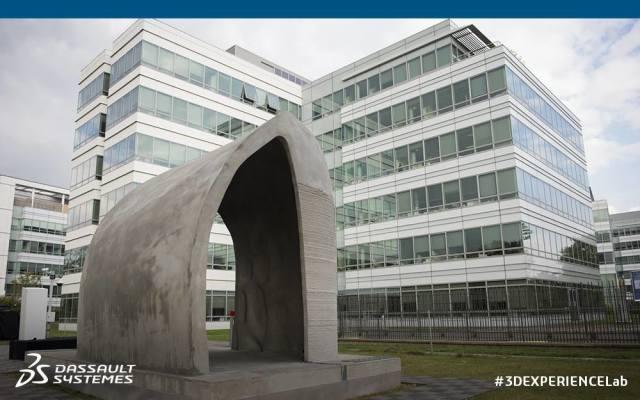
Technological advancements don’t simply affect the lives of individuals, but actually reshape entire societies. What could be more indicative of this power than the change that happens to the buildings in which we live and work?
Deloitte recently highlighted the effects of new technology on our cities and buildings in its 2017 Commercial Real Estate Industry Outlook. In addition to trends associated with data analysis and the Internet of Things (IoT), the global research and service firm examined 3D printing and its role in the world of commercial real estate. Bob O’Brien, Global Real Estate Sector Leader for Deloitte, spoke to ENGINEERING.com about how additive manufacturing (AM) may change the way that buildings are constructed in the near and longterm.
3D-Printed Buildings
So far, a number of 3D-printed buildings have been erected, with China’s WinSun probably the most prolific in this sphere as it 3D prints walls offsite and assembles them on location to construct entire usable structures. In addition to 10 small houses, a villa and a five-story apartment complex, WinSun has 3D-printed an office building in Dubai that is actually being used.
Although the technology is quickly evolving, O’Brien was quick to point out that it may be more than a decade before buildings are 3D printed on a widespread basis, indicating the regulatory concerns around additive construction, particularly in developed countries.
“3D printing is still at early stages in terms of impacting commercial real estate and engineering and construction,” O’Brien said. “I think you’ll see a phased implementation. You’ll see architectural components of buildings using 3D printing within the next decade. I think that here in the U.S., given the regulatory reform that needs to happen and the complexity and sophistication of the buildings that the market demands, we’re a decade or more away from buildings being built using 3D printing.”
Entire buildings may face obstacles in terms of meeting existing construction code, but O’Brien suggested that such components as roofing or siding may be 3D printed first in order to introduce elements of customization into buildings. This will simultaneously demonstrate the capabilities of the technology and provide a stepping stone toward regulatory approval and full-scale implementation.
“The first place we’ll likely see it, for example, warehouses, sheds, relatively simple buildings before we get to more complex buildings like multifamily residential or office or retail,” O’Brien added.
Outside of WinSun’s efforts, O’Brien’s hypothesis is already proving to be true. XtreeE in France has so far 3D printed a structural component for integration into a children’s playground and a concrete pavilion, which serves more of an aesthetic purpose than a functional one. Ai Build, too, has begun with a pavilion before moving on to more ambitious projects. Branch Technology in Chattanooga, Tenn., first 3D printed artistic structures and has only now begun work on an actual dwelling. It remains to be seen if the home it is currently building will actually serve a functional purpose or as more of a proof of concept.
While these companies work to demonstrate the possibilities of 3D printing, there may be regulatory changes that occur to make additive construction easier to integrate into the larger industry, according to O’Brien. “In the U.S., many cities, towns and governmental jurisdictions have strict building codes around the nature of the products that can be used to build a building, primarily focused on things like fire safety, the safety of drinking water and that sort of thing,” O’Brien explained. “In an environment where you’ve got such significant existing building codes, those codes would ultimately have to be adapted to permit 3D printing.”
Read more at ENGINEERING.com