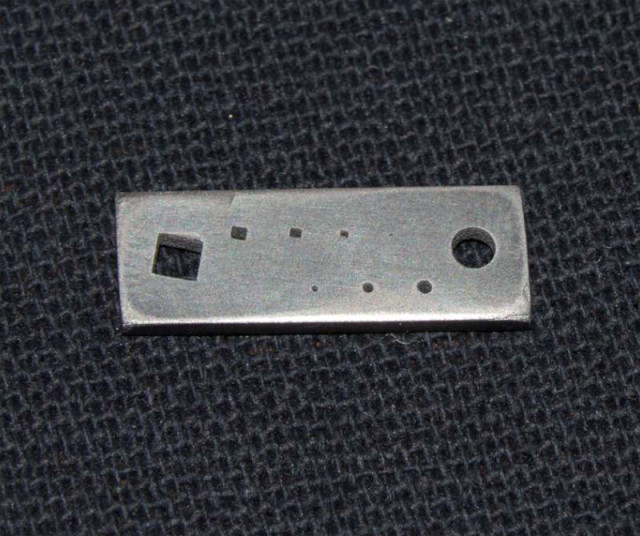
It’s no secret that metal 3D printing is becoming big business.
Just ask GE Aviation, which just purchased two of the leading metal 3D printing companies in the industry. As the technology becomes integrated into the mainstream manufacturing supply chain, other 3D printing firms are going to have to keep pace with this rapidly evolving industry.
Prodways, the 3D printing subsidiary of the French Groupe Gorgé, is making its own advancements in the space by developing a new metal 3D printing material using the company’s existing technology. Developed with the Alternative Energies and Atomic Energy Commission (CEA), a French public research organization, this process expands on Prodways’ already expanding technology portfolio, which includes selective laser sintering (SLS) and rapid digital light processing (DLP) for metal casting.
In an exclusive scoop for ENGINEERING.com, Alban D’Halluin, managing director of Prodways, was able to discuss the implications of this new material technique, as well as the French firm’s other unique 3D printing technologies.
3D Printing with Metal Paste
The R&D group at Prodways has spent two years working with CEATech LITEN, a subsidiary of CEA, to create a novel metal 3D printing technique that fuses metal powder with an organic binder. Prodways’ existing V6000 machine applies the firm’s existing MOVINGLight technology to viscous pastes. Up until now, the V6000 has been used to 3D print ceramic objects. However, D’Halluin explained that Prodways has been able to expand the material set to include a wide range of metals.
Prodways’ MOVINGLight systems use one to two DLP projectors, mounted on an X-Y gantry, to cast UV light down onto a vat of photocurable resin. This setup allows Prodways’ ProMaker machines to take advantage of a robust build volume while maintaining rapid printing speeds. These combined strengths, then, position the MOVINGLight printers as batch manufacturing systems capable of high throughput.
The new material developed for the V6000 machine combines metal powder with a binder in such a way that Prodways is able to print a viscous, metallic paste quickly and with a fine level of detail. The printed object is then sintered in an oven, which burns out the organic binder and leaves only a dense metal object.
Creating the material was no easy task, according to D’Halluin. “The challenge to develop such a material is to combine three elements that are very hard to get together,” D’Halluin said. “You need to get some reactivity so that you can actually send the UV light to go deep enough into the material to cure it. You need to get the material to be stable enough so that it will cure quickly, but you also need a lot of metal powder in the material to actually be able to do the final sintering. The last requirement is that you need to be able to de-bind the metal powder and the binder so that you actually produce the final part when you put it in the oven.”
After much research, Prodways and the CEATech LITEN team were able to develop a metallic paste that is stable enough, cures quickly enough and contains sufficient metal powder to produce a metallic end part. The V6000 is able to spread a very thin layer of the paste, such that Prodways is able to cure a 50-micron layer in just one second using a variety of metal powders. So far, Prodways has printed with titanium and Inconel, but D’Halluin believes that it is also possible to print with copper, cobalt-chrome and steel.
Upon sintering, Prodways is able to achieve more than 90-percent density in the final metal component. For some applications, some porosity may not be a problem. D’Halluin suggests that, because the V6000 can achieve 99-percent density with ceramics, such a high level of density will be possible with metals as well.
Of the quality of the process, D’Halluin said, “We are able to get very accurate and very precise parts. That’s really coming from the precision of the DLP and we’re very happy with the surface finish of the parts that we have printed.”
The Benefits of MOVINGLight Metal 3D Printing
The ability to 3D print metal pastes brings some distinct advantages, both over traditional manufacturing techniques and metal 3D printing specifically.
“We are now able to explore a wide variety of metals. Now, it’s time to really explore what applications and what processes can benefit from this technology,” D’Halluin said. “Typically, we would have to approach applications that today use the metal injection molding [MIM] process.”
MIM also involves the combination of a fine metal powder with a binder; however, unlike with Prodways’ 3D printing process, this feedstock injected into a mold to create batches of parts to be sintered in an oven. D’Halluin explained that MIM is limited in that the feedstock is difficult to extrude, ultimately limiting the complexity and detail of the mold that can be used. Moreover, all molding processes are unable to produce certain geometries, such as those with interior cavities and tubes.
“We are bringing the flexibility of 3D printing to the MIM process and that is really what we are now going to explore in more depth,” D’Halluin said.
At the same time, 3D printing metal with MOVINGLight offers some benefits that other 3D printing processes such as direct metal laser sintering (DMLS) can’t. MOVINGLight is already a fairly rapid technology, capable of manufacturing sizeable batches of parts. The V6000 specifically has a build volume of up to 5 in x 20 in x 6 in (127 mm x 508 mm x 152 mm) and can print at up to five times faster than DMLS techniques. The combination of size and speed, in this case, would enable batch manufacturing of metal parts.
Read more at ENGINEERING.com