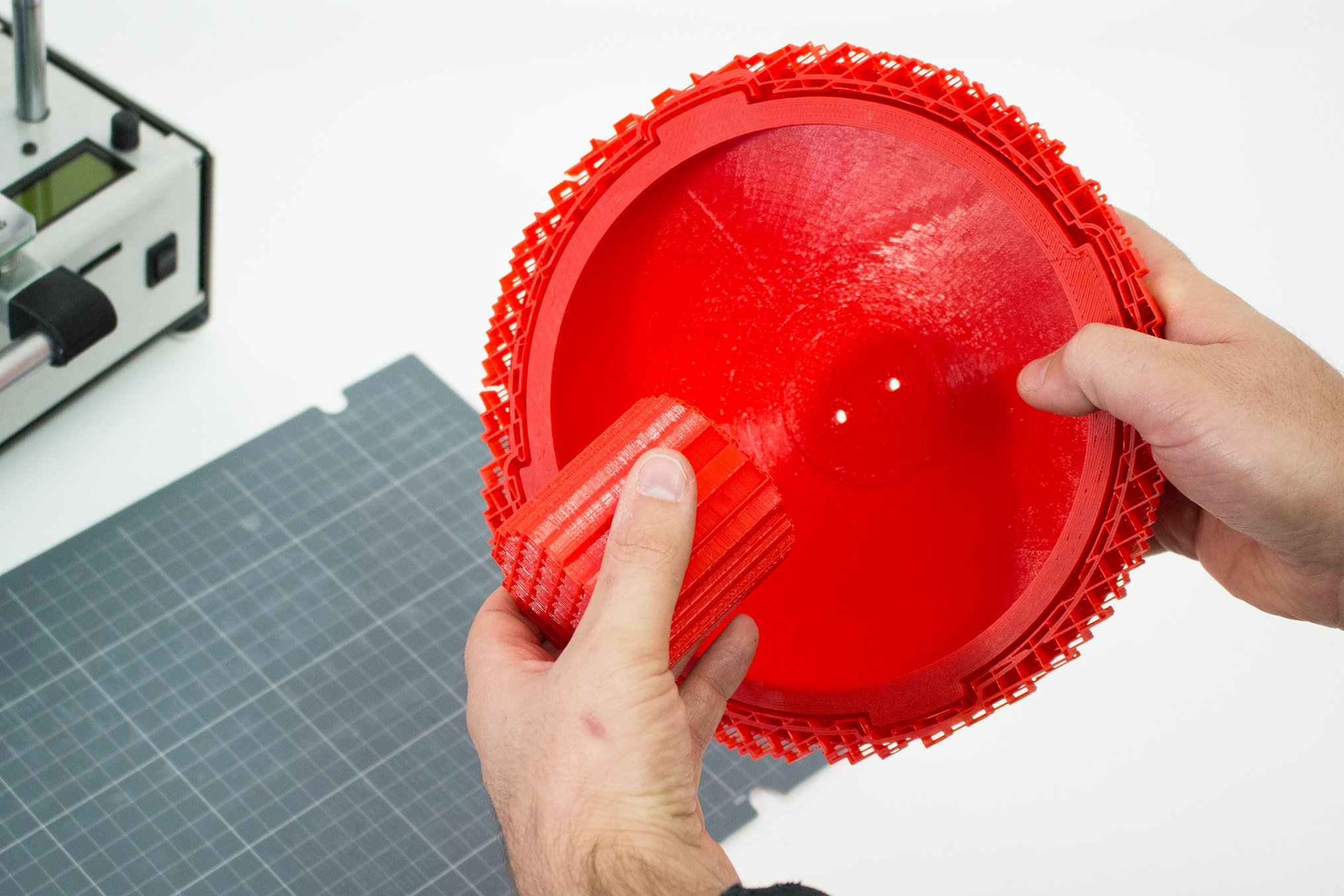
We had the opportunity to discuss business with MAKEiT’s Salomo Murtonen.
