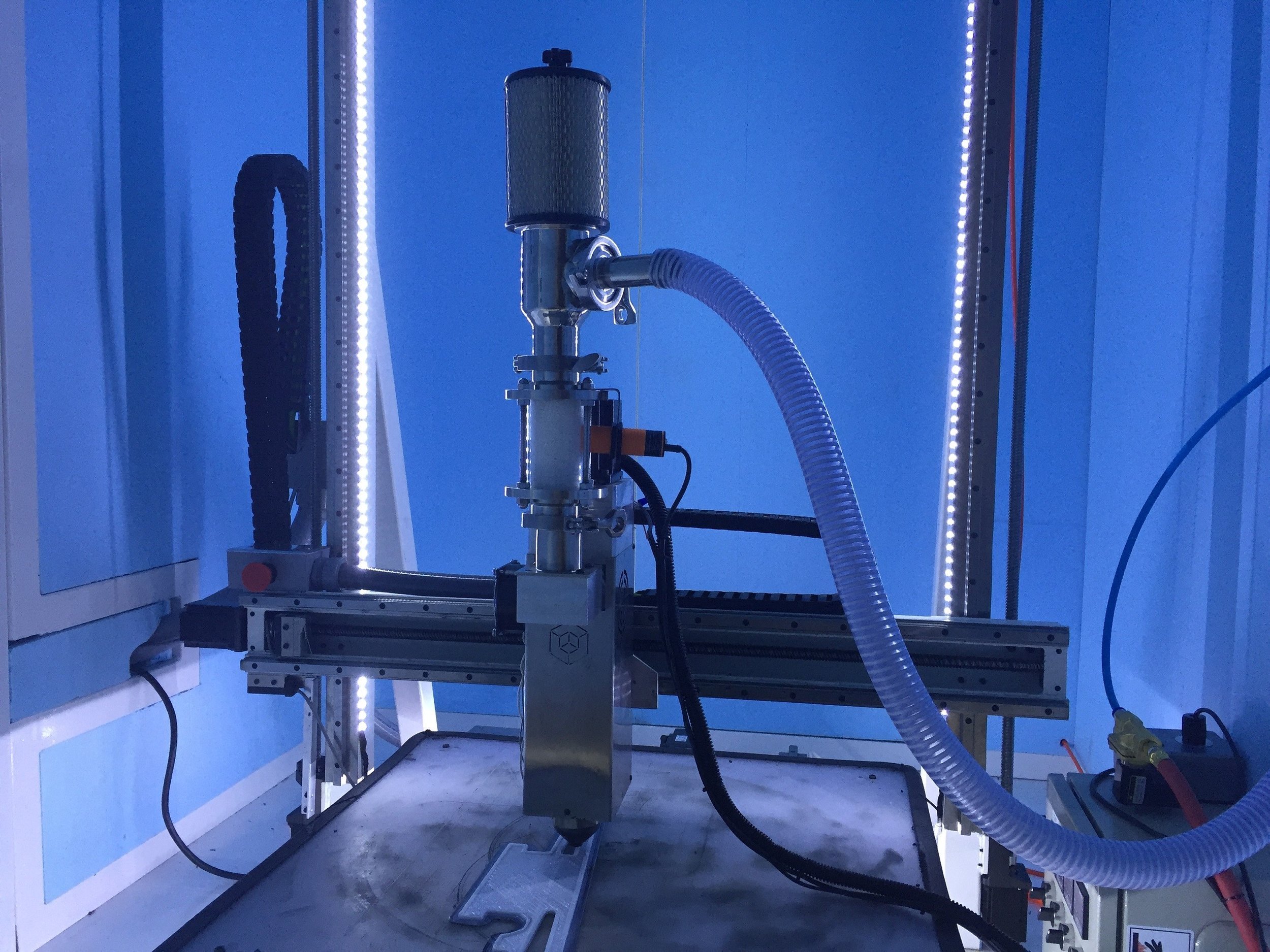
Titan Robotics announced plans to incorporate a pellet-fueled extruder on their massive Atlas 3D printer.
Titan Robotics is a small 3D printer startup company based in Colorado, founded by Clay Guillory. We told their origin story here earlier this year, and since their launch, they’ve been quite successful producing ultra-large, highly-reliable 3D printers.
But all of these machines have used the familiar filament-based extrusion systems commonly used on much smaller 3D printers. IT works, but there are a couple of major constraints: the cost of filament is high, and there is a limit to the volume of plastic a filament machine can extrude per hour.
Three other vendors of large 3D printing gear have also realized this problem: BigRep (pellet strategy), Stratasys (new pellet machine concept) and WASP (pellet extruder) have all determined that use of material pellets instead of filament can solve the issues.
Now Titan Robotics jumps on the same train by announcing a joint project with Push Plastics to produce a practical pellet extruder for the Titan Robotics Atlas machine. The Atlas, if you’re not familiar with it, is a custom-built high-precision, high-reliability enclosed 3D printer with a build volume of 915 x 915 x 1220m.
Printers of that size have one major issue: it takes a long time to complete such large prints, not only days, but sometimes weeks in length! That’s too long to be practical in some cases.
The answer comes in the design of a high-volume pellet extruder. Titan Robotics explains what they’re up to:
Through working with Push Plastic, Titan was able to swap out a traditional filament extruder with the pellet extruder directly onto the Atlas. Because the Atlas is a robustly designed machine, no other auxiliary equipment was needed to adapt the system for pellet extrusion.
Even better, the design of this pellet extruder should enable use of materials beyond mere PLA, such as ABS, Polycarbonate and more. How does it do so? The Atlas is an enclosed cabinet that can be heated, drastically reducing material warp issues.
But here’s the most important statistic in the announcement:
Titan Robotics was able to print with ABS resin in the heated enclosure with flow rates of 5 lbs per hour. Titan is currently working in conjunction with Push Plastic to further optimize printing in an enclosure with ABS and Polycarbonate and to increase flow rates even more.
Whoa! That’s hugely fast! To put this in perspective, that’s like 3D printing an entire 1kg spool of PLA in only 26 minutes! Most desktop 3D printers would take days to run out an entire spool. While the extrusion is rather coarse, fine details really don’t matter on larger prints, so resolution is not an issue. This new feature will make the Atlas one of the fastest large-format 3D printed around.
And it will be far cheaper to operate, as well, since the cost of pellets by weight is often 10X less than the cost of filament.
So it now seems that large-format 3D printers had all better start using pellets, or your equipment will soon not be able to compete on operational costs.
Via Titan Robotics