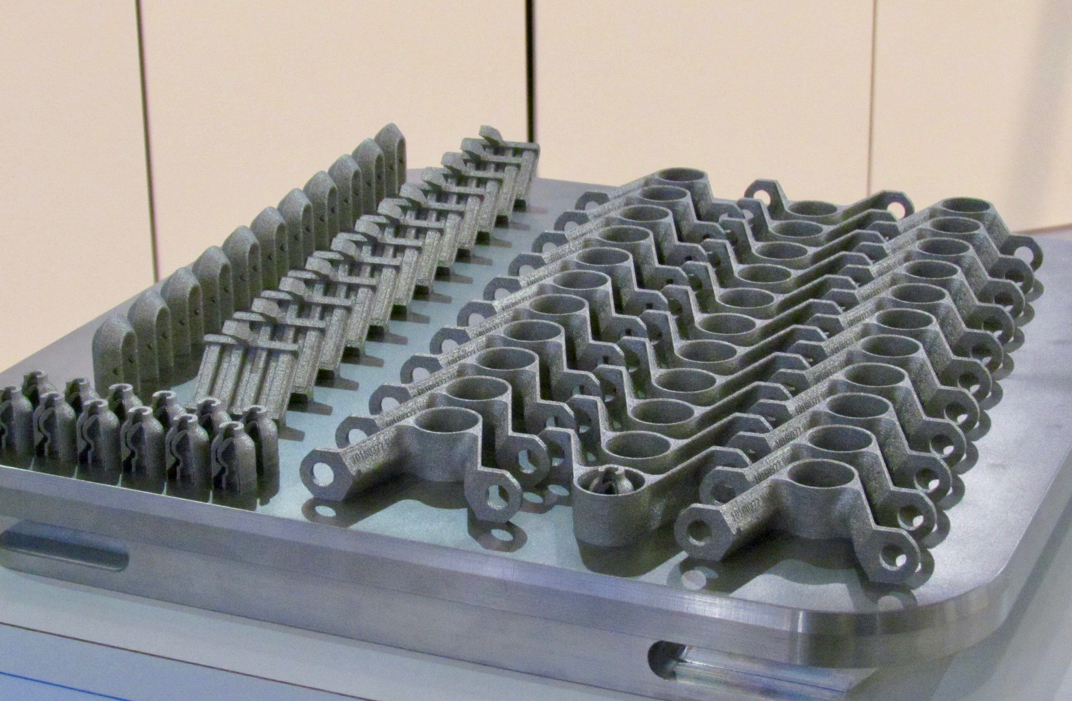
A report from the University of Nottingham proposes ways to make automobiles more fuel efficient through the application of 3D metal printing.
The “Functional Lattices for Automotive Components” project hopes to achieve “significant weight reductions” and “lower the number of separate components” in automotive design.
The approach the project appears to be using is to swap out conventional parts with 3D printed equivalents that have been lightened through lattices. The “skeletal” new parts would be functionally just as strong as the originals, since the lattice would be specifically engineered to provide strength along the expected lines of mechanical stress.
The other approach used is to reduce the number of parts. This is done by redesigning some complex components that would otherwise be an assembly of smaller parts. In conventional manufacturing, making processes have constraints that limit the complexity of the object, frequently requiring multiple parts made to meet a functional need.
These restrictions are not present when 3D printing, and so a new part meeting the function can be designed that doesn’t need to be broken down into sub-components for assembly. While this approach certainly simplifies things, it also reduces weight because there is far less need to include bolts and other attachment hardware to keep the sub-components together.
So I am entirely convinced this project can succeed, technologically. Shapes can be designed to dramatically reduce the weight of the parts. The project is suggesting reductions of 40-80% on many components, particularly the heaviest items in the automobile.
I am entirely not convinced this project can succeed, financially.
At the present time, 3D printed metal objects are horrifically expensive. Let me put this in perspective: titanium powder for 3D metal printing can be acquired for as little as USD$500 per kg.
There are a lot of kg’s in a car, even if you reduce the weight by 40-80%. Do the arithmetic.
The technology of 3D metal printing has become functionally appropriate for application in industry – but it has yet to become financially feasible except for certain industries where high parts costs already exist. Does that include automobiles? I don’t think so, at least not yet.
No, the real innovation required here is to somehow reduce the cost of 3D metal printing. And that’s happening now in several projects I’m aware of.