MAKEiT is based in Alhambra, California and makes inexpensive but powerful desktop 3D printers. We first encountered them at a trade show in 2015, and have written stories on their progress several times, including their most recent launch of the Pro-L model.
Fabbaloo: MAKEiT is only two years old; how did it get started? How much have you grown in those years?
Salomo Murtonen: Our company was first registered in summer 2012. As an operational business, it has been a little over 2 years old. Started with two people in a living room and garage, we have now grown to a team of 5; from zero product to 3 printer models, and couple more in the pipeline… from zero paid customer to a solid base of repeating customers. We are building a local network of strong resellers, while progressing with advanced R&D projects with Caltech, auto maker and designer, etc.
Fabbaloo: Unlike many desktop 3D printer manufacturers who initially focused on the consumer market, MAKEiT has been focused on the professional market from the beginning. Did you know something others did not know?
Salomo Murtonen: It arose from both our personal takes on 3D printing and somewhat out of necessity. Coming from engineering and design backgrounds we’ve long been familiar with not just 3D printing, but the idea of distributed and additive manufacturing has been talked about in that circle for years. We ourselves wanted to have the ability to design and manufacture our own products at a much smaller scale and it was clear to us that the printers on the market at the time fell significantly short of the needs for real manufacturing.
Industrial and professionally focused users value things differently than hobbyists, experimenters, and DIYers. Before we even started selling we spent about a year going to shows, expos, Maker Faires, etc, and got a lot of valuable feedback on the printer and our position in the market.
