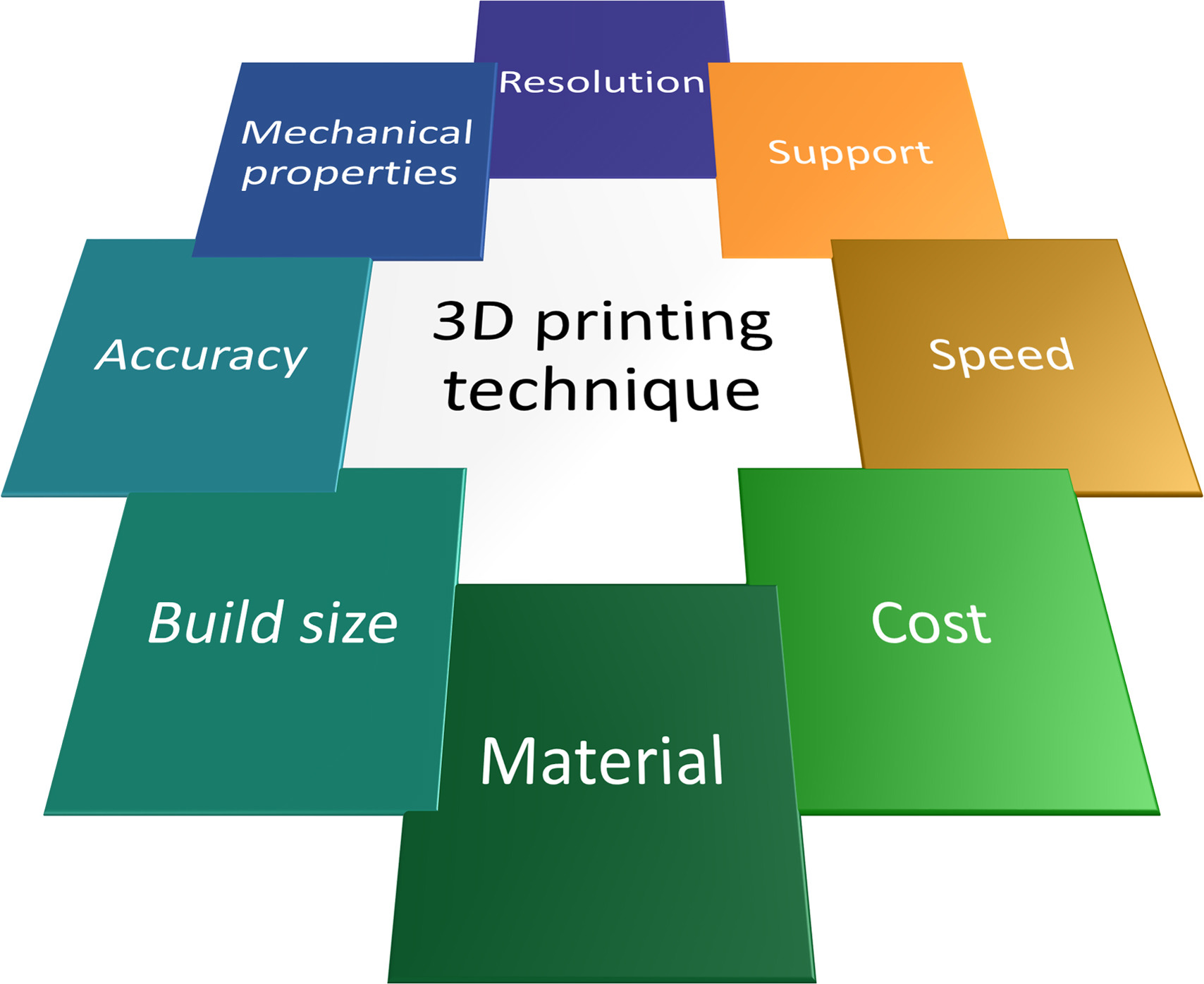
There’s some interesting research on the ability of 3D printing technologies and their ability to produce unusual membranes.
Membranes are essentially specialized filters whose shape permits or allows particles of particular sizes to pass through. They’re used in a wide variety of industrial applications, but currently have a number of manufacturing constraints.
Sounds familiar? I thought so too. The proposition is whether 3D printing technologies could be used to produce unusual or better membranes. A study in this regard was undertaken by the Centre for Advanced Separations Engineering and Department of Chemical Engineering, University of Bath, and the School of Chemical Engineering and Advanced Materials, Newcastle University, both in the UK.
While some industries, particularly aerospace, have leveraged 3D printing technologies to produce unusual parts that could not have been manufactured in other ways, could the same effect be true for membranes?
Membranes are a bit different than an aircraft or rocket part in that they require extremely fine details. But if you could 3D print microscopic shapes, then it is theoretically possible to design membranes that could operate in vastly different and more complex ways than current approaches.
Perhaps you could design a complex membrane shape that would capture certain types of particles based on their geometry. Or you could design a shape that would be easily cleaned. Or both. Perhaps a multi-layer membrane could perform seemingly magical acts of filtration by combining several steps of a process.
Toxic materials might be purified, liquids cleansed, materials separated in ways not yet imagined.
It sounds great, but could this be done with current 3D printing technologies? The study identified these characteristics as requirements to 3D print such styles of membranes:
- Resolution: High resolution needed – in nanometer range resolution
- Accuracy: Need to be able to print the membrane as designed, inclusive of the effect of pre-treatment and post-treatment steps (e.g. removal of support material)
- Build size: Need to be able to print actual membrane sizes (e.g. >1 m in width)
- Speed: Generally as fast as possible to minimise build time
- Printed materials: Extension of compatible 3D printable materials to include the common materials used for membranes
- Mechanical properties: Materials which are able to resist high pressure processes (1– 40 bar) and a range of different solutes and solvents
- Support: Smooth (low roughness) and strong support that can be easily removed or AM system that does not need support
- Cost: Competitive and comparable to phase inversion membrane fabrication.
One requirement I disagree with is the size. If you require a membrane with more than 1 meter in width, you could also assemble a series of smaller membranes together in an array to accomplish the same feat, although at greater cost.
The study surveyed literally all major 3D printing processes, equipment and materials to determine whether this is possible today. Their conclusion:
We have illustrated that current AM techniques are not cost-effective for membrane fabrication and are projected to remain non-competitive to conventional membrane fabrication techniques due to the requirement of complex printing technologies and materials in the short/medium term. However, future AM techniques may be targeted for niche membrane markets whereby specific membrane design requirements are needed. Current printing technology is able to print dense membranes as well as porous one with resolutions from ~100 nm, thus are unsuitable for ultrafiltration and nanofiltration.
That’s what I would have expected to see: too expensive and insufficient detail. But that could certainly change in the future. Please take a look at this interesting and very detailed analysis.
Via Science Direct