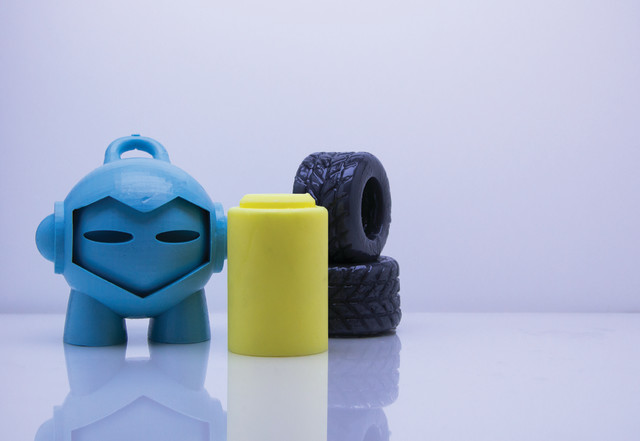
When I last spoke to Graham Bredemeyer over a year ago, he told me that he was developing a unique 3D printer platform in his own apartment in Chattanooga, Tennessee.
Since that time, the technology has evolved into a startup called Collider, complete with an R&D lab and an advanced 3D printer dubbed the Orchid.
Unveiled at Inside 3D Printing San Diego, the Orchid may hold as much or more promise for 3D printing as Carbon’s M1 3D printer and continuous digital light processing (DLP). The system is capable of combining the dual strengths of reaction injection molding and continuous DLP 3D printing to produce geometrically complex parts from a potentially vast array of materials available to the reaction injection molding industry.
In conjunction with the big unveiling, I spoke with Bredemeyer, who is both CEO and founder of Collider, to learn exactly how the technology works and what Collider plans for the future.
Programmable Tooling
The Programmable Tooling process relies on printing an a sacrificial mold with continuous DLP before filling the print with thermoset resin. (Image courtesy of Collider.)
The Orchid implements a hybrid 3D printing technique that Collider refers to as “Programmable Tooling.” The process begins with continuous DLP 3D printing, the projection of near-UV light at a vat of resin to produce layerless parts at very fast speeds. Similar technology can be seen at companies like Carbon and 3D Systems; however, Collider has introduced a second step in the process that changes the 3D printing ballgame altogether.
Unlike other continuous DLP platforms that 3D print solid objects, the Orchid 3D prints molds with extremely thin-walled shells. Once the mold is complete, the print bed is raised and, through a hole in the bed, reaction injection molding plastic from a two-component resin meter mixing system flows into the hollow shell, filling it with thermoset resin which hardens into a solid object. At the same time, through a second hole, an air control system ensures that there are no air pockets or deformations during the reaction injection molding process.
All of this takes place within the machine itself, meaning that there is no manual intervention along the way. It is only after this second step that the object is manually removed and rinsed with hot water to remove the outer shell. The result is a fully dense plastic part.
3D Printing with Thousands of Variations of Materials
The advantages of Programming Tooling could be a thousand-fold, in that by introducing traditional reaction injection molding plastic to the 3D printing process, the Orchid can potentially use many of the thousands of variations of existing 2K thermoset materials already on the market. Bredemeyer argued that this tackles an issue that manufacturers face in relation to the high cost of tooling for small batch parts.
“[3D printer manufacturers] talk about the materials that they’re developing,” Bredemeyer said. “But when I’ve been talking to manufacturers for last five years, I haven’t ever heard them complain about mass manufacturing materials. I do, however, hear them all complain about tooling. That’s a problem that we’re really solving fundamentally. Tooling for low volumes of parts is an extremely big issue for manufacturing. The materials are not.”
Therefore, rather than attempt to develop materials in-house, Collider invented Programmable Tooling as a means of getting at the root of the problem by making a system that can perform batch production using the wide range of existing materials.
“It’s not that we’re making new materials. It’s that we’re enabling thousands of different material variations through the development of a new machine,” Bredemeyer added. “The difference is in the materials, not because the materials are new, but because the materials are good and they’re proven and they’ve been mass produced for decades.”
A manufacturer could potentially save a tremendous amount of time and money with a rapid production technique such as Programmable Tooling. Collider estimates that the time and tooling required to make a run of 10 tail lights would take 11 days and cost $259.40 per unit, due to economies of scale related to tooling. Using the Orchid, the firm estimated that it would only cost about $5.44 per unit and take two hours.
Read more at ENGINEERING.com