It was very common for a hobby user to tell us proudly how their machine can do almost everything ours can, only to then elaborate on the hundreds of hours it took to get there, and the hours every week it took to keep it running. Meanwhile the professional segment users immediately valued what we had to offer, and we frequently heard things like “this is the first printer that looks like a real tool, not a toy”, which echos to our original vision of “making a value-add tool” to solve existing problem, ie, how to lower the initial costs of producing a physical product while increase “to market” speed.
Fabbaloo: You offer two models, the PRO-M and the PRO-L. What’s the difference between them?
Salomo Murtonen: The most basic difference is size. The Pro-M has a build volume of 8x9x8 inches, the Pro-L comes in at 10x12x13 inches. The Pro-L also has included a few more future-proofing features as we intend to offer upgrades in the future; things like extra ports for future add-ons. Both of our machines come with dual extrusion, and the Pro-M can be optioned up a bit to include things that come standard on the Pro-L, like the taller 13-inch height and the wall-mount compatible side panels. There are also some differences in what’s included in the package; we’re trying to keep the Pro-M base price very accessible, while the Pro-L is really an all-inclusive top level package.
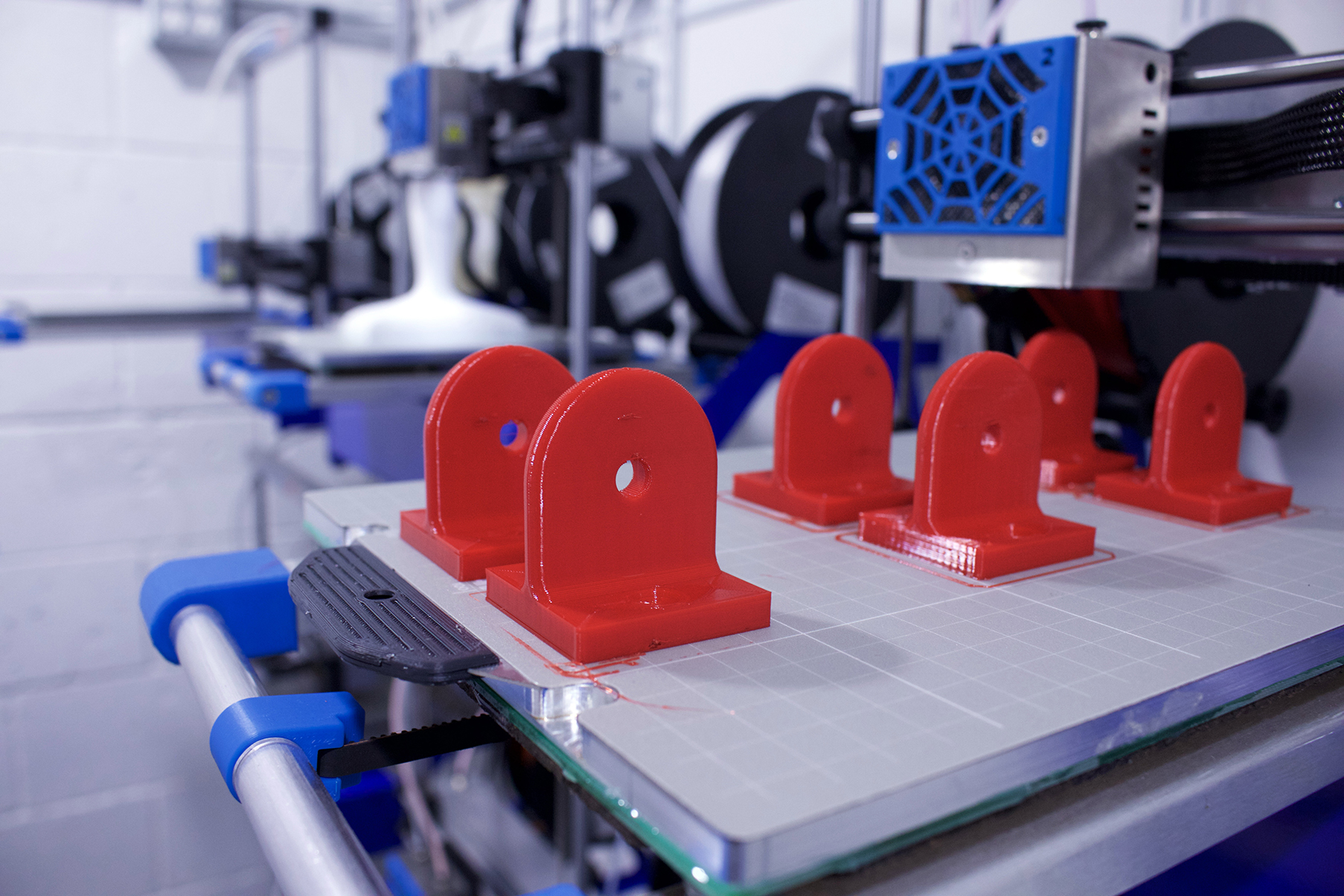
Fabbaloo: When I saw the machine last year I was impressed with its ability to 3D print copies of items. Can you describe how that works, technicallY?
Salomo Murtonen: It’s actually a pretty simple system. Our print head has two nozzles spaced 50mm apart, and since they’re on the same head they move together always. The duplication is a simple on/off toggle from the printer’s menu, or can be set with gcode while slicing, and it turns the second nozzle on as a blind copy. The second nozzle will print whatever the first nozzle prints, only 50mm offset to the right. There is of course the limitation that this won’t work with parts that don’t fit under that 50mm dimension in width, but it’s still applicable for tall parts or long parts. It’s proven to be a very valuable feature for many of our customers who run batch part production on a daily basis.
