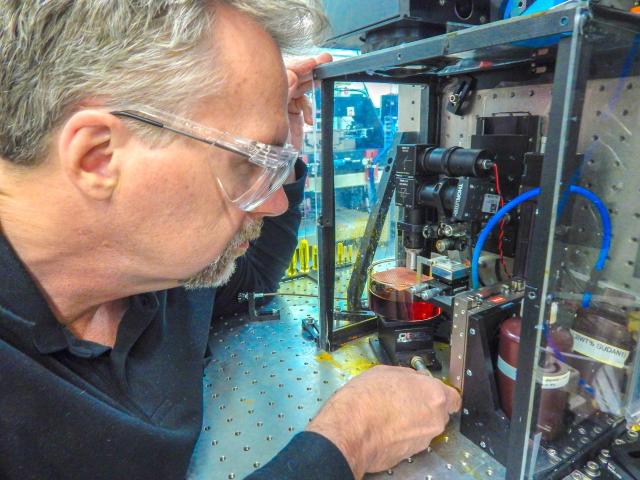
U.S. government labs have become involved in 3D printing in a big way, necessarily adopting the technology for research and development purposes since the technology’s inception, but also pushing the boundaries of what 3D printing is truly capable of.
While Oak Ridge National Laboratory, located on the East Coast, has developed large-scale additive manufacturing (AM) for producing such components as complete auto chassis, Lawrence Livermore National Laboratory (LLNL) is taking 3D printing down to the micro- and nanoscale, manipulating the physical properties of objects by modifying their inner geometries.
ENGINEERING.com spoke with Christopher Spadaccini, director of the Center for Engineered Materials, Manufacturing and Optimization at LLNL, to learn about some of the research that the lab is conducting in this area, as well as the cutting-edge AM technologies that make this research possible.
Micro-SLA 3D Printing for Macro Applications
While LLNL works to advance existing commercial 3D printing systems for its own research, the lab also develops technology in house. Among the techniques created by LLNL is a process called micro-stereolithography (micro-SLA).
The micro-SLA process is similar to digital light processing (DLP) 3D printers, which use DLP projectors to cast UV light onto photosensitive resins, gradually building the object one layer at a time. The process replaces the DLP projector with a light-emitting diode (LED) that lights up a micromirror or liquid crystal on a silicon chip. With the micromirror or liquid crystal displaying digital photomasks of each layer, the resin is cured as the substrate is lowered.
This technology allows Spadaccini and his team to create complex micro-geometries very quickly, allowing for the 3D printing of architected materials, also known as metamaterials. Spadaccini describes the concept of developing architected materials as “creating geometry out of the right constituent material at the right length scale to give you really unique properties, like high stiffness and strength at low densities.”
By 3D printing complex lattice structures at the microscale, for instance, it’s possible to design parts that are extremely lightweight, but which have enormous strength due to the way that geometries of the objects behave on the microscale. Voids allow the prints to have a reduced mass, while the tensegrity of the microstructures maintains stiffness and strength.
It’s important to note that LLNL is world famous for its supercomputing capabilities, so, while the manufacturing technology is essential to producing these metamaterials, the lab is developing 3D printing processes to bring engineered geometries to life. By simulating the physical characteristics of given shapes made from specific materials, LLNL aims to produce programmable matter.
Read more at ENGINEERING.com