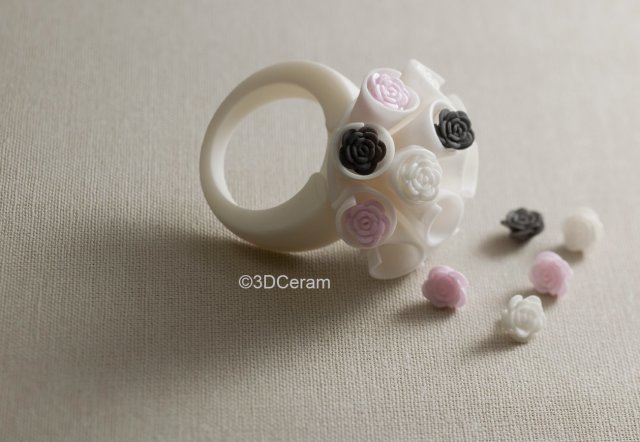
While ceramics may be among the oldest and most widespread of materials used by humanity, ceramics 3D printing has a much more narrow set of applications.
For that reason, there are only a handful of companies that manufacture 3D printers specifically for 3D printing with ceramics. Among them is the French firm 3DCeram, producers of the Ceramaker 3D printer.
The Ceramaker is a stereolithography (SLA) 3D printer that 3D prints photocurable ceramic pastes made up of alumina, zirconia or hydroxyapatite (HA). With a build volume of 300 mm x 300 mm x 110 mm (11.8 in x 11.8 in x 4.3 in), the system is capable of producing objects with layer thicknesses as fine as 25 microns (0.001 in).
In addition to high resolution and accuracy, the Ceramaker produces high-strength parts with a low coefficient of thermal expansion, low density, high abrasion and corrosion resistance and good chemical stability. Unused material can be recycled and reused to decrease material wastage.
The materials produced for the Ceramaker so far have various distinct characteristics. Alumina, or aluminium oxide, is an electrical insulator with high thermal conductivity, hardness and resistance to wear and chemicals. The material is, therefore, suitable for use in cutting tools, as an abrasive or for use in electronics.
Zirconia, or zirconium dioxide, has high thermal stability, good hardness and resistance to wear and chemicals, making it ideal for 3D printing jewelry. Our own bone mineral is a modified version of HA, which makes the material especially suited for creating biocompatible implants or other situations in which bone must be replaced.
How the Ceramaker Works
The Ceramaker is an SLA 3D printer, directing a 355-nm UV laser at galvanometer mirrors that deflect the light onto a layer of photocurable resin infused with ceramic particles. With each layer of a print, a blade coats the print bed in a thin layer of this ceramic paste before the laser light hardens the photopolymer within the paste. The print bed is then lowered incrementally, and a subsequent layer of paste is applied to the print bed.
The process is repeated until the object is finished, at which point the uncured paste is scraped away for reuse. As the print is gradually revealed, excess material is further rinsed off until only the desired object remains. This “green” part is then placed into a furnace, which debinds the resin and sinters the ceramic, resulting in about 20 percent shrinkage.
DETEKT, a Taiwanese 3D printer reseller and 3D printing and engineering service provider, employs a number of engineers responsible for performing such duties, including converting patient CT scans into 3D printable implants. Key Liu, responsible for quality and regulatory affairs at DETEKT, explained that post-printing shrinkage requires special care: “[U]sing this technology requires excellent CAD skills because ceramic materials experience high shrinkage of roughly 19 percent, and designs that are too thin or too thick can lead to product failure after sintering.”
Read more at ENGINEERING.com