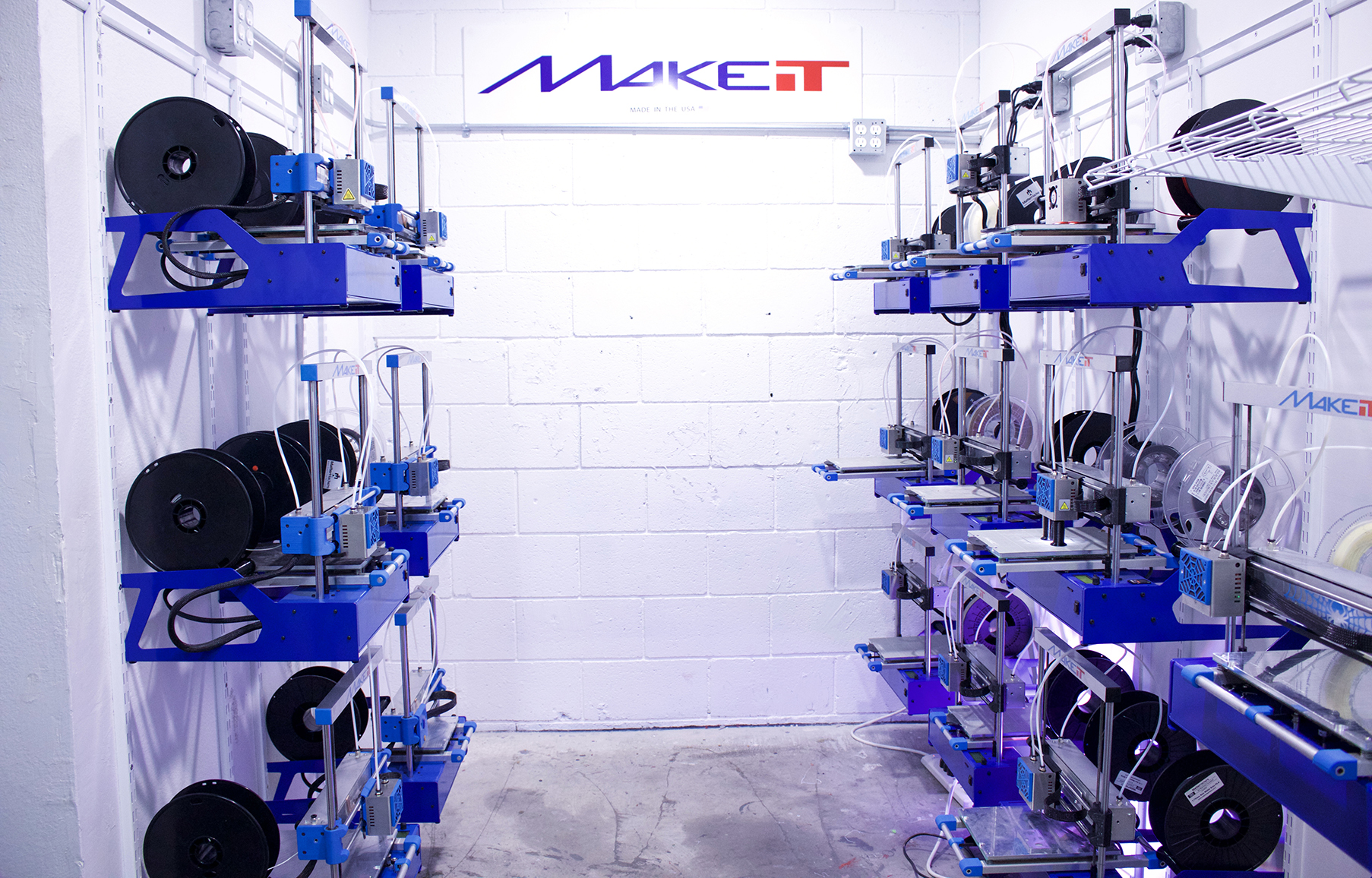
Fabbaloo: With the tremendous amount of competition in the desktop 3D printing sector, does MAKEiT offer a notable feature to differentiate from others?
