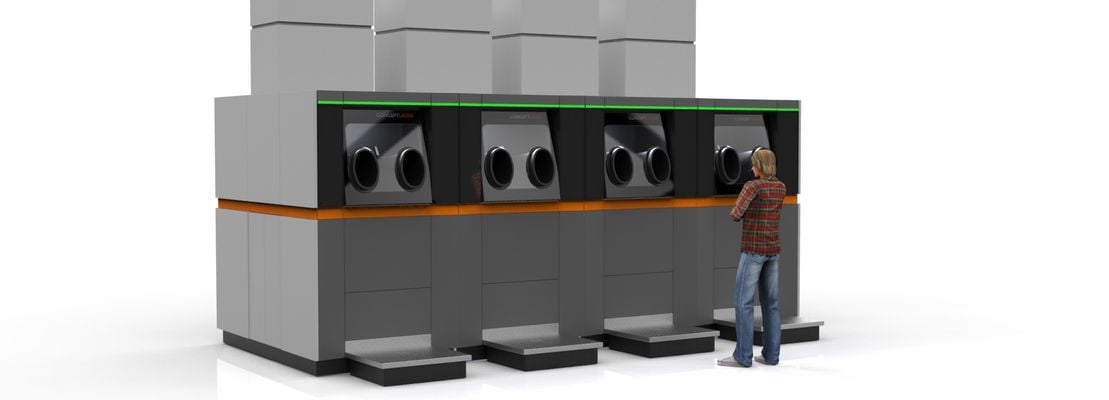
It’s contagious! Concept Laser has joined several other players in producing a “Smart Factory” based on their 3D printing technology.
The sixteen-year old German company has been producing a line of competent metal 3D printers that are widely used. But now they’re announcing something a little different. Their new machine architecture attempts to optimize the making process by de-coupling “pre-production”, “production” and “post-production.” steps.
The new architecture involves “handling stations” and “build and process units” that are entirely separate. The idea is to make the entire workflow more efficient by allowing some activities to take place in parallel. This also permits companies to implement scalable 3D printing solutions by configuring the optimum set of units.
The new architecture also includes a powerful new laser component that includes no less than four 1,000W lasers building within 400 x 400 x 400mm chamber. This is a very flexible solution that not only will enable much faster 3D printing, but also reliability: if one laser fails, the remainder can complete the print.
There is also a 2-axis coating system in the new architecture that is said to be more efficient time-wise. It includes a toll changer that can provide a great degree of flexibility.
One very interesting feature is a new method of handling material. Typically the powdered metal materials are manually dealt with per machine, resulting in some downtime while material handing takes place. In the new architecture the material is kept in “modules” that are automatically moved about, saving labor and increasing uptime.
This is a big step for Concept Laser and should result in a very powerful platform that would much more easily fit into a factory scenario – and especially an Industry 4.0 configuration.
Via Concept Laser