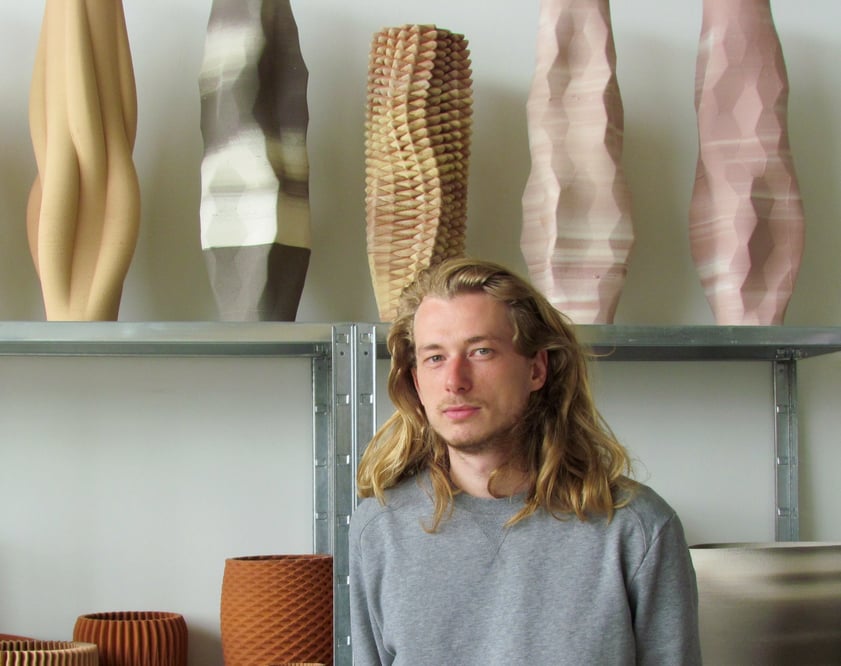
In a tiny workshop located in a repurposed aging factory in Eindhoven lies one of the most interesting 3D printers in the world: Olivier van Herpt’s ceramic 3D printer.
The machine is the invention of designer Olivier van Herpt, who seems to have created a machine of great power and capability.
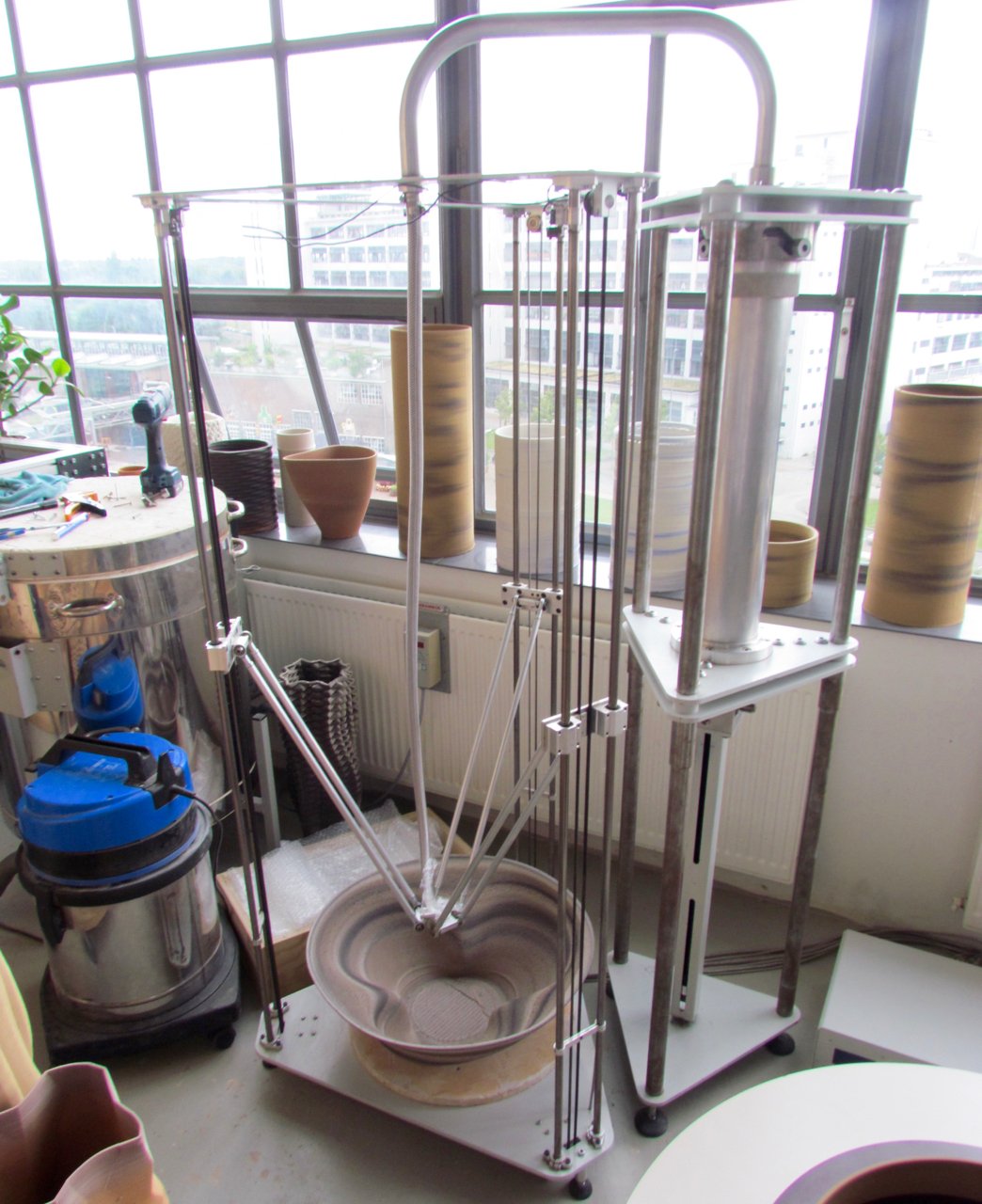
But how did he arrive at such an invention? In school he worked on ceramics, and also 3D printing in plastics with a small OrcaBot. He found, as so many designers do, that 3D objects printed in plastic are not always in demand. He says, “It was hard to make valuable objects in plastic.”
But having knowledge from his studies, van Herpt decided to make the switch to a material that potentially could offer the ability to make more valuable 3D objects: ceramics.
