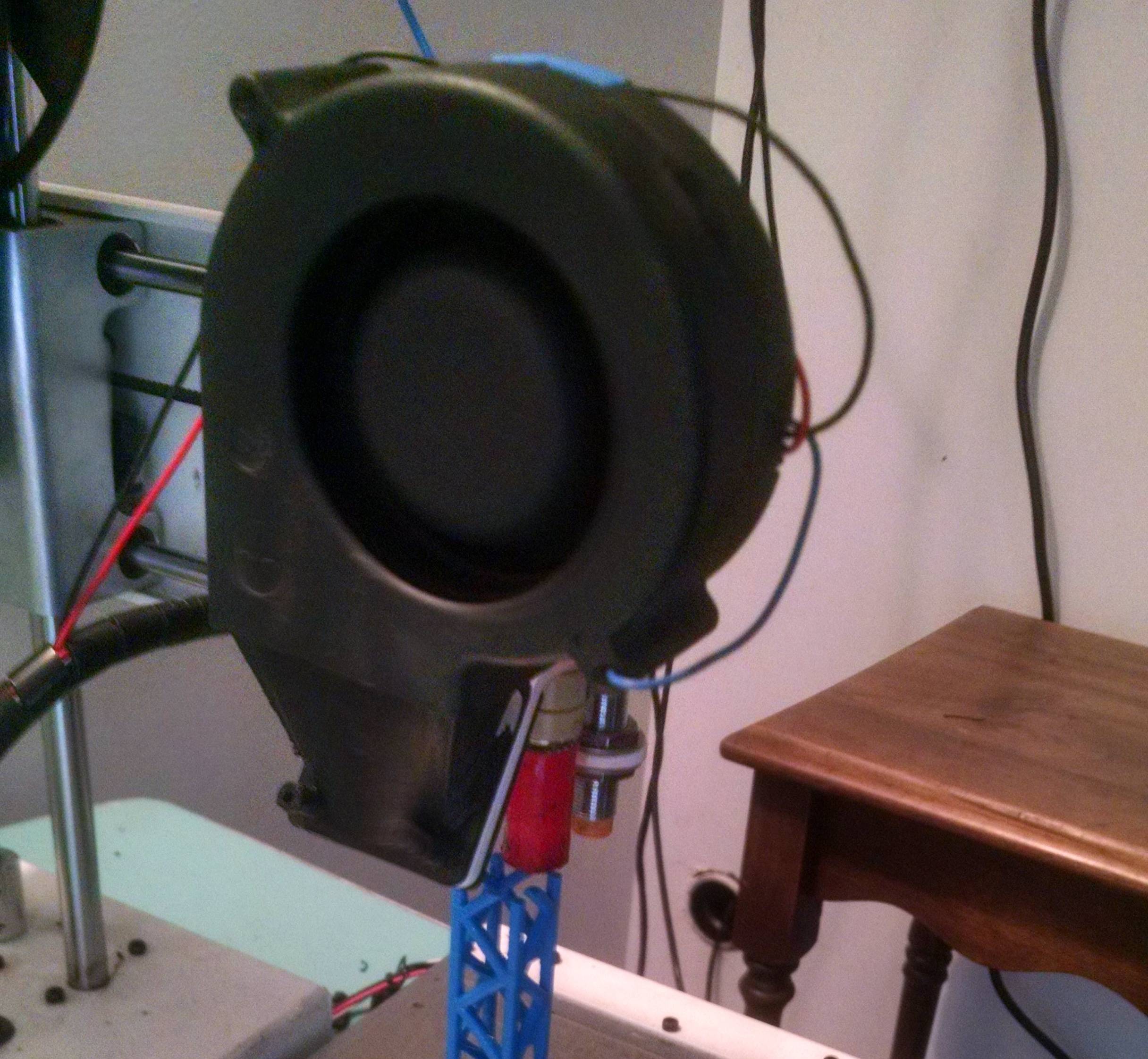
There’s often much discussion of heating issues in 3D printing, but there’s another thermal dimension to consider: cooling.
Everyone understands that in the plastic extrusion 3D printing process, the hot end raises the temperature of the filament to just the right level for extrusion (I like to describe this state as similar to “toothpaste”). The nozzle is then moved about the print volume by the 3D printer’s motion system to gradually extrude an entire object.
But cooling is just as important as heating.
You might be wondering why fans are typically involved in 3D printing, and it’s because of the need for cooling.
Consider this: when the plastic is moving through the hot end and nozzle, it’s completely under control of the GCODE. We know exactly where it is. But once it leaves the nozzle, the plastic is on its own and cannot be controlled.
Therefore it is of extreme importance to make sure the plastic doesn’t move or deform after leaving the nozzle. This is done by literally freezing the plastic as soon as possible, and that’s where the fans come in.
The fans blast ambient air at the freshly extruded plastic in an attempt to cool it off very rapidly.
Why do so? In some cases, cooling matters less because the extruded plastic is simply resting on a previous layer. But that’s not always the case. Sometimes the fresh extrusion has a slight overhang. If not properly cooled, it may droop into the overhang.
It could be even more challenging if there is a “bridge”, where there is nothing at all under the fresh plastic. A string of freshly extruded hot plastic is stretched across a gap. If not properly cooled the bridge will dip. Or even collapse.
This is why fans and airflow around the nozzle are so critical. The fans should not cool the hot end, but should blast the fresh extrusion almost immediately as it emerges from the nozzle.
Theoretically if you had perfect cooling you could safely extruder a horizontal line. I’ve seen bridges of up to 200mm successfully attempted, but this is often challenging.
Poor prints are sometimes the result of ineffective cooling, particularly if you observe droops in overhangs. Some 3D print operators, such as Reddit user bent-grill, have opted for massive cooling subsystems as shown at top.
That’ll get the job done!