Salomo Murtonen: In order for small businesses with limited shop space to scale up the batch production capacity, we have launched the original wall-mount printer system after using this system in our own shop. It is a fast, simple and cost effective system to set up a vertical production line on a shop wall in couple hours. In our shop there are 9 printers installed on 6 shelf tracks. These tracks are stock items available in hardware stores. We custom made track-ready side panels to be added to regular MAKEiT Pro desktop. This addition won’t cost customer a penny. Besides printers cost, the extra cost of this production line is the shelf tracks, which is under $150 in our case. Now all plastic parts on MAKEiT Pro printers are produced in house, with this production line utilizing “Duplication” mode. Groups of printers are assigned to produce certain parts using size-specific nozzles and filaments so that production efficiency is enhanced. As for managing production line maintenance, our system has its advantage as well. If one printer is messed up requiring service, we just fix that particular printer, while other 8 printers are still on, functioning individually, unlike the traditional practice, shutting down the whole line in order to conduct maintenance service.
To minimize down time, we offer an unique solution to our clients: “down time coverage”. It is included in our one year product warranty. While their printer is in service with us during the warranty time, we will print for their digital production at material cost. This way our customer won’t lose any printing time.
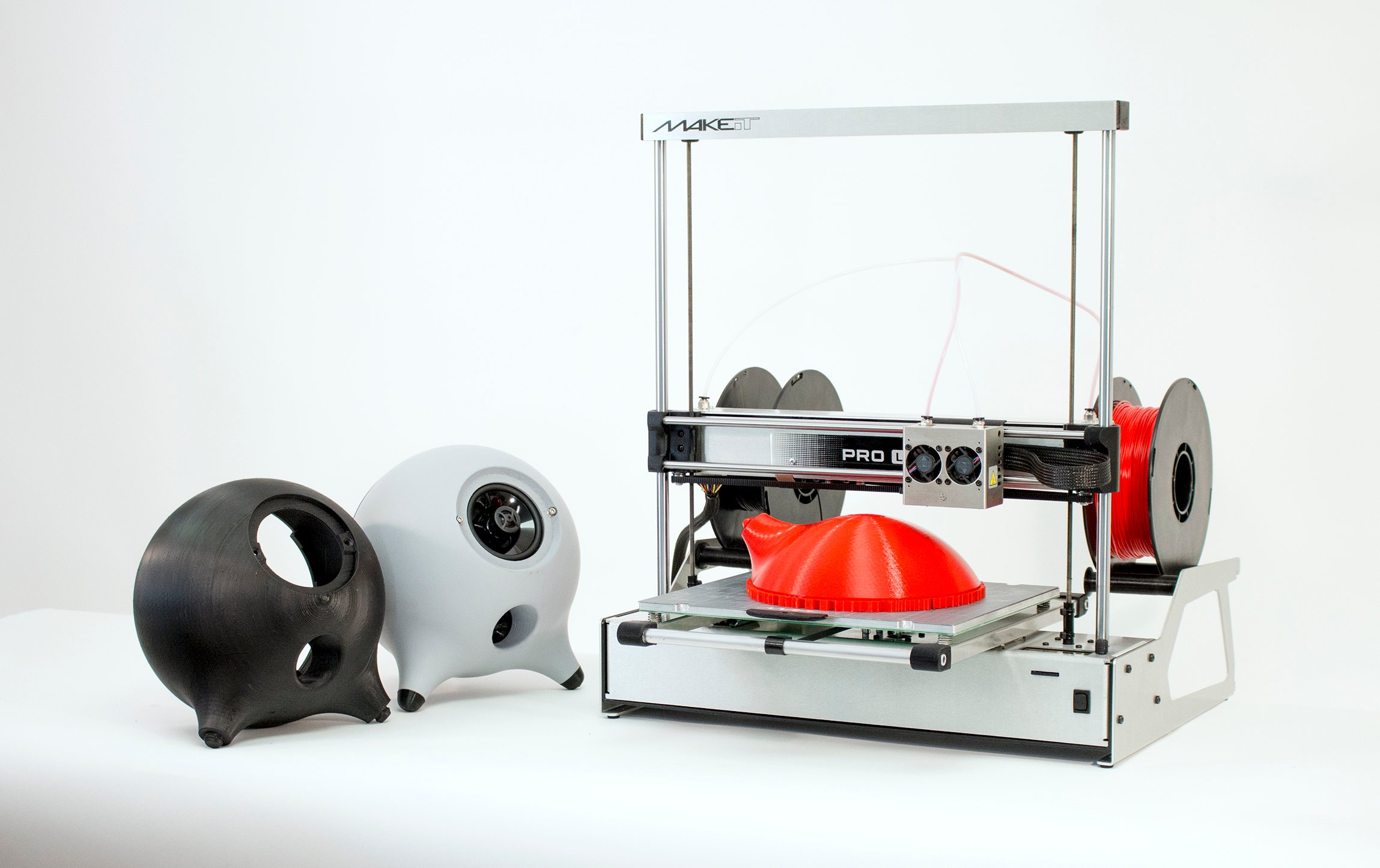
Fabbaloo: Another aspect of the machine I witnessed was very high quality for a desktop extrusion-based system. I understand the PRO-L can print 0.01mm layers. How has the machine been designed to provide this?
