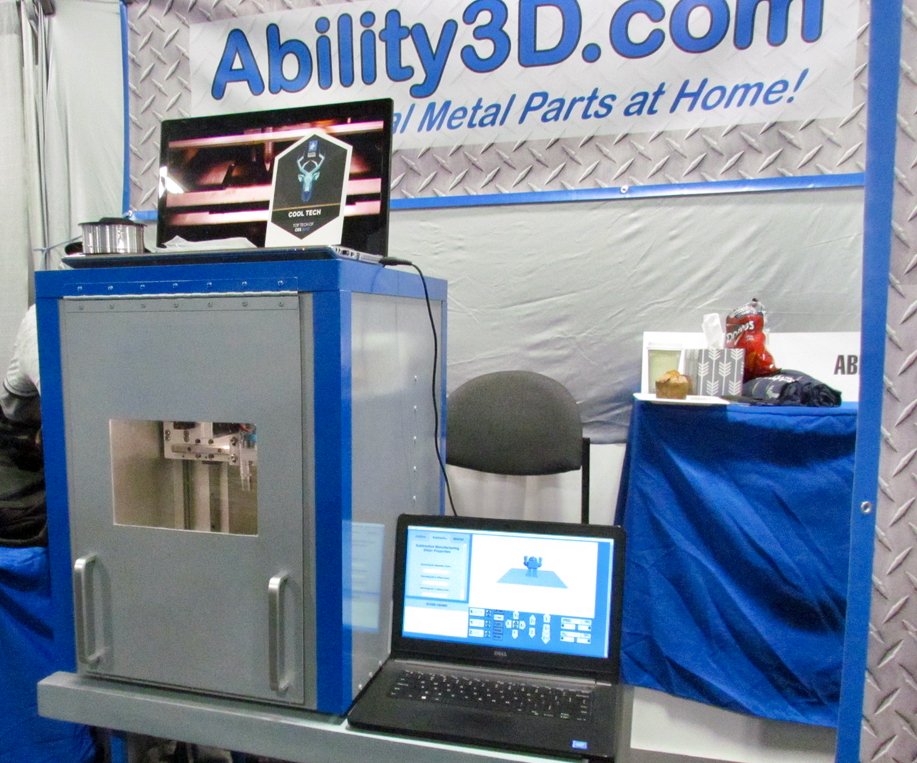
We had a chance to talk to Ben Willard, the “guy in the garage” behind Ability 3D, a 3D metal printer.
In the past few years I’ve seen a number of different strategies for 3D printing in metal, but none are like that used by Ability 3D.
The driving force behind Ability 3D is one Ben Willard of Florida. The engineer, who formerly worked at NASA for several years, has been a fan of 3D printing since 1998. Since then he built several 3D printers of his own design, but was always intrigued by the idea of 3D printing in metal.
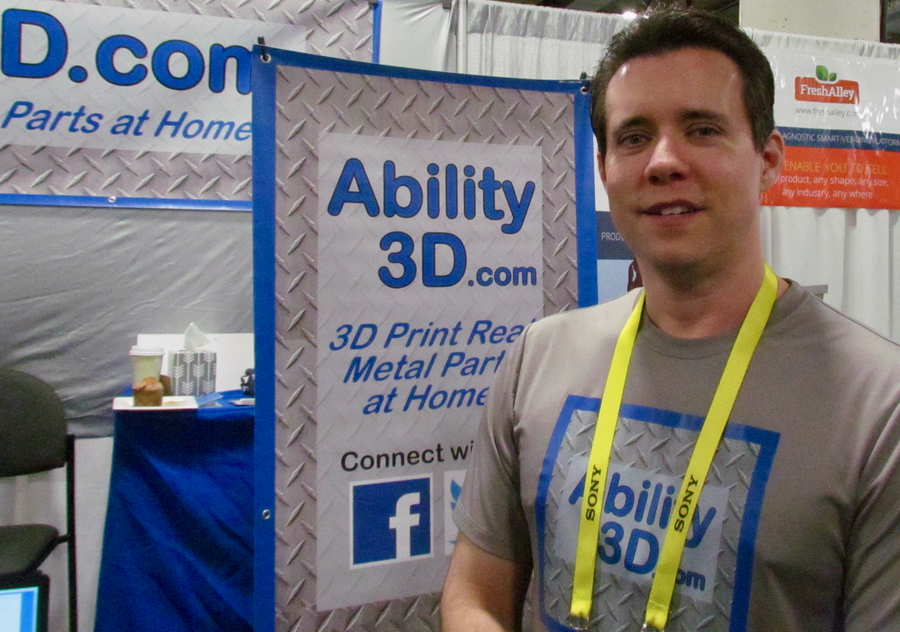
However, 3D metal printers of the day were – and are – typically very expensive to purchase and operate. They are far out the price range of hobbyists, startups and smaller companies, the market Willard wishes to address.
