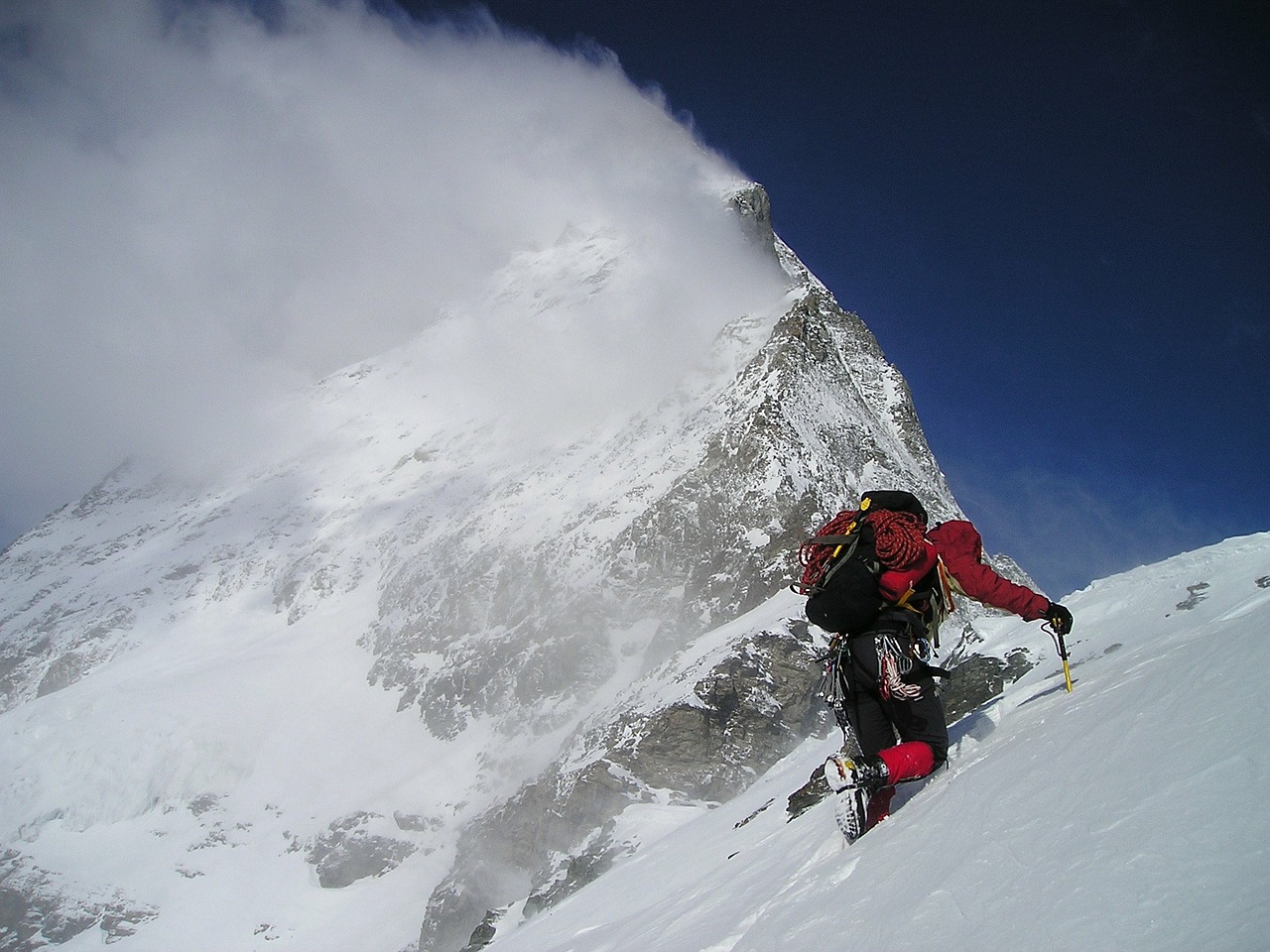
3D printing may be on the verge of a dramatic shift in focus as we’ve overcome one mountain, only to be faced with another.
I’ve been following 3D print technology for almost a decade now and have seen a great many ideas rise (and sometimes fall) over that period. Enormous progress has been made, and everyone agrees there is much left to do. But what, exactly?
In the desktop 3D printing world it’s been fascinating to observe how innovative companies have been gradually improving their processes by incrementally adding features that make 3D printing experiences better. Some of the improvements include:
- More robust structural and motion systems to ensure accurate prints
- Effective bed adhesion systems to ensure prints succeed
- Heat capture and control to avoid warped parts
- New materials designed “for 3D printing” that print much more easily
- Finer nozzles and extruders to enable very fine print resolution
- Complex slicing software to ensure prints are successful
- Easy-to-use interfaces that enable more rapid human operation
- Multiple hot ends to extrude dissolvable support enabling allowing any geometry to be 3D printed
But this is what I am now thinking: most of the improvements over the past few years have really been all about ensuring we get a correct and accurate SHAPE out of the 3D printer.
And these moves have largely succeeded: most reputable desktop 3D printers these days can reliably produce arbitrary shapes on demand. Some readers may not have been around, but years ago when the first devices appeared, it was almost a miracle to 3D print the object correctly the first time. I personally recall seeing many unsightly blobs sitting on my print bed, while wondering what possible parameter changes could improve the situation. That scenario doesn’t happen much anymore unless you’re designing your own 3D printer.
So what’s next? What happens when you can actually produce any arbitrary shape on demand?
It’s the material properties.
Engineers will know there are, in our universe, countless types of materials with a huge variety of chemical, mechanical and thermal properties. Outside the world of 3D printing these materials are the menu from which the complex objects of today are made. Pick the right material for the job, it just makes sense.
However, that’s definitely not the case in 3D printing. What put me on to this concept was that I had been avoiding ABS plastic. ABS, while popular, is challenging to 3D print due to its tendency to warp. Instead I simply switched to PLA and everything is fine. I can produce the shapes I want easily.
But what’s really going on here? We’ve been picking our 3D print materials largely based on whether they print properly, as opposed to whether they meet the requirements of the end function of the object being printed.
In fact, some of the recent custom-designed plastics boast of “printability” features, and oh, by the way they are also stronger. It’s the printability that seems important, not the other properties.
In the end we seek objects that function, and we must make them of materials that aid that function.
Ideally we need to have a much vaster array of printable materials at our disposal.
Some work has taken place in this regard, with the introduction of hybrid PLA filaments and the ability to 3D print materials such as nylon, PETG and HIPS, but there is so much more.
We may need new machine designs, new 3D printing processes and new 3D print software, and this will certainly take much time.
In the meantime, by all means 3D print that shape, but as for functions, not so much.