Unfortunately, there were no commercially available, inexpensive ceramic 3D printers available for purchase at the time, so the ingenious van Herpt simply made one himself.
Then it gets interesting: he found that while he could build a delta-style 3D printer to extrude wet clay, there was a serious problem with the output from the machine. Wet clay simply isn’t strong enough to build interesting shapes, because such attempts result in collapse.
This is the case with other ceramic printers today: they all seem to use wet clay and are thus limited by the poor strength of the material.
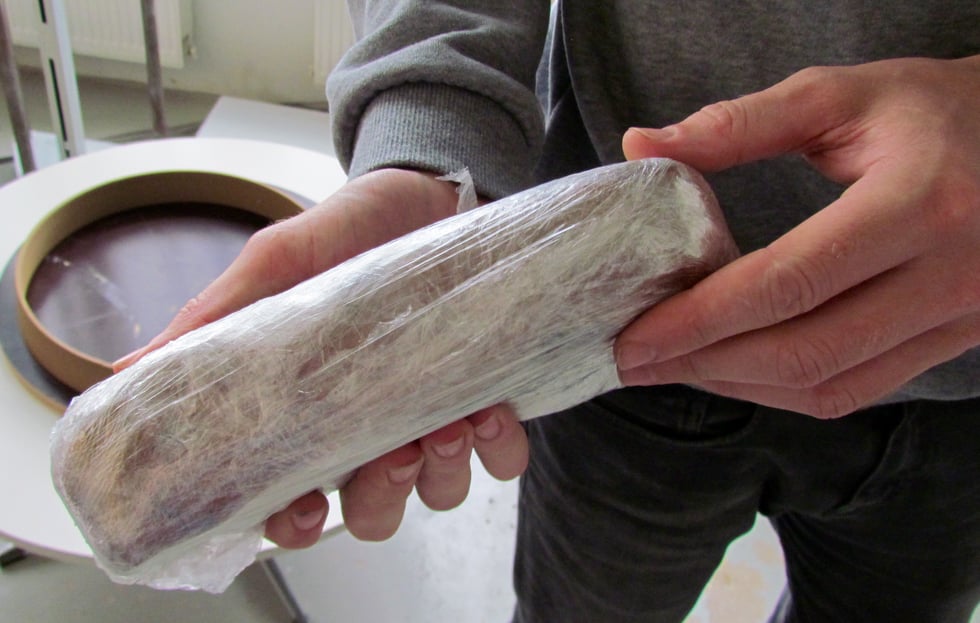
van Herpt decided to build a machine that would instead use hard clay, the same stuff used by artists to produce clay works. It typically comes in hard bricks like the one shown here. If you’re not familiar with this stuff, it takes a bit of effort to push your thumb into it and make a depression.