The known 3D printing processes were obviously out of the question, so Willard turned to a more familiar metal process: MIG welding.
In this process, an electric arc forms between a consumable metal rod and the build target, where the consumable material is heated sufficiently to join the target.
The idea of the Ability 3D machine is to “CNC” this process. Essentially the machine is a MIG welder in a CNC package. The print head moves the MIG apparatus around in a controlled manner to gradually build up a solid, metal object. A standard MIG welding wire is used in the process.
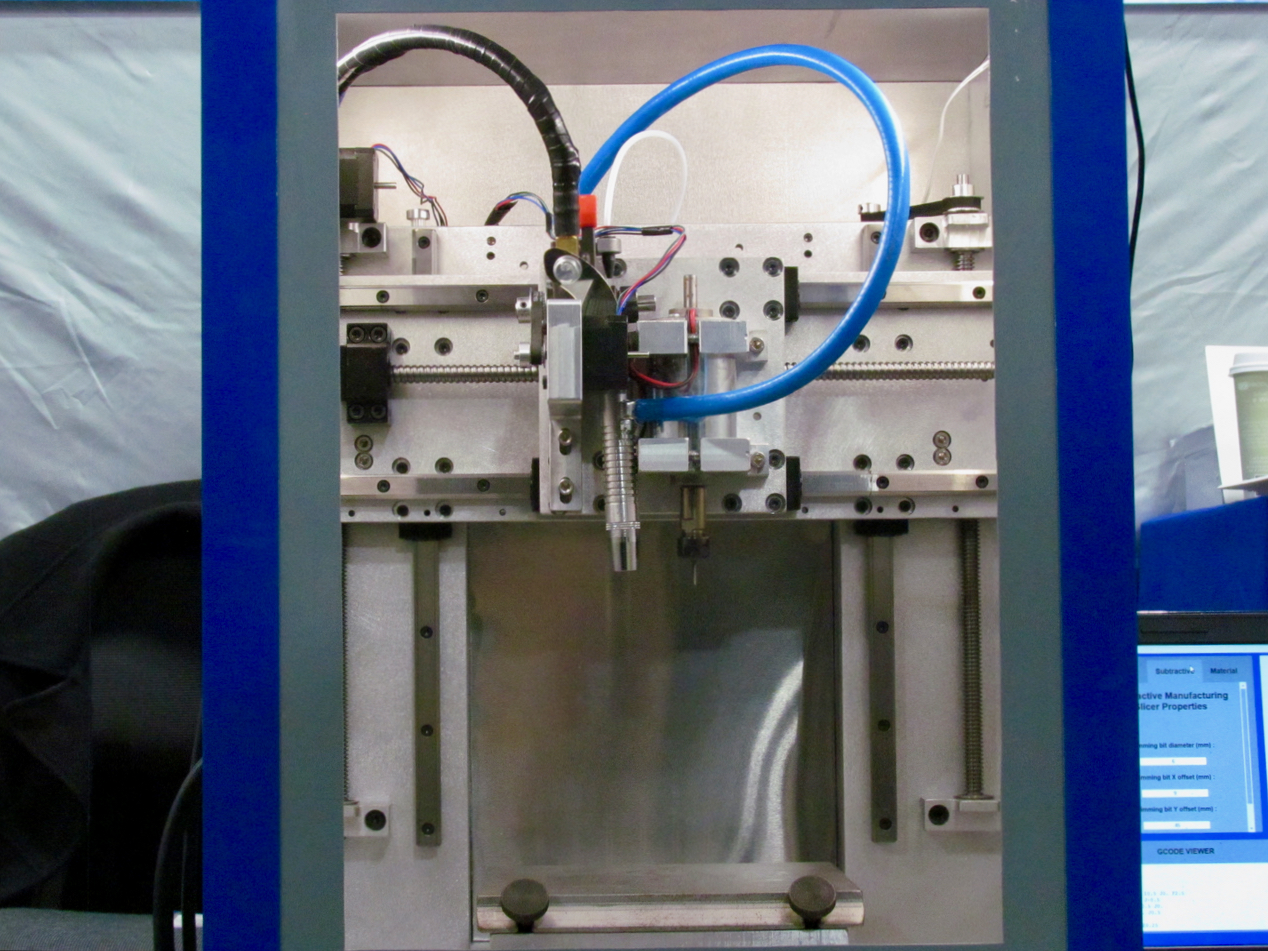
As you might imagine, the deposition would tend to leave rather coarse and irregular metal shapes as it proceeds. This would certainly cause issues when depositing subsequent layers as the surface would be not flat. To counteract this effect, Ability 3D includes a CNC “trimming bit” to shave off the brim of the layer’s deposition, as well as flattening the top of the most recently deposited metal surface. The size of the trimming bit determines the minimum feature size for prints coming off this machine.
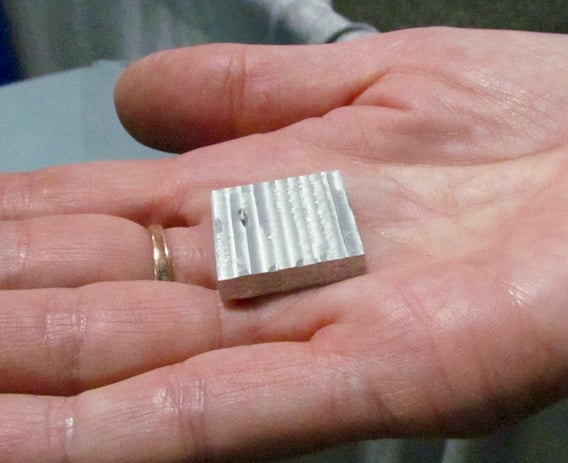
There are some very interesting advantages to this process.
First, the MIG process is very well understood. It is capable of depositing very strong, solid metal material that is used for industrial purposes across the world for decades.
Secondly, MIG material is available everywhere and in a wide variety of standard metal mixtures. And it’s not terribly expensive.