Salomo Murtonen: First it should be noted that not all materials and not all part geometries are possible at 0.01mm layers. This layer resolution relies not only on the precision of the machine, but also the material science behind the plastics you’re using. It works great with ABS and PLA, but flexible materials and materials with greater viscosity when melted, like PET, won’t be able to achieve that.
Then there’s the basic mathematical answer, which is by choosing motors, belts, threaded rods, etc. that have the proper step angle, pitch, etc. to allow for discrete motion at that small of a scale, but it also goes a lot deeper than that too.
Extrusion at layers that fine is very difficult to manage, as you’re using just the tiniest bit of filament for each layer. Cooling at layers that fine is very different as well, since your nozzle will basically stay in the same spot without having much filament passing through it at all. We designed our printhead cooling system so that it actually pulls air from beneath, up through the head and away from the part, opposite from most systems that blow air directly onto the part. This allows us to pull contaminants away from the part while also providing a very controllable cooling.
Fabbaloo: How has the PRO-L been received by clients? Have many been sold, and what are customers saying about it?
Salomo Murtonen: There was the immediate reaction that most people love the updated polished aluminum look, but our customers are finding a lot more to appreciate as well. It’s clear to people who use the machine that it’s intended as a tool and not a toy. The durability that comes from our component and material choices in construction is often mentioned and highly appreciated. The combination of build volume, dual nozzles, and high precision still stands apart from most offerings in the same price range. Many of our customers considered more expensive systems like the uPrint before deciding to go with the Pro-L, citing its lower price and operational cost, greater precision capability, smaller size, and accessibility to a wider range of materials. The longer our customers have their printers the more they fall in love with them, they’re just so easy to keep going and going and going. Most of the questions we get from customers are centered around software or the design of their part. The machine is so capable a lot of users have room to learn and grow before achieving everything it’s capable of, but the hardware is rock solid and we’re seeing even beginner users get great results out of the box.
Pro-L was introduced to market in August. Our very first Pro-L customer is Jet Propulsion Laboratory. They will use our Pro-L together with many other tools to build cubeSats, miniature satellites for space research.
Fabbaloo: Where do you see making improvements for future machine releases? What would you like to work on next?
Salomo Murtonen: “Focusing on industrial use” has been our original vision and will be the guideline for our future development. R & D is our strength. We have made significant improvements since our first printer version, clients who bought our original Pro model printer are able to upgrade their older model with many improvements we made for the Pro-M and Pro-L.
We are working on a third model that customer can build 6ft tall object.
