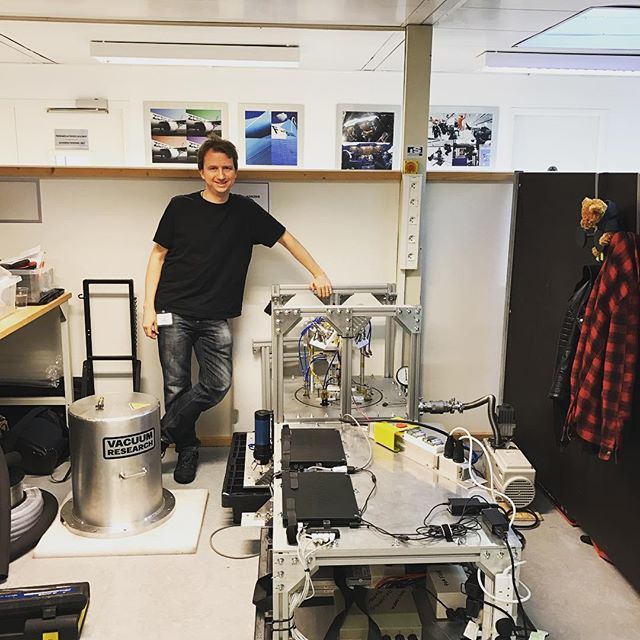
Made In Space changed the world when it installed the Zero-G Printer on the International Space Station (ISS) in late 2014.
It changed the world once again when its second generation machine, the Additive Manufacturing Facility, was put aboard the ISS earlier this year to become the first commercial 3D printer in space.
As exciting as printing plastic in space may be, humanity’s ability to manufacture objects in space will only begin to truly take shape when we can 3D print metal objects. For this reason, Luke Carter, of the Advanced Materials and Processing Laboratory (AMP Lab) at the University of Birmingham, has made it his mission to 3D print metal in microgravity.
While Carter and his team at AMP Lab have yet to send a metal 3D printer into space, they are making significant headway and have recently demonstrated the ability to 3D print metal in microgravity aboard three separate parabolic flights. ENGINEERING.com spoke with Carter to learn more.
Zero-G Metal 3D Printing Ain’t Easy
Due to the fact that Carter and his team are in the process of seeking patents and funding for subsequent research, the University of Birmingham Postdoctoral Researcher was reluctant to give up too many details about the project. What he did reveal, however, provided a glimpse into the difficult nature of 3D printing without the help of gravity.
Working closely in collaboration with the European Space Agency (ESA), Carter and his fellow researchers have developed a demonstrator device capable of printing aluminum in microgravity. While metal 3D printing often evokes images of powder bed processes, like selective laser melting, Carter explained that powder wouldn’t do in an environment like the ISS, as it would be difficult to keep the powder in place. Instead, the Birmingham machine more closely resembles the metal 3D printing process of directed energy deposition (DED), and uses an aluminum wire as feedstock.
Ensuring that the material stays in place without gravity is a unique problem to solve. “One of the challenges with 3D printing in microgravity is keeping the material where you put it,” Carter said. “It sounds odd, but if you put an object on a table on Earth, it stays there. But when you’re floating around, as I’ve learned on the parabolic flights, things don’t necessarily stay where you put them. More importantly, small forces can just send things off in strange directions.”
Without giving away too much detail about the mechanisms involved, Carter explained how the technology managed to keep the printed object in place. “We’re not relying on gravity for things to drop into position. We’re essentially using the surface tension of the molten material to feed our wire into and keep it in place,” Carter said. “We’ve also developed some different ways of keeping the material attached to the substrate. I can’t say too much about that and why we have to worry about that, but it’s certainly of interest.”
Like a DED machine, such as the plasma arc system developed by Norsk Titanium, the Birmingham device creates a near net shape part. The printed object would necessarily have to be machined to its final dimensions. “The process itself is inherently a near net shape process. It is not ever going to produce the geometric accuracy that you see coming out of a high-end [powder bed] 3D printer. It’s just not that kind of process. Being wire feed, its resolution is limited in that way.”
For this reason, Carter envisions the use of a CNC-type machine on the ISS at some point in the future to ensure that printed metal parts can be properly finished. This would be essential for “mating” pieces, in which two parts need to fit snugly together, as well as removing support structures, though Carter believes it’s possible to print support structures with built-in weak points to easily snap them off.
Another issue his team had to consider was the power requirements of the ISS. For the project, it was necessary to ensure that the printer used less than 1500 watts of power. Carter’s team managed to keep it below 1300. “What we developed is quite efficient in terms of getting the energy where we need it. It runs at about 1300 watts, which is a little bit less than your standard electric kitchen kettle.”
Read more at ENGINEERING.com