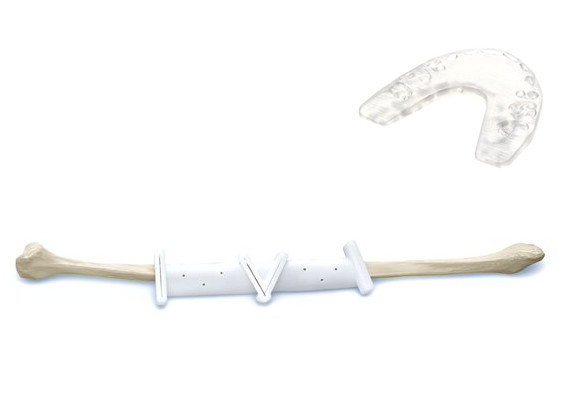
Healthcare is one of the industries to most dramatically see changes occur due to the use of 3D printing technology.
In fact, market research firm Gartner suggests that it is the medical sector that is leading the advancement of 3D printing over other industries.
3D printing has already become the dominant technology used to manufacture patient-specific hearing aids and dental aligners and, more recently, 3D printing has become increasingly leveraged for the manufacturing of patient-tailored implants and instruments for craniomaxillofacial (CMF) reconstruction and knee and hip replacements. This is clearly just the beginning for additively manufactured products in the medical space, which will one day include 3D-printed organs and patient-specific pharmaceuticals.
Among the large industrial players to adopt 3D printing for the production of medical products is Johnson & Johnson, a multinational corporation with some 250 subsidiaries across 57 countries and a market cap of $323.8 billion. While the multinational corporation’s 3D-printed orthopedic implants have been on the market for several years, Johnson & Johnson is also partnering with some of the most exciting firms in the 3D printing space, such as Carbon, HP, 3D Systems, Organovo and Materialise.
To learn more about how the corporation will leverage the technologies from these firms, I spoke with Joseph Sendra, worldwide vice president of Manufacturing Engineering and Technology for Johnson & Johnson. As one might expect from such a large multinational corporation, the executive could not divulge too much about what Johnson & Johnson is working on behind closed doors, but Sendra was able to lay out the corporation’s larger vision for 3D printing technology.
3D-Printed Implants and Instruments
3D printing has long been adopted by manufacturers as a means of prototyping during the design process, but starting several years ago, Johnson & Johnson subsidiary DePuy Synthes began using the technology to produce patient-specific instruments and implants.
Sendra described the work being performed by DePuy Synthes, “We have a product line called TRUMATCH in our orthopedic segment that consists of implants and surgical guides for CMF surgery, and resection guides for knees that are personalized today. These personalized devices have complex geometries and are provided on demand for surgical applications in the CMF space and knee surgery.”
TRUMATCH CMF uses a patient’s CT scan and then clinical engineers are able to create patient-specific implants and surgical guides. While patient-specific implants ultimately fit into a patient’s anatomy with fewer complications, surgical guides are used during an operation to direct a doctor in how to cut the bone and accurately locate the implant, taking the guesswork out of delicate procedures and reducing time in the operating room. An added benefit that 3D printing brings to patient-specific implants is the ability to fabricate complex geometries that are difficult to produce from subtractive methods.
The TRUMATCH Knee offering uses a three-dimensional computerized scan (CT) of the patient’s leg to create surgical guides that are designed based on the patient’s unique anatomy. The process, which was designed internally, has had a long term partnership with Medical Modeling, now 3D Systems. All surgical guide design, communication with surgeons and the overall product lifecycle are managed by a dedicated team based in Warsaw, Ind. Upon surgeon approval, the electronic file is securely transferred, 3D printed at 3D Systems, and then returned to DePuy Synthes for final assembly, sterilization, and shipment.
Earlier this year, DePuy Synthes TRUMATCH CMF announced the expansion of its existing partnership with Materialise, a leader in the medical 3D printing space due to its 25 years of experience as a 3D printing service provider and software developer. Materialise had already produced DePuy Synthes’ patient-specific surgical guides, but it will now also supply the Johnson & Johnson subsidiary with patient-specific CMF implants. These implants will be sold through DePuy Synthes TRUMATCH CMF Solutions in Australia and Europe, excluding France.
Sendra pointed out that, while 3D printing is an important technology for bringing patient-specific implants and instruments into existence, the software is at least equally crucial in making these designs possible. “Our focus areas include, but are not limited to, the personalization of instruments and devices and software related to patient-specific technology. Really, that’s what the additive space brings to healthcare. It’s not so much about the manufacturing technology itself. It’s about the enablement of personalized solutions specific to you and I and people like us. That’s what we’re really getting in the additive space,” Sendra said.
He added, “Think of it as an ecosphere of health-care personalization anchored in 3D printing, but that 3D printing is essentially the enabler. There’s a lot more around it that’s necessary to make it happen.”
In that way, DePuy Synthes TRUMATCH CMF could not have found a better company to partner with than Materialise. In addition to fabricating individually tailored guides and implants through its large 3D printing facilities, the Belgian company has long been developing software for use with 3D printing. The firm’s MIMICS Innovation Suite allows the end user to quickly render models from CT images and to design personalized devices from the rendered patient images.
Materialise’s ProPlan CMF planning software has been developed for TruMatch CMF to allow their clinical engineers to collaborate with doctors in a virtual setting to pre-operatively plan the surgery, define the implant shape, and design the surgical guides, resulting in an output file that can be sent to a 3D printer to product an anatomic model or surgical guide. With DePuy Synthes TRUMACTH CMF , Materialise has advanced the pre-operative planning capabilities of their ProPlan CMF and Mimics software to enable surgeons to optimize their plans prior to surgery, leading to improved accuracy and efficiency in the operating room.
Given the work that Johnson & Johnson has performed with Materialise to develop this software through DePuy Synthes TRUMATCH CMF, it may be that the corporation will continue its work in software development, just as it pushes to create new 3D-printed implants and instruments.
Read more at ENGINEERING.com