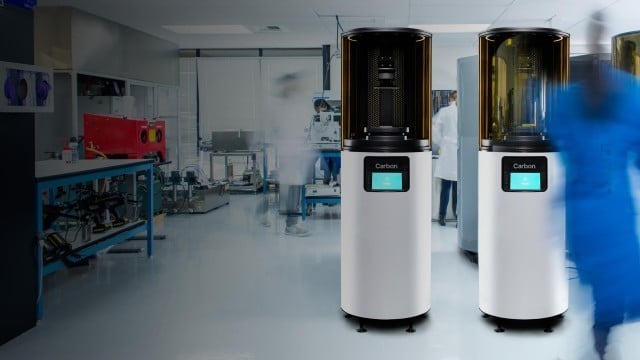
With a stunning reveal during a TED Talk last year, Carbon quickly became the apple of the 3D printing industry’s eye.
While comparisons to Terminator 2 caught the mainstream media’s attention, the speed and capabilities of Carbon’s continuous liquid interface production (CLIP) 3D printing process suddenly revealed to mainstream manufacturers the possibility of 3D printing industrial grade parts in an instant.
The technology was further validated when one of the world’s largest manufacturers, GE, along with Nikon, JSR and BMW, provided Carbon with a whopping $81.1-million investment. To learn more about why this technology is worthy of such a large investment and what that money will be used for, ENGINEERING.com spoke with Kirk Phelps, VP of product management for Carbon.
What Is CLIP?
CLIP is a form of digital light processing (DLP) 3D printing, in that it relies on a projector to cast UV light onto a vat of photopolymer resin, hardening the resin until a complete 3D object is formed. It differs from conventional DLP in that this photocuring process is very fast. Projecting light through an oxygen-permeable window, CLIP is able to print objects continuously, without the need to pause between layers and mitigate the suction forces typically associated with DLP.
Not only does this allow CLIP 3D printing to fabricate objects at 25 to 100 times the rate of other systems, but it results in isotropic strength throughout a 3D-printed part. In parts produced with almost every other 3D printing technique, there are identifiable horizontal layers which have weak vertical bonds that make these components much weaker on the Z-axis than on the X and Y. With CLIP, however, parts are equally strong in every direction.
Phelps explained that this is a key reason that prevents 3D printing from being implemented in the production of end parts.
“Conventional 3D printing technologies all produce parts with layers, which compromise the quality of the parts because they have different mechanical properties along different axes,” Phelps said. “Engineers find this lack of consistency problematic. As a result, most conventional 3D-printed parts are limited to prototyping applications. In contrast, CLIP parts have consistent mechanical properties regardless of axis, similar to injection molded parts.”
CLIP Materials
Once a print has been produced, it undergoes a second curing process that further unlocks the potential of CLIP-printed parts for various engineering applications. Phelps was able to elaborate on how this second curing step differs from the initial 3D printing process.
“This two-stage cure is very important differentiator for us as it allows us to combine the resolution and surface finish of light-based 3D printing with engineering-grade thermoset mechanical properties,” Phelp said. “This combination has never before been achieved by additive technology and it is what allows us to make the final-quality parts that we do. Specifically, light crafts the shape of the part (stage one) and chemistry sets the mechanical properties of the part (stage two). Bottom line for engineers: CLIP parts have engineering-grade mechanical properties and extremely fine surface finish and resolution.”
So far, Carbon has been able to develop a variety of five different photopolymers that exhibit various mechanical properties. In addition to a general-purpose resin, Carbon has created rigid, flexible and highly elastic polyurethanes, as well as a high temperature–resistant and strong cyanate ester. These materials will only expand, given the fact that former DuPont Chair and CEO, Ellen J. Kullman, joined the Carbon Board of Directors and Carbon entered into a material development agreement with Kodak.
Read more at ENGINEERING.com