I asked how the print adheres to the print surface, as this is a big issue for some existing 3D metal printers: an expensive “hot wire” EDM machine is often required to slice the print off a metal plate after printing.
It turns out Ability 3D uses an entirely different process for bed adhesion. The idea is to use dissimilar metals when printing: the base is a different metal than the print material. Willard explained that a thin, but strong molecular bond is formed between the two during printing. However, this bond is quite brittle. Thus, removing the print is as simple as knocking it with a hammer afterwards. This is vastly simpler than methods used on more expensive machines.
Installation of the machine is similarly less expensive than industrial machines; you need less environmental setup than you would for a MIG welding arrangement. You’ll need a standard 15A outlet and a dryer hose-like vent for fumes. The rest is all self contained within the printer’s cabinet.
It remains to be seen how strong and reliable the parts printed in this process can be, but Willard explained that independent testing is actually underway at this time.
Pricing of this machine is an interesting tale. Willard expects the price to be a mere USD$3,000, far, far less than the six or seven-figure setups you’ll need for industrial metal printing equipment. His desire is to enable access to 3D metal printing capabilities for as many people as possible, and will hold at this price level, in spite of investors and speculators that propose he raise the price to at least six figures.
Regardless, the intention is to launch the product on Kickstarter this March, and that’s not very far away.
Via Ability 3D