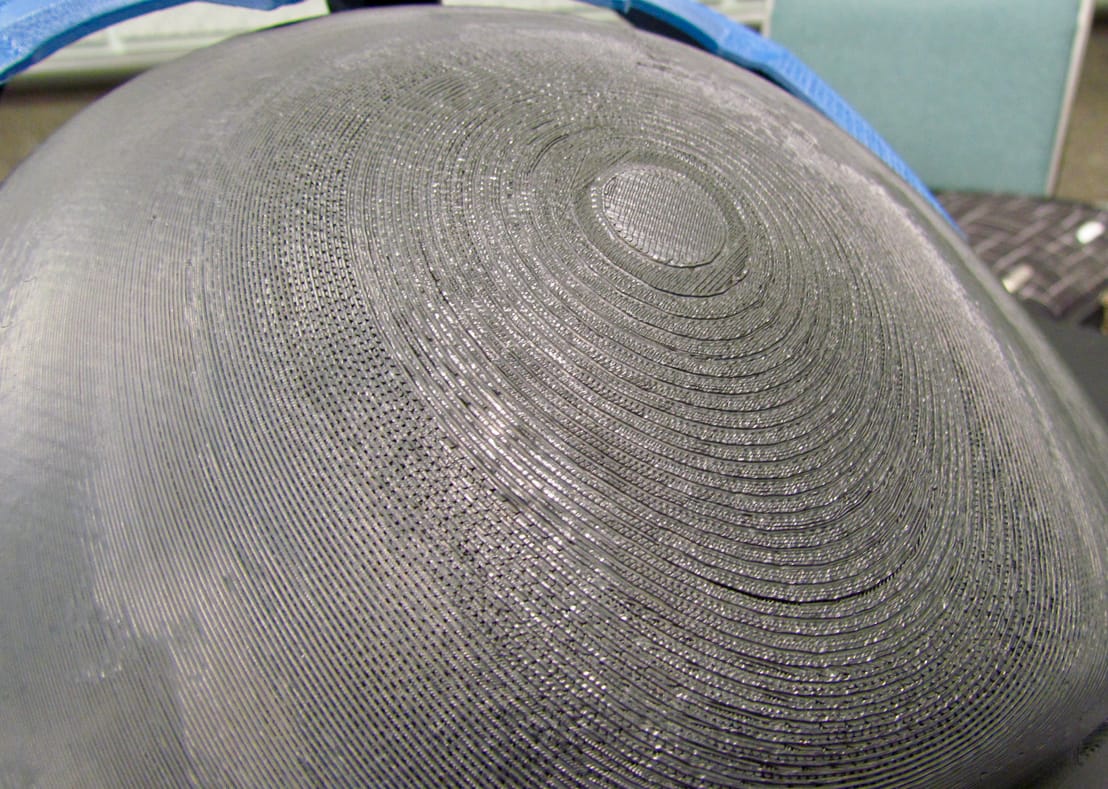
When asked how well the PLA prints work, given that the nature of the F123 series does not permit the use of soluble support, Hahne had no issues. He said the breakaway supports were well designed and had a very minimal touch on the model, leading to almost instant separation after the print completes.
Hahne also reports that the machine is extremely quiet, although I’m still not sure you’d want to have it in your office.
Asked about the pricing of the equipment, Hahne explained that while the price may be higher than some other competitive machines, his business was easily able to pay off the cost of the machine in a few months due to the efficiencies provided. Things like “drag and drop” from Solidworks do add up over time and reduce labor costs.
The F123 series offers a variety of materials, and I asked Hahne about them. He explained that he liked the low cost of PLA, the deep reds, bright oranges of ABS, but overall preferred using the new ASA material for its good engineering characteristics and color selection. He did add that they found PC-ABS to be the best of the materials for printing thin-wall structures.
So it seems there is at least one very happy customer using the F370; there’s likely going to be many more.
Via CADPD