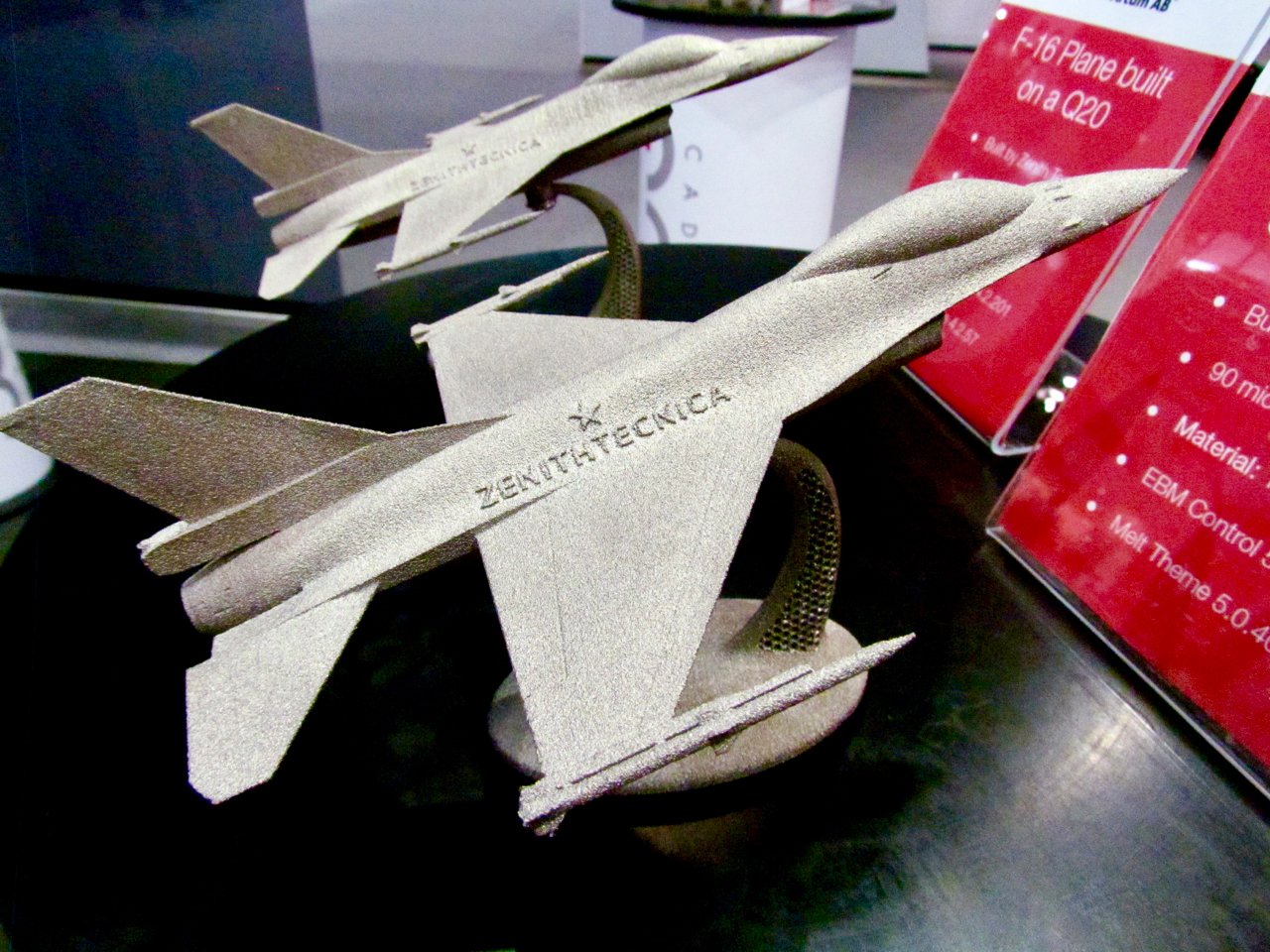
Those familiar with polymer 3D printing will recall the challenges of successful printing, but that’s nothing compared to the requirements of 3D metal printing.
We will continue to see a lot of experimentation in 3D metal printing in coming years, as it requires far more investigation than that of its polymer equivalent processes.
Why? In a sentences, it’s because metal prints are most likely to be used as production parts rather than prototypes or artwork.
Once you shift the purpose to production, a number of important things happen.
Whereas if producing a prototype or artwork, the primary goal might be to ensure the simple shape was achieved, there’s a lot more to do when producing a production part.
Production parts are by definition used for some specific purpose. Someone will pay money for that part – or the contraption it’s part of – to perform a useful function. The buyer expects the part to perform properly when delivering that function.
But what does “deliver properly” actually mean? It means that the part will meet a possibly long list of engineering requirements. It must provide the appropriate strength in expected conditions.
And it must be guaranteed to do, for every copy produced.
That means the print must not only be able to meet the specifications, but EVERY part must do so as well. And they must do so for the expected lifetime of actual use, which could be many years. That requires a very good understanding of the physical nature of the part as it is produced within a 3D metal printer.
This is why time must be spent tuning the 3D metal printer parameters to ensure the appropriate micro crystalline structure is reliably formed during printing operations.
But there’s more.
Often printed metal parts must have an audit trail. Consider the case of an aircraft part. Should there be a problem with the part, it must have a completely transparent history of its production so that any errors detected can be rapidly corrected.
This means that the specific machine producing the part must be known, as well as the specific printing parameters used. The specific material used – which must have a very consistent chemical mix – must also be known. There’s a great deal of information to be tracked for some types of 3D metal printed parts.
If this sounds expensive, it is. But that’s actually ok for certain industries where there is already the expectation of expensive parts, such as aerospace and to a lesser extent automotive.
I should say that while I’ve listed the effects on metal 3D printing of a shift to production, much of the same effects would be occurring when polymer 3D printing moves to a production state as well. a
It’s a lot more than just getting a print done; you must absolutely know exactly what that part will do once it’s produced.