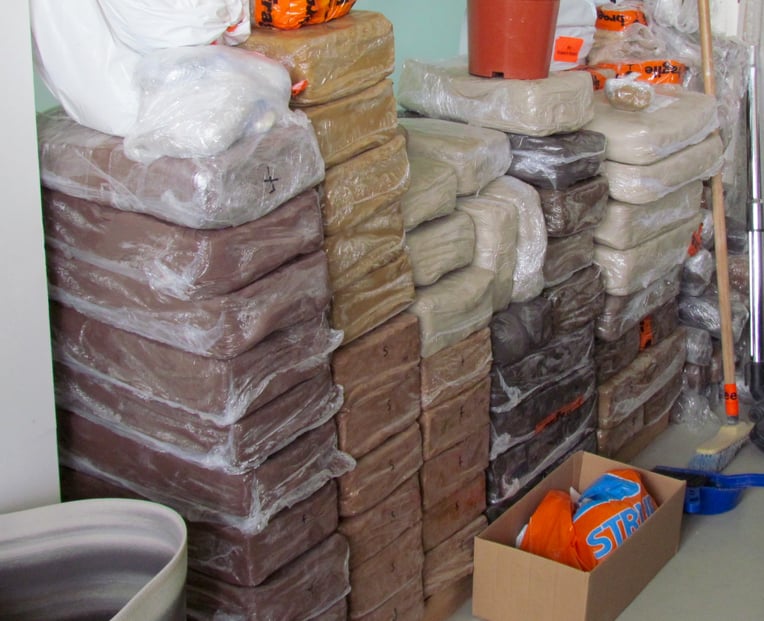
But how could you extrude such material? Wet clay designs usually involve compressed air to push the slurry of clay through tubes to the extrusion point, but that definitely would not work with the much harder clay.
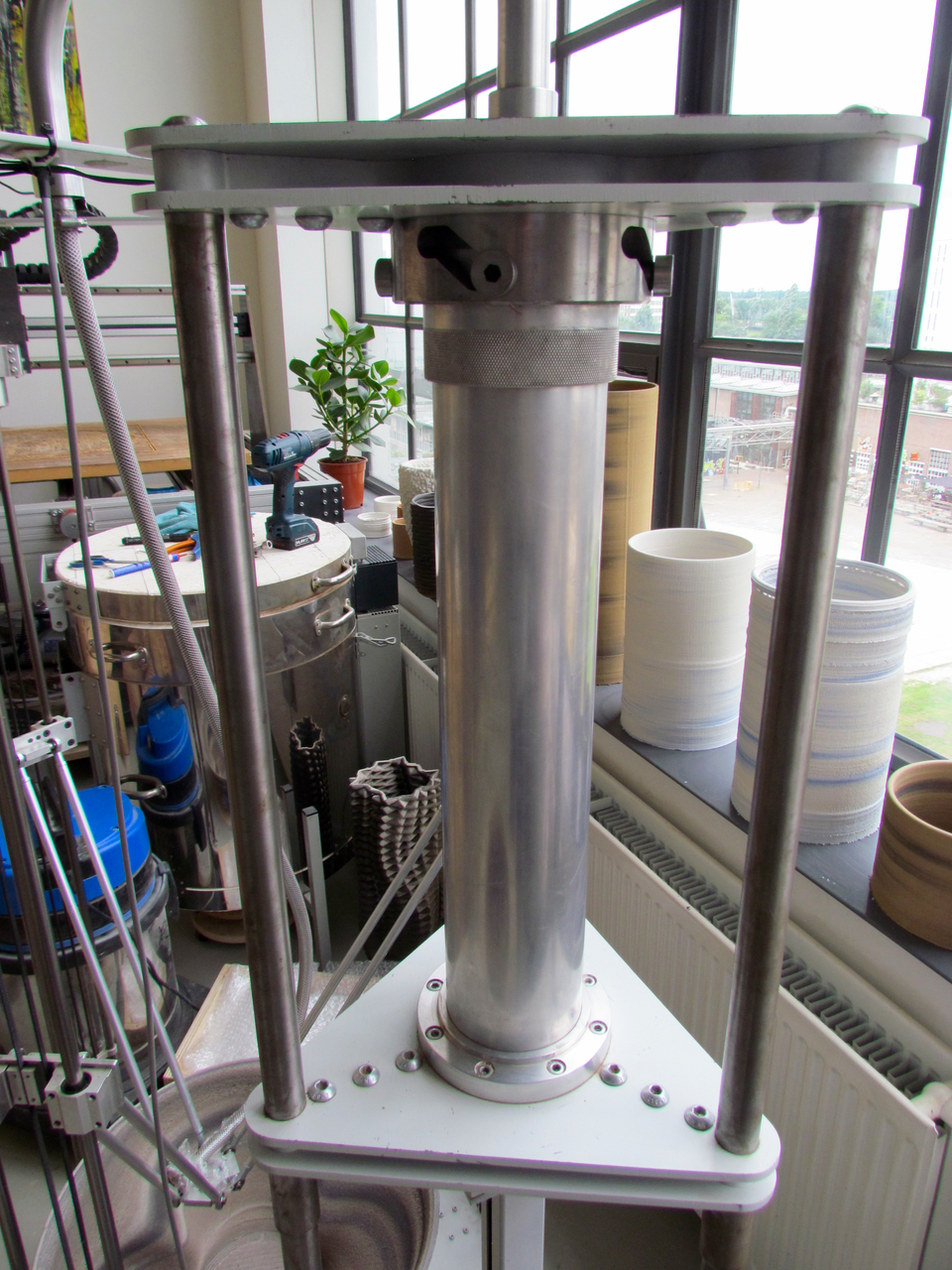
van Herpt designed a piston with a massive stepper motor that drives a gear to slowly push the hard clay through a steel-reinforced hose to the extrusion point. How strong is this piston mechanism? van Herpt told us the mechanism generates an astonishing 6,000kg of force to move the hard clay.
To put that in perspective, that’s like lifting 4.5 Toyota Prius automobiles ALL AT ONCE. This is an enormous amount of pressure, sufficient to accurately move the hard clay through the extrusion system.
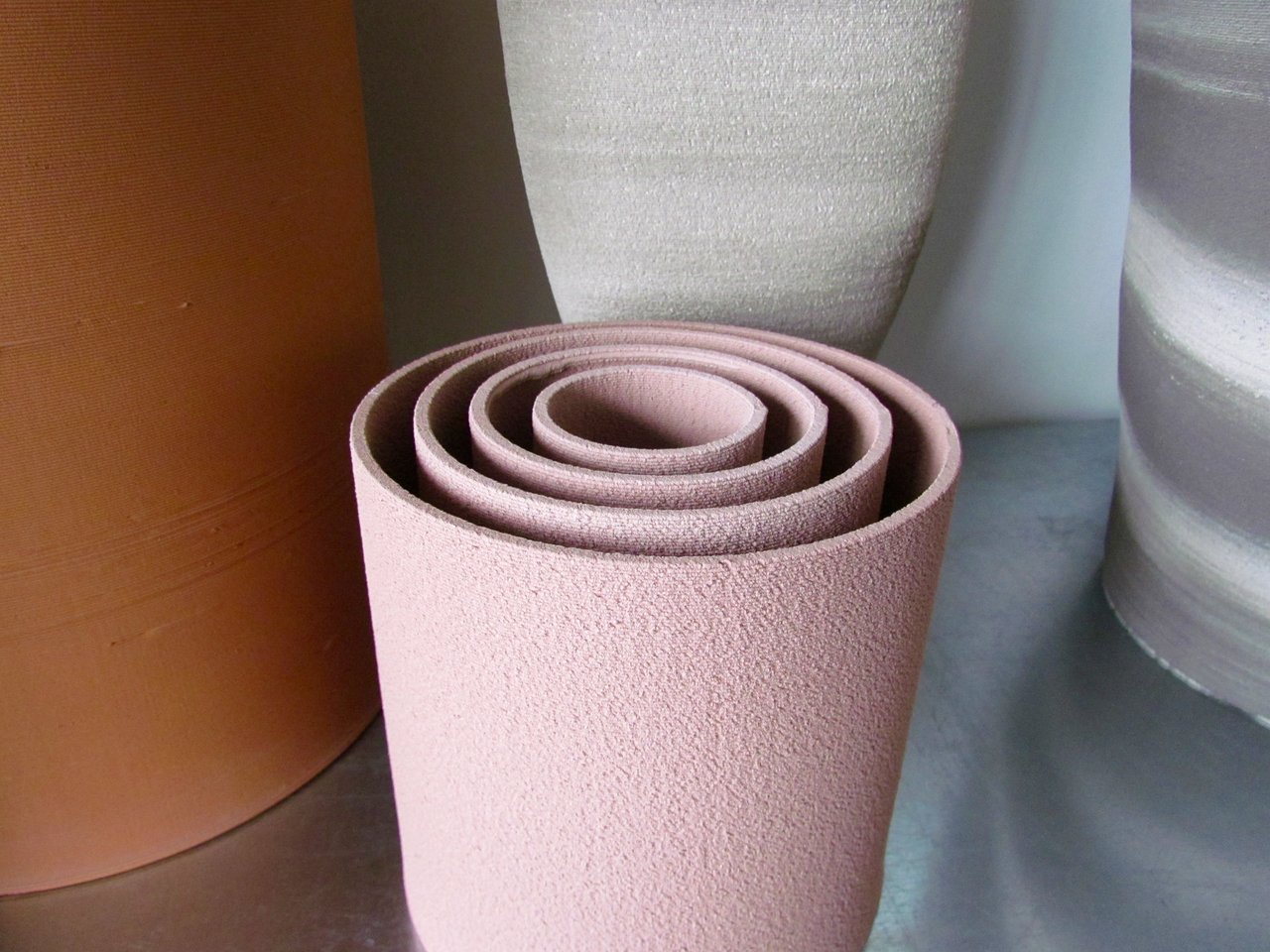
The resulting ceramic 3D printing system is quite capable of printing large relatively smooth – and large – vases in only an hour or two. The hard clay doesn’t slump, enabling the printing of much more complex objects. These prints are then dried for a couple of days and then fired in the usual manner to finish ceramics.
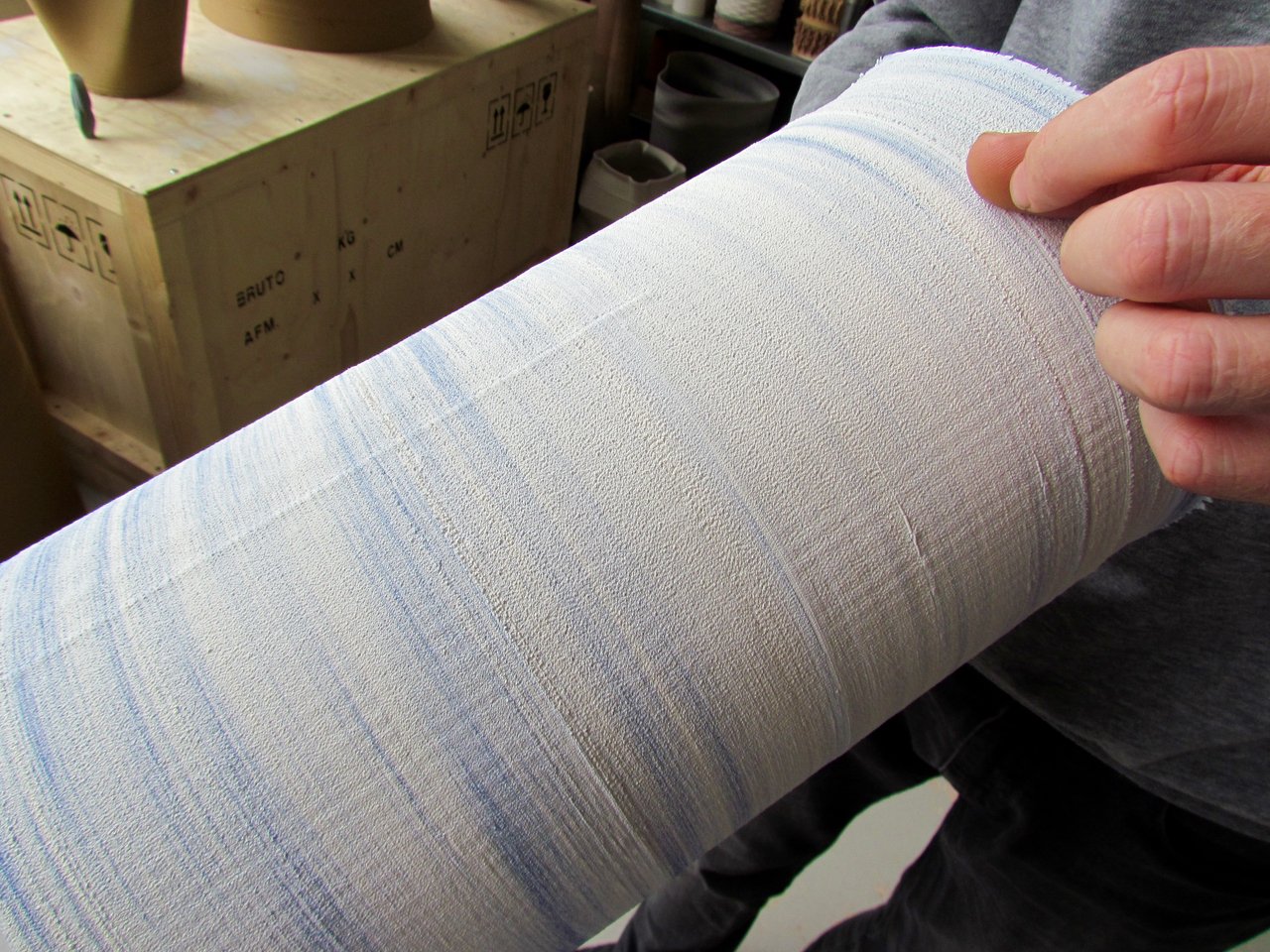
van Herpt explains that while many of his prints use a 1.0mm layer size for speed, the machine is also capable of printing much smaller layers, such as the 0.3mm layers shown here in a porcelain experiment. Of course, large prints typically do not require such precision.