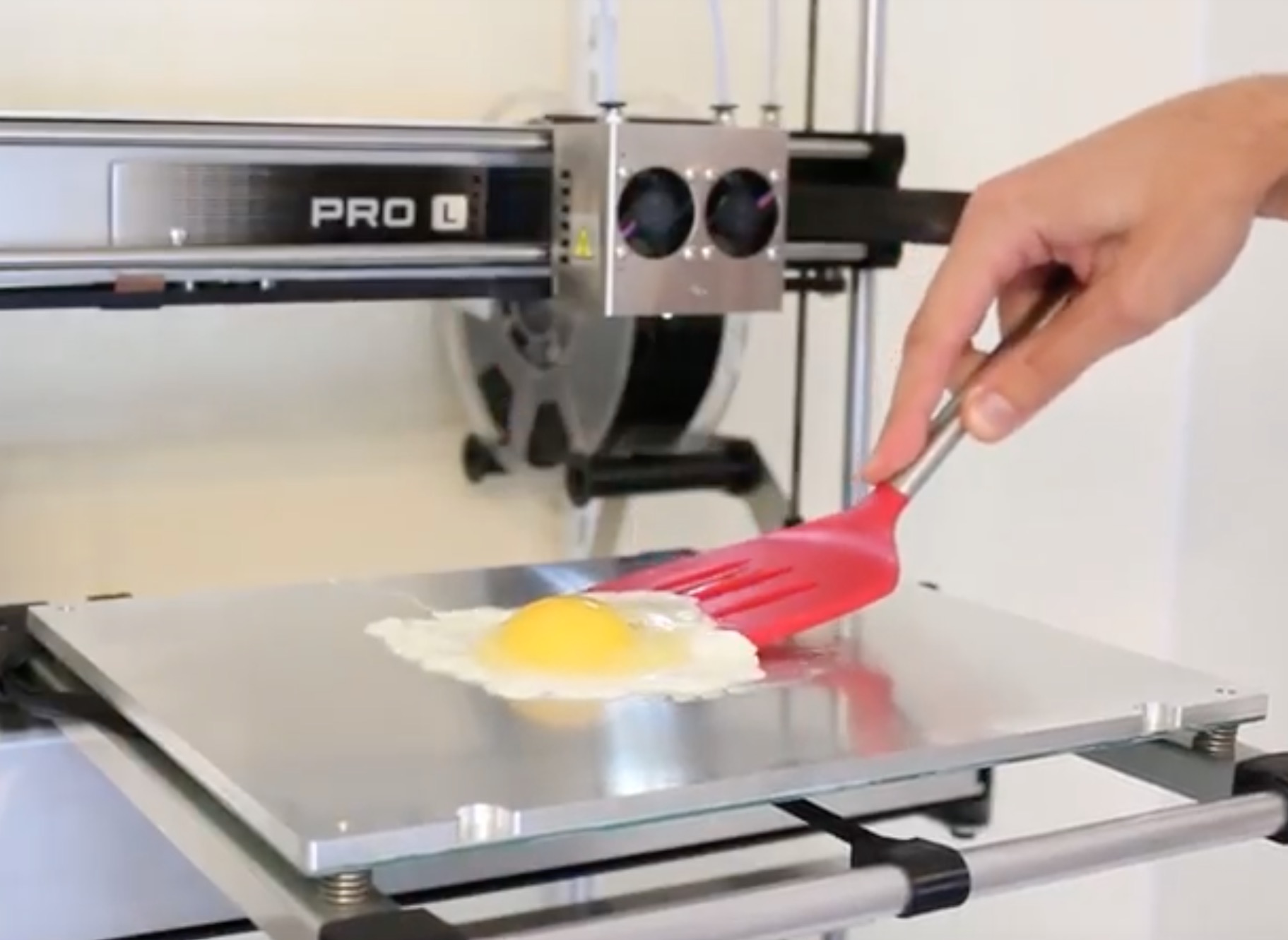
Fabbaloo: Finally, are you still frying eggs on the print bed? (from this video)
Salomo Murtonen: We could probably cook bacon too if we wanted to wait a while for it to finish! I think we should probably add a “do not try this at home” disclaimer to that video. It’s a funny way of demonstrating a very commonly asked question, but it’s probably not sanitary. We’re planning on putting out more tongue-in-cheek videos like this soon.
Via MAKEiT