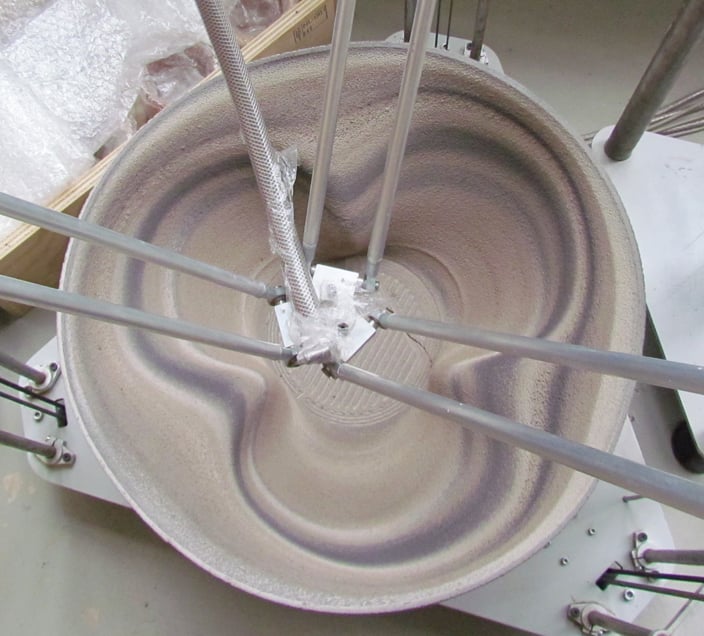
It’s also possible to change color patterns in the print by pre-mixing the clay as it’s loaded into the piston. Here you can see a partially printed vase with varying colors that are derived from the input clay itself.
van Herpt is developing a production version of the as-yet unnamed machine, but at the moment it’s only a prototype being beta tested. It’s my understanding that at least one will soon be acquired